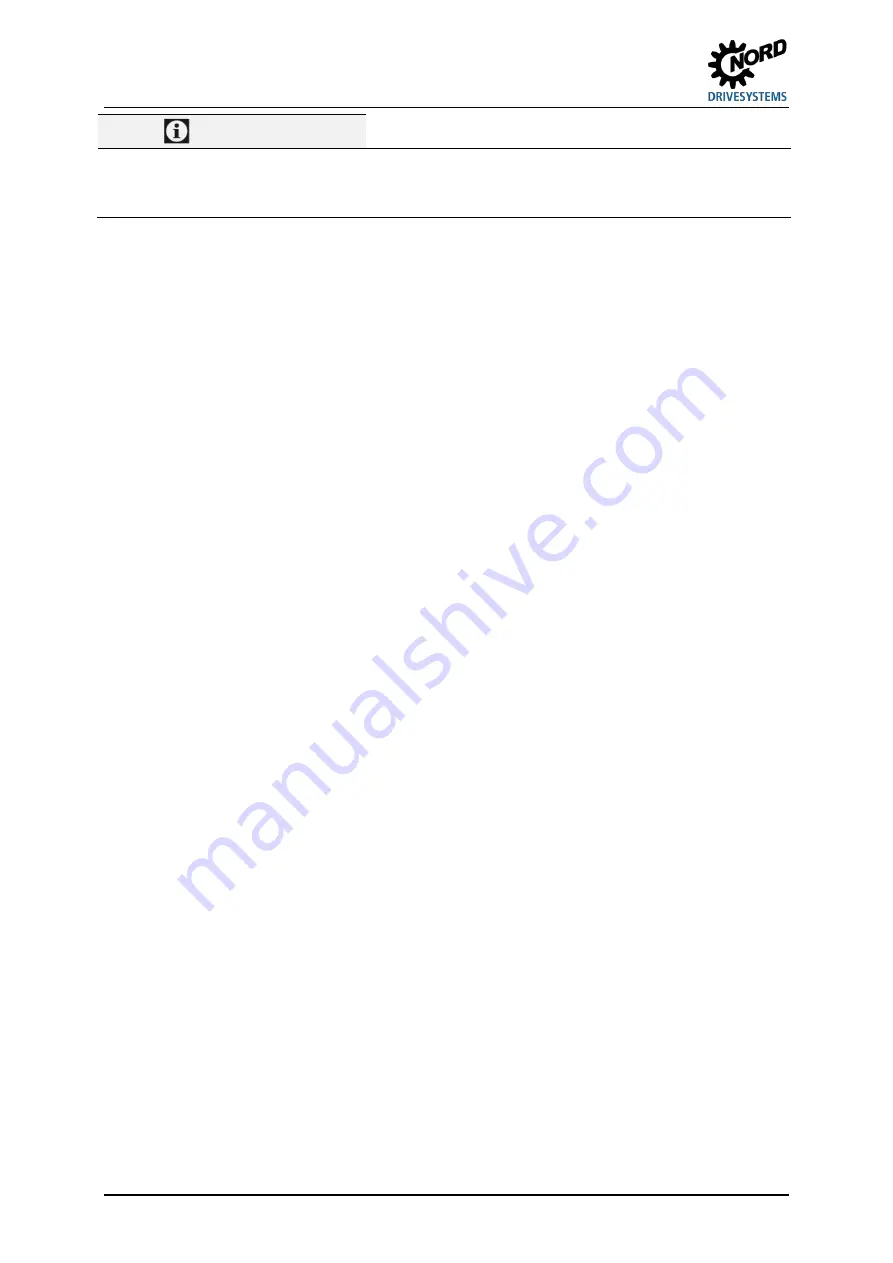
Industrial gear units – Operating and Assembly Instructions
28
B 1050 en-4419
Information
The service life of shafts, bearings and couplings depends on the precision of alignment of the shaft.
Therefore,
zero deviation
should always be aimed for in alignment. In this context, refer to the
special Operating Manuals regarding the requirements for the coupling, for example.
The base on which the gear unit is fitted must be vibration-free, torsionally rigid and flat.
The flatness of the bolting surface on the base must be of the appropriate precision (please see
chapter 7.5 "Tolerances for bolting surfaces").
Any contamination to the bolting surfaces of gear unit and base must be thoroughly removed.
The base must be designed according to the weight and torque, taking into account the forces acting
on the gear unit. Bases which are insufficiently rigid may lead to radial and axial displacement during
operation, which is not measurable when the unit is stopped.
When attaching the gear unit to a concrete base using masonry bolts or base blocks, appropriate
recesses must be provided in the base. Tensioning bars must be cast into the concrete base in their
aligned state.
Bolts with a minimum quality of 8.8 must be used to fasten the gear unit. The bolts must be tightened
to the correct torques (please see chapter 7.4 "Screw tightening torques").
The tolerances of the shaft ends and the flange connections should be obtained from the specific
dimension sheet for the order.
The gear housing must always be earthed.
Welding of the gear unit is prohibited. The gear unit must not be used as the earth connection for
welding work, as this may cause damage to the bearings and gear wheels.
Summary of Contents for B 1050
Page 1: ...B 1050 en Industrial gear units Operating and Assembly Instructions...
Page 2: ...Industrial gear units Operating and Assembly Instructions 2 B 1050 en 4419...
Page 6: ...Industrial gear units Operating and Assembly Instructions 6 B 1050 en 4419...
Page 83: ...7 Appendix B 1050 en 4419 83 Gear units SK 5207 SK 10507 M1 oil screw holes...
Page 85: ...7 Appendix B 1050 en 4419 85 Gear units SK 5207 SK 10507 M3 oil screw holes...
Page 87: ...7 Appendix B 1050 en 4419 87 Gear units SK 5207 SK 10507 M5 oil screw holes...
Page 89: ...7 Appendix B 1050 en 4419 89 Gear units SK 11207 SK 15507 M1 oil screw holes...
Page 91: ...7 Appendix B 1050 en 4419 91 Gear units SK 11207 SK 15507 M3 oil screw holes...
Page 93: ...7 Appendix B 1050 en 4419 93 Gear units SK 11207 SK 15507 M5 oil screw holes...
Page 95: ...7 Appendix B 1050 en 4419 95 Gear units SK 5217 SK 11217 M1 oil screw holes...
Page 97: ...7 Appendix B 1050 en 4419 97 Gear units SK 5217 SK 11217 M5 oil screw holes...
Page 112: ...6052902 4419...