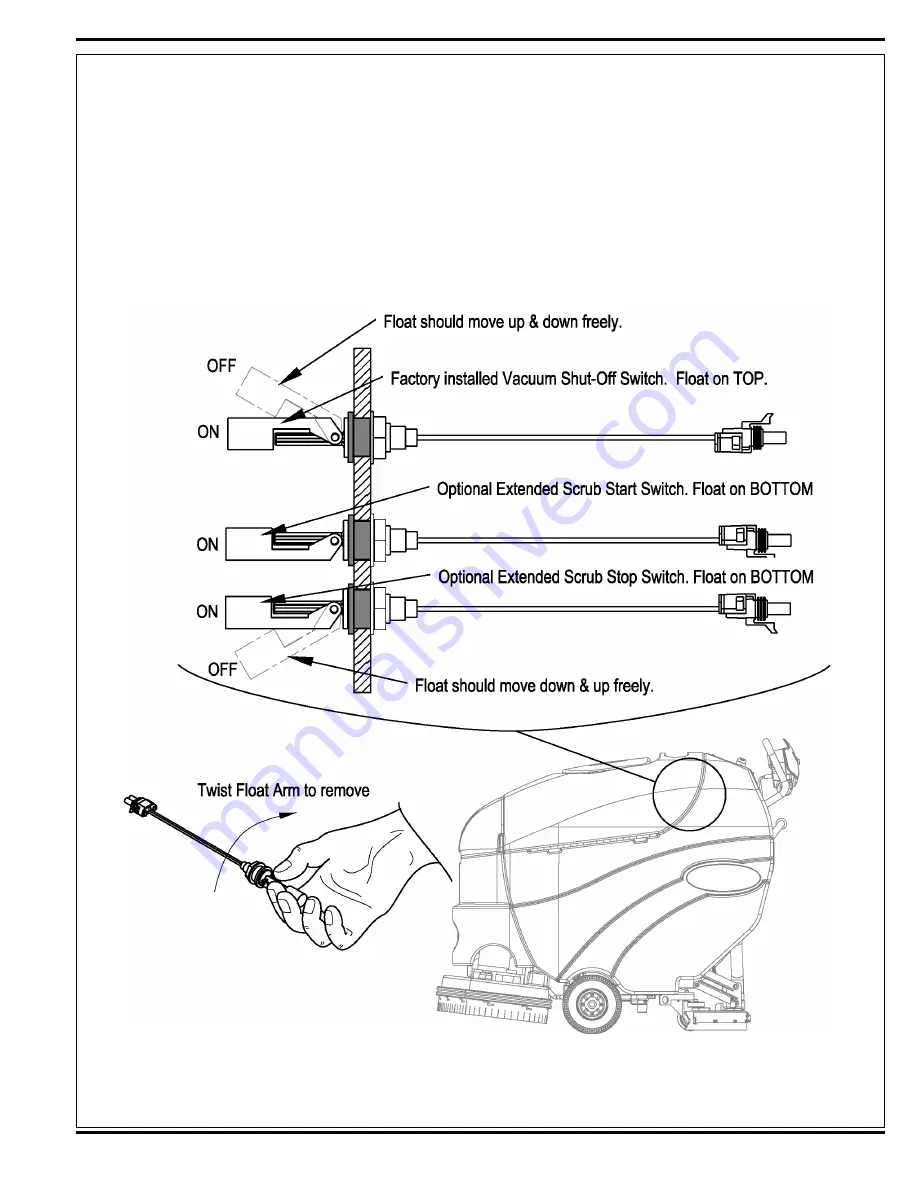
FORM NO. 56043098 - Convertamatic
™
24, 26, 28, 32 / BA 625, 725, 825 -
31
RECOVERY SYSTEM
MAINTENANCE OF RECOVERY TANK FLOAT SWITCHES
If the recovery tank
fl
oat switch(es) become dirty it can impair their proper operation. A dirty vacuum shut off switch can cause the vacuum motor to not function at
all or to not shut off when the tank is full. Dirty extended scrub system switches can prevent the optional extended scrub system from functioning properly.
If daily rinsing of the recovery tank does not suf
fi
ce to keep the switches clean you may need to remove the
fl
oat arms for cleaning. The
fl
oat arms can be removed
easily by grasping them as shown below and twisting to remove. It is very important that they be reassembled correctly in order to function. See
Figure 3
for the
correct orientation of the switch
fl
oat arms.
FIGURE 3
Summary of Contents for BA 625
Page 2: ......
Page 7: ...FORM NO 56043098 Convertamatic 24 26 28 32 BA 625 725 825 5 SPECIFICATIONS revised 5 07 ...
Page 25: ...FORM NO 56043098 Convertamatic 24 26 28 32 BA 625 725 825 23 FIGURE 2 SCRUB SYSTEM ...
Page 27: ...FORM NO 56043098 Convertamatic 24 26 28 32 BA 625 725 825 25 NOTES ...
Page 55: ...FORM NO 56043098 Convertamatic 24 26 28 32 BA 625 725 825 53 FIGURE 4 ...
Page 57: ...FORM NO 56043098 Convertamatic 24 26 28 32 BA 625 725 825 55 FIGURE 5 ELECTRICAL SYSTEM ...
Page 63: ...FORM NO 56043098 Convertamatic 24 26 28 32 BA 625 725 825 61 FIGURE 6 ELECTRICAL SYSTEM ...
Page 79: ...www nilfisk advance com 2008 ...