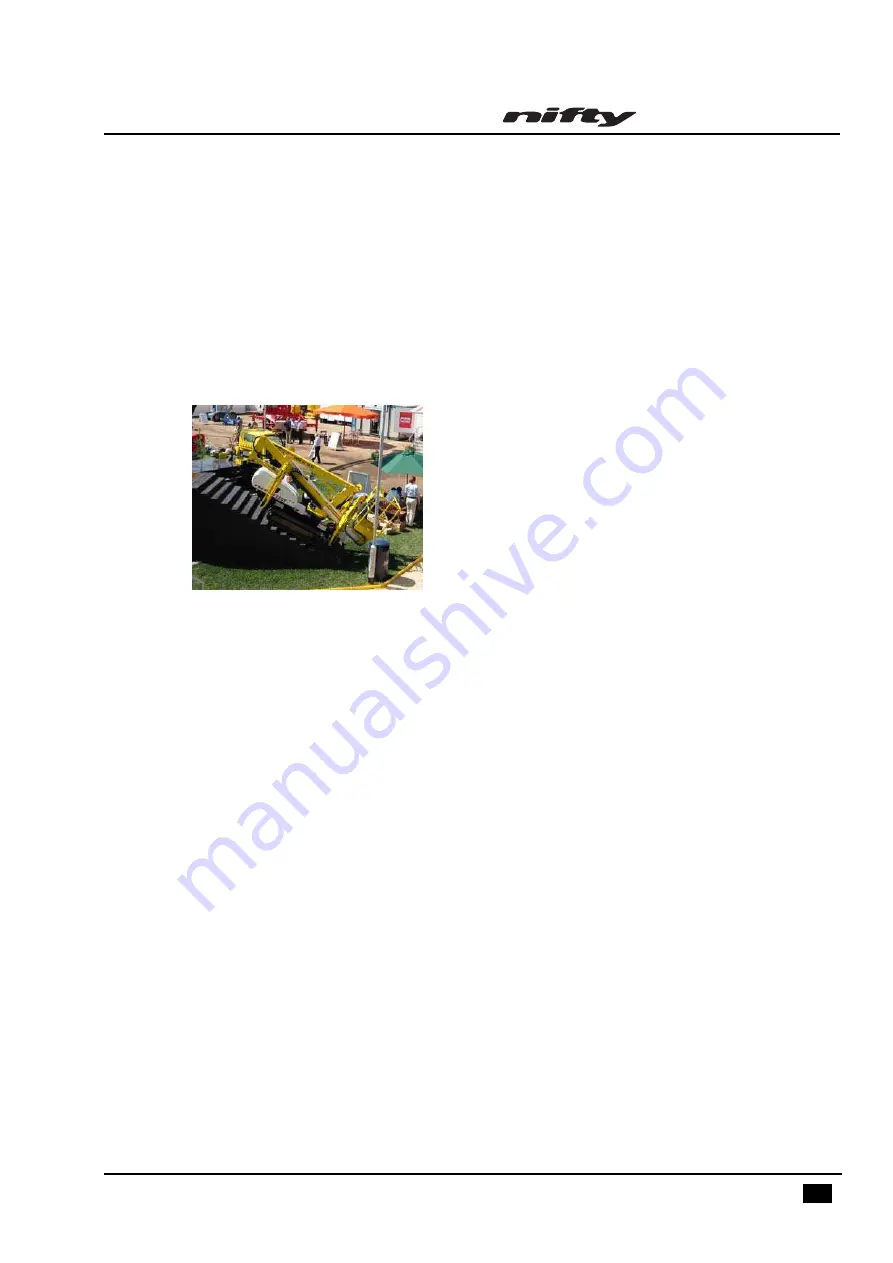
TrackDrive (TD) Series
Operating & Safety Instructions
English/USA 12/09
21
When climbing steps, a further judgement will be needed as to whether the weight of the machine, or
the traction required to climb or descend would cause damage. Many domestic installations feature
soft edge strips or boards to provide the front edge of the step. These edging strips are unlikely to
tolerate the action of climbing and might detach causing degradation of the steps themselves. More
importantly, the edge reliability is critical to the tractive effort and if less than adequate might cause the
machine to ‘slew’ sideways on a step rather than climb. The risks to the operator are obvious, whether
in the platform or driving from the side. A stair built from flagstones or loose blocks is not likely to
support the weight or accept the track movement over it. Loose ramps or ply sheets to spread the
track forces can be used, but again must be securely anchored to prevent the tracks from ‘gripping’ the
surface and shooting the boards out from under the machine.
The single greatest factor affecting the ability of the Track Drive
TD150T to attack any slope, incline or stair is
traction.
If there is inadequate adhesion between the tracks and the
surface to which the machine is presented
it will not climb
.
Driving across a slope is not recommended, but if this unavoidable then the outriggers legs can be
used, if space permits. Deploying the downhill legs gives the operator a further protection against
toppling, but with the additional risk of damage to the machine. Better safe than sorry.
4.1.5 VARIABLE
WIDTH
TRACK OPTION (if fitted)
It is recommended that whenever the machine is driven across a slope, or for added safety when
climbing or descending, the tracks should be extended to their maximum width. To achieve this, the
platform selector switch is left in the ‘Track Drive’ position, (i.e. to the right). Then using the variable
width toggle switch with the green button, the tracks will extend to their maximum width and stay in
this position. To change back to minimum travelling width, the toggle switch can be used in the
reverse direction, again in conjunction with the green button. When minimum width is achieved, the
tracks will again stay at this width. The Operator should make any adjacent personnel aware of the
machine operation, particularly in respect of the extending tracks, and ensure that no one is close
enough to the machine when the tracks are moving in or out. If a track ‘digs in’ whilst changing width
the machine can slew slightly along its length and could cause injury.
Summary of Contents for TrackDrive TD150T Series
Page 2: ...Courtesy of Crane Market...