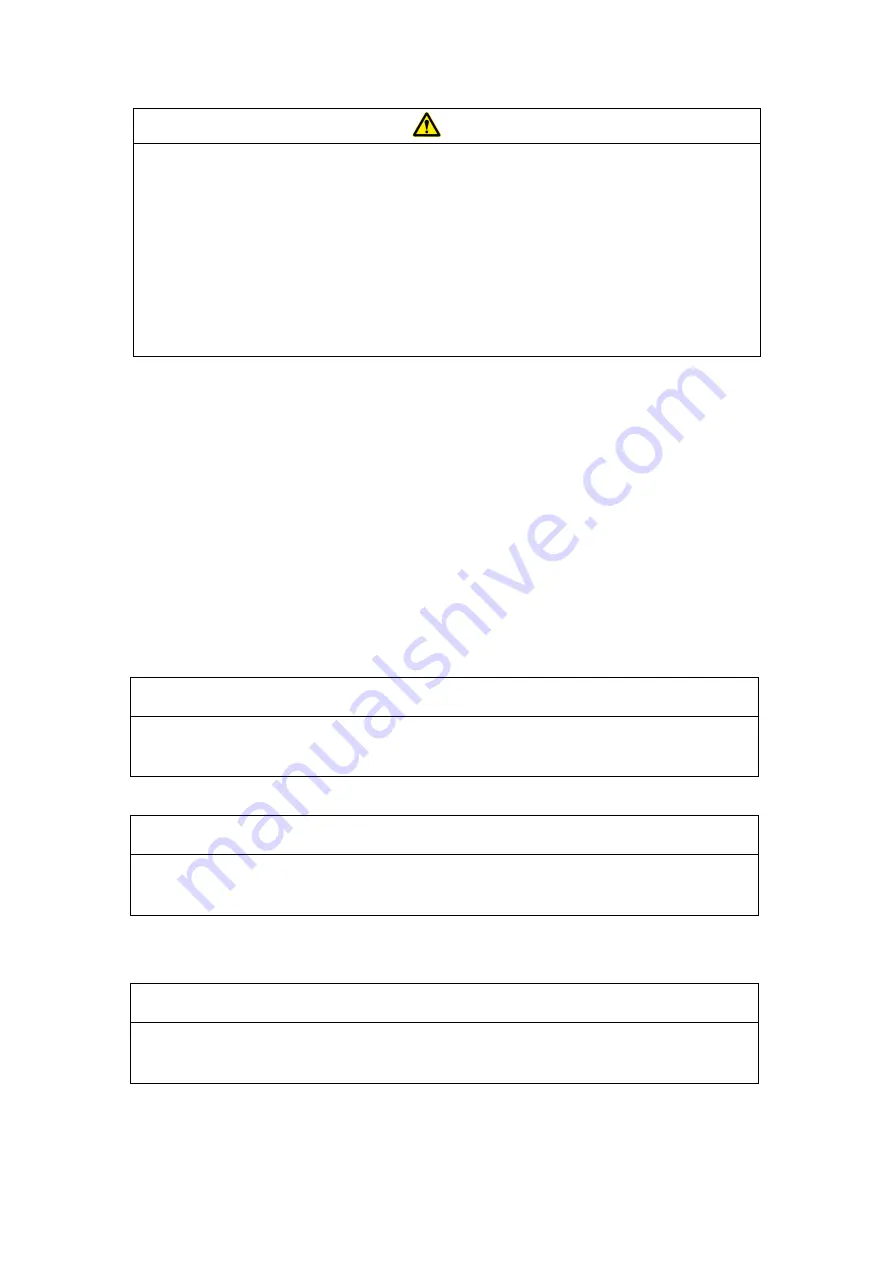
-15-
Warning
The fire pump room must have the following facilities:
1.
Ventilation facilities;
2.
Flood prevention and drainage facilities;
3.
Lighting facilities;
4.
Heating facilities must be installed in the low-temperature area of fire pump to ensure
that the pump temperature is not lower than 4℃;
5.
Fire extinguishing devices (e.g. dry chemical fire extinguishers).
3.1 On-site Installation
3.1.1 Location
The location of fire pump should be as close as possible to its water supply, the following
conditions should be met:
3.1.2 Foundation
The ground must be dry, flat and strong enough to support the weight of the equipment
without sinking by time.
3.1.3 Fire Pump Group Placement
The fire pump group shall be placed on a level ground with adequate open space. The
adjacent area around the fire pump group shall not stack any inflammable materials.
Note
Before changing position, the hatch door of the fire pump group must be shutdown and
kept shutdown during transportation or lowering.
Note
The fire pump group can work at a maximum angle of ±5 degrees, but the angle should
be maintained at ±2 degrees for optimum performance and reliability.
3.2 Fixing and concreting
Note
The fire pump group shall be fully fixed and a separate civil engineering solution shall be
implemented in accordance with local regulations.