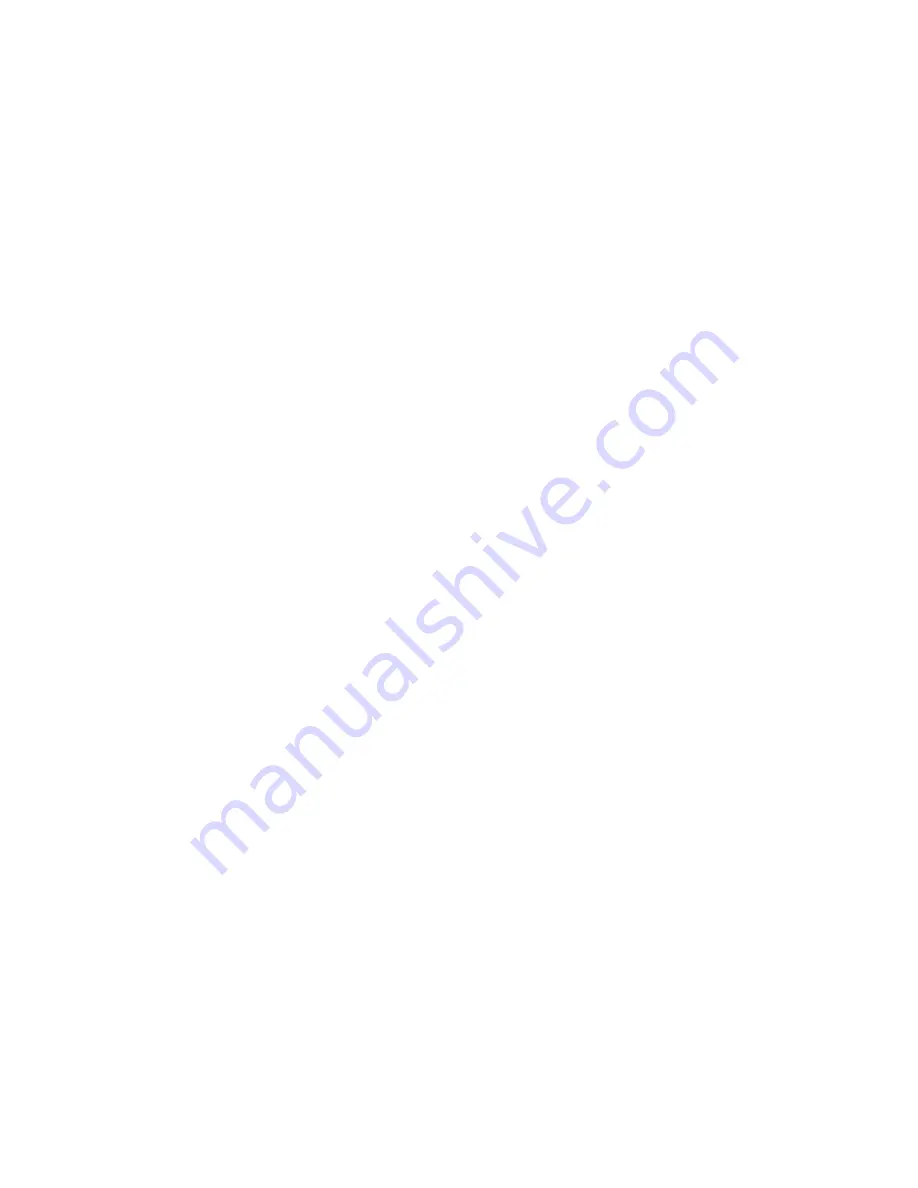
9
AUTOMATIC TEMPERATURE CONTROL (ATC)
The Nieco Automatic Temperature Control (ATC) is a system that operates the broiler at two different
energy input rates; a high energy input for initial warm-up and periods of high volume, and low energy for
regular operation. This dual input rate and the ATC allow the broiler to operate at a very consistent tem-
perature throughout the day and thus provide a very consistently broiled product. Since the broiler will
remain on the lower input rate (low gas) most of the day, a substantial energy savings is realized.
The ATC consists of two gas pressure regulators piped in parallel, a solenoid valve in series with the
high gas pressure regulator, a probe to sense the temperature at the loading end of the broiler, and a
control unit which is operated by the signals from the probe. The control unit causes the solenoid valve to
open and close. When the valve is open, the machine is in high gas mode, and the gas pressure is
increased to heat up the broiler.
Under heavy product loads, the temperature sensed by the ATC probe will drop low enough to cause the
ATC to open the solenoid valve. When the solenoid valve opens, the amber indicator light on the control
panel will light. The ATC will keep the broiler on high pressure until the temperature sensed by the probe
returns to the calibrated setting.
CALIBRATING THE ATC
1. Loosen the control knob lock screw and set the ATC control knob to 600° F.
2. Turn on the Main Power Switch.
3. Turn on the Motor Power Switch.
4. Light the broiler following the procedure in this manual.
5. The broiler should be in high gas mode at this time. (Amber light on.)
6. When the broiler reaches 600°, the high gas will shut off, and the broiler will be in low gas.
7. 40 minutes after lighting the broiler, slowly turn the ATC control knob up (clockwise) until
the high gas clicks on. This is the idle temperature of the broiler.
8. As soon as the high gas turns on, slowly turn the ATC down (counter clockwise) 10° to 20°
below the point where the high gas turns on.
9. Tighten the control knob lock screw to prevent accidental movement.
10. The control knob setting may need a minor adjustment on the first day of use, in order to
maintain 10° to 20° below the normal idle temperature. Once the adjustment is correct, it
need not change from day to day unless the broiler operating conditions change.
WARNING
Never set the ATC control knob at a setting high enough to keep the broiler in high gas pressure. The
machine may be damaged, energy costs will be much higher, and some broiler parts may wear out pre-
maturely.
MEAT HOLDING SECTION
The Models 732/735, 532/535, 522 are equipped with a temperature controlled meat holding area
beneath the cooking chamber. Finished product automatically slides into the holding area after cooking.
Cooking guidelines call for a holding temperature of 155°, and a maximum holding time of ten minutes.
The temperature of the holding area can be adjusted for proper performance. Use a setting of 200° F to
start, and adjust as necessary.
Summary of Contents for 522G
Page 10: ...10 D PARTS AND LOCATION Model 732 735 Gas Feed End View...
Page 11: ...11 Model 732 735 Gas Right Side View...
Page 12: ...12 Model 732 735 Gas Left Side View...
Page 15: ...15 Model 532 535 Gas Left Side View...
Page 30: ...30 J WIRING DIAGRAM Models 732 735 532 535G Domestic U S A...
Page 31: ...31 Models 732 735 532 535G International Export Models...
Page 32: ...32 Model 522G Domestic U S A...