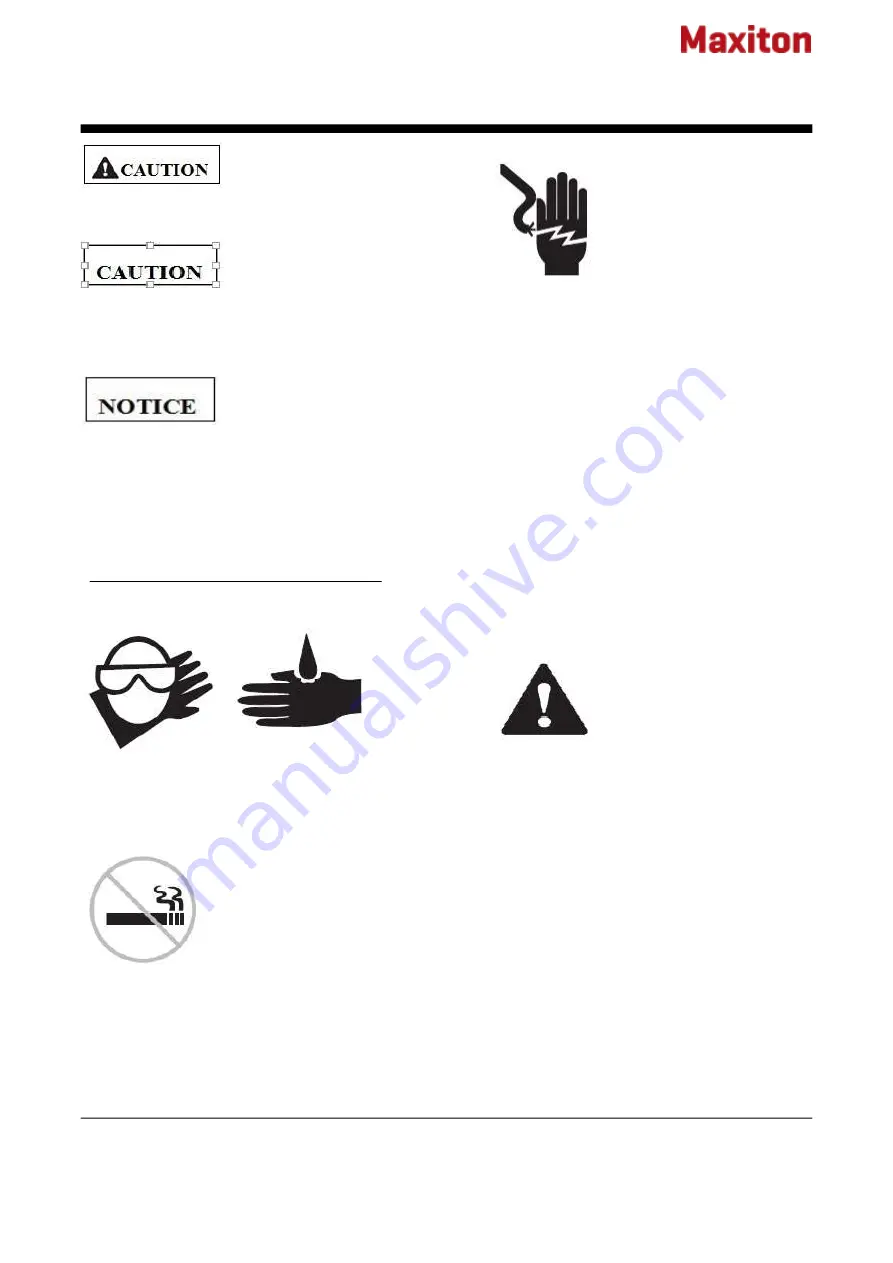
Operation and Maintenance Manual
Second Edition
A Brand of Niuli
6
MAXITON GTJZ
Yellow with safety alert symbol! used
to indicate the presence of a potentially hazardous situation
which, if not avoided, may cause minor or moderate injury.
Yellow
without safety alert
symbol!used to indicate the presence of a potentially
hazardous situation which, if not avoided, may result in
property damage.
Green!used to indicate operation or
maintenance information.
Battery Safety Burn Hazards
Batteries contain acid. Always wear protective clothing and
eyewear when working with batteries.
Avoid spilling or contacting battery acid. Neutralize battery
acid spills with baking soda and water. Do not expose the
batteries or the charger to water or rain during charging.
Explosion Hazards
Keep sparks, flames and lighted
tobacco away from batteries. Batteries
emit an explosive gas.
The battery tray should remain open
during the entire charging cycle.
Do not contact the battery terminals or the cable clamps with
tools that may cause sparks.
Component Damage Hazard
Do not use any battery charger greater than 24V to charge
the batteries.
Electrocution Hazards
Connect the battery charger to
a
grounded,
AC
3-wire
electrical outlet only. Inspect
daily for damaged cord, cables
and wires. Replace damaged
items before operating.
Avoid electrical shock from contact with battery
terminals. Remove all rings, watches and other
jewelry.
Tip-over Hazard
Do not use batteries that weigh less than the
original equipment. Batteries are used as
Counterweight and are critical to machine
stability Each battery must weigh 65 pounds / 28
kg.
Lifting Hazard
Use the appropriate number of people and proper
lifting techniques when lifting batteries.
Maintenance of Safety Rules
Danger
Failure to obey the instructions and safety rules in
this manual,
will result in death or serious injury.
Many of the hazards identified in the operator's
manual are also safety hazards when
maintenance and repair procedures are
performed.
Do Not Perform Maintenance
Unless:
➢
You are trained and qualified to perform
maintenance on this machine.
➢
You read, understand and obey: