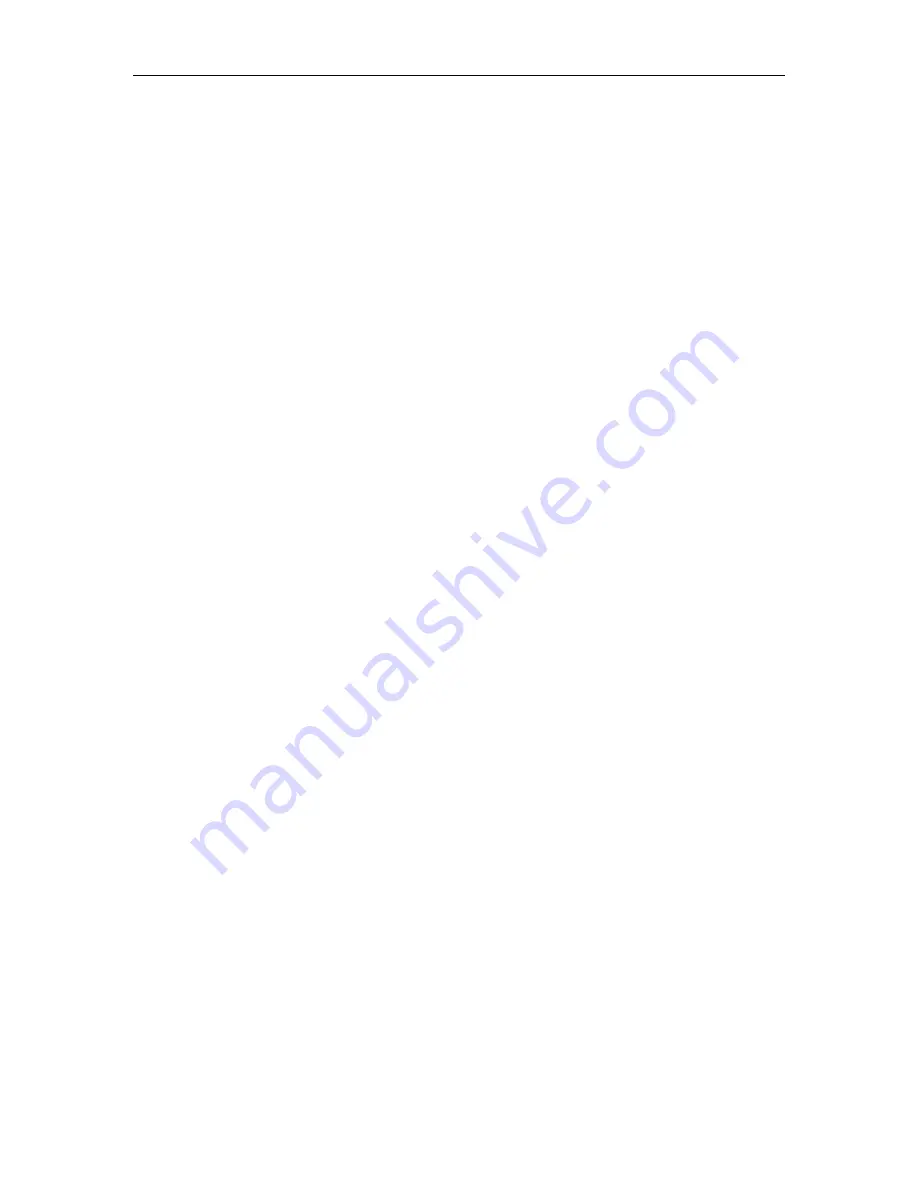
Smart Systems User’s Manual Version 1.1
63
This feature is useful for producing a continuous data image even if the system is
backed up during the survey line.
Note that it is not possible to back up and have the arrow indicator move more than one
screen.
The physical position corresponding to the Back-up arrow is the centre of the Noggin.
This position can be changed from the centre of the Noggin to any other position. See
Section 6.3.2 on changing the Arrow Offset value.
6.2.8
Calib. (Calibration) Menu
Noggin systems can be used to scan into many different materials including soil, rock,
concrete, snow, ice and wood. The radio wave emitted by a Noggin system will travel at
different velocities depending on the material being scanned. The depth value (see
Section 6.3.1) and on Depth Lines (see Section 6.2.4) are only accurate if the system
has been properly calibrated to determine the velocity of the material being scanned.
See Section 6.3.1 - Depth for more details about how depth is calculated.
The Calibration function is a tool for determining the velocity of the material being
scanned. A velocity value can be input directly (see Section 6.3.1 - Velocity) or
determined in one of two different ways depending on the situation:
1) Hyperbola
matching
2)
Target of known depth
Note that unlike the Calibration with Noggin systems (see Section 5.3.4), the
Noggin
plus
Calibration does NOT automatically update the velocity value in the
software. In the Noggin
plus
calibration, once a velocity is determined, the user
must enter it into the System Parameters (see Section 6.3.1 - Velocity).
Hyperbola Matching
This is the most accurate way of determining the velocity of the material being scanned
because it extracts the speed using data collected in the area. This method may not
work in all situations because it depends on having a good quality hyperbola (or inverted
U) in the data. A hyperbola is the characteristic Noggin response from a small point
target like a pipe, rock or even a tree root. If the hyperbola has long tails on it, we can
match the shape of the hyperbola and determine the velocity of the material in the area.
With the hyperbola visible on the DVL screen, select the hyperbola (
∩
) button. This will
superimpose a hyperbola on the data. This hyperbola can be moved up (
), down (
),
left (
) and right (
) using the appropriate arrow buttons. The goal is move the
hyperbola until it lies on top of the hyperbola in the data (see Figure 6-3). Then, the user
can adjust the width of the hyperbola to make it wider (
) or narrower (
) until the
shape of the hyperbola matches the shape of the hyperbola in the data. After matching
the hyperbola, the velocity value is displayed and now can be entered under the System
Parameters (see Section 6.3.1 –Velocity).
Pressing the up, down left, right, wider and narrow buttons once makes a very small