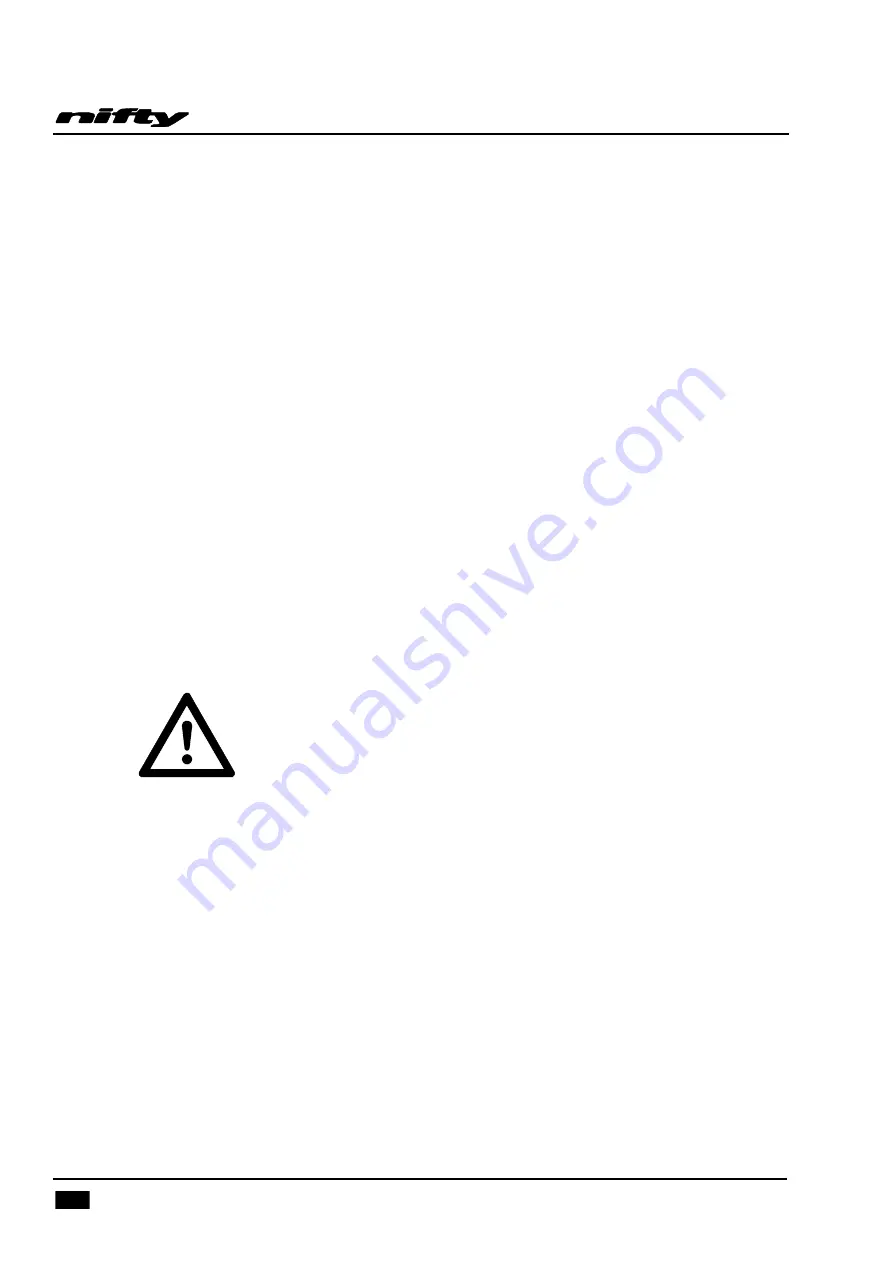
Height Rider/SP Series
Operating & Safety Instructions
English/USA – 07/17
Original instructions
36
EMERGENCY PROCEDURES
1)
Push in red emergency stop to shut down
all
machine movement.
2)
Release
both emergency stops to restore normal controls.
In the event that the controls fail or the cage overload is activated as described in Section 5.3, the
booms can be operated from the cage location as described below:
1)
Press
white override button
situated on the cage console. (Refer to Section 4.3.1)
If engine is running, it will stop. Override mode is for booms only and will not operate drive.
2)
Activate a
single
desired function paddle.
(Note: Multiple boom function is not available in override mode).
3)
If the cage has contacted a fixed object and cage overload has disabled the machine, move
machine slightly using steps 1-2. The overload alarm and visual warning will cease and
normal controls are available.
4)
Restart engine with selector switch.
5)
Use normal controls if available for the fastest recovery time. Press the green button or
footswitch and operate the desired function lever(s).
6)
If normal controls are not available, continue using the override button to lower the machine
using auxiliary power.
Note:
The override mode is for
booms only
and will not operate the drive function. If the engine is
running, it will stop once the override button is pressed.
4.3.6
SiOPS
TM
- LOAD SENSING CONSOLE
WHEN OPERATING THIS MACHINE THE USER MUST BE AWARE OF ANY
OVERHEAD OBSTRUCTIONS.
This machine incorporates a load sensing cage console that senses if the operator has been pushed or
has fallen against the console. If the load applied to the front of the console is greater than the pre-
determined amount, the footswitch will be disabled to increase operator safety and reduce the
possibility of sustained involuntary operation of the cage controls.
Note
: The green button will illuminate once the footswitch has been disabled, but continues to be
available for use at all times. This allows the operator to use the cage control functions and
manoeuvre the machine to a safe position. If cage overload has also activated, the procedure
described in Section 4.3.4, ‘Emergency Procedures’ (above) should be followed first.
To reset the footswitch and normal controls:
1)
Release the load from the front of the console.
2)
Ensure cage controls are in the neutral position and clear of objects.
3)
Raise foot clear of footswitch then lower foot onto footswitch to reactivate.
Note:
If SiOPS
TM
has been activated and the footswitch is not reset within
15 seconds
, then the blue
warning beacon will flash (located on underside of the cage) and a warning announcement will
sound until the footswitch is reset as described previously.
Summary of Contents for HR21 4x4
Page 79: ......