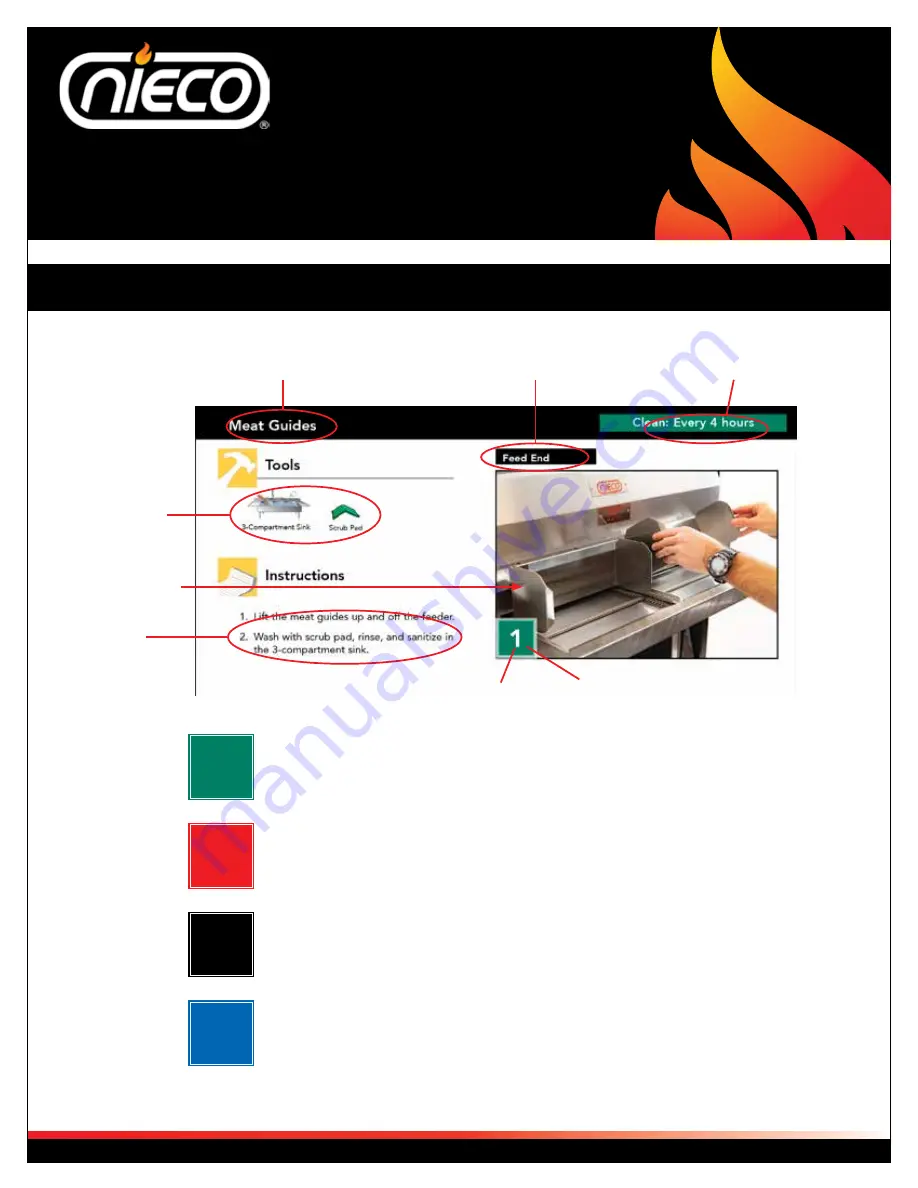
20
Model FH94 Electric
III. OPERATION
FH94E
How To Read The Cleaning Section
Every 4 Hours
Daily
Weekly
Monthly
The location of the part
When to clean the part
Picture of the part to be
removed and cleaned
How to remove and
clean the parts
The tools needed
to clean the part
The name of the part to be cleaned
Step in Cleaning Chart
Frequency Color Code
Cleaning & Disassembly Guide