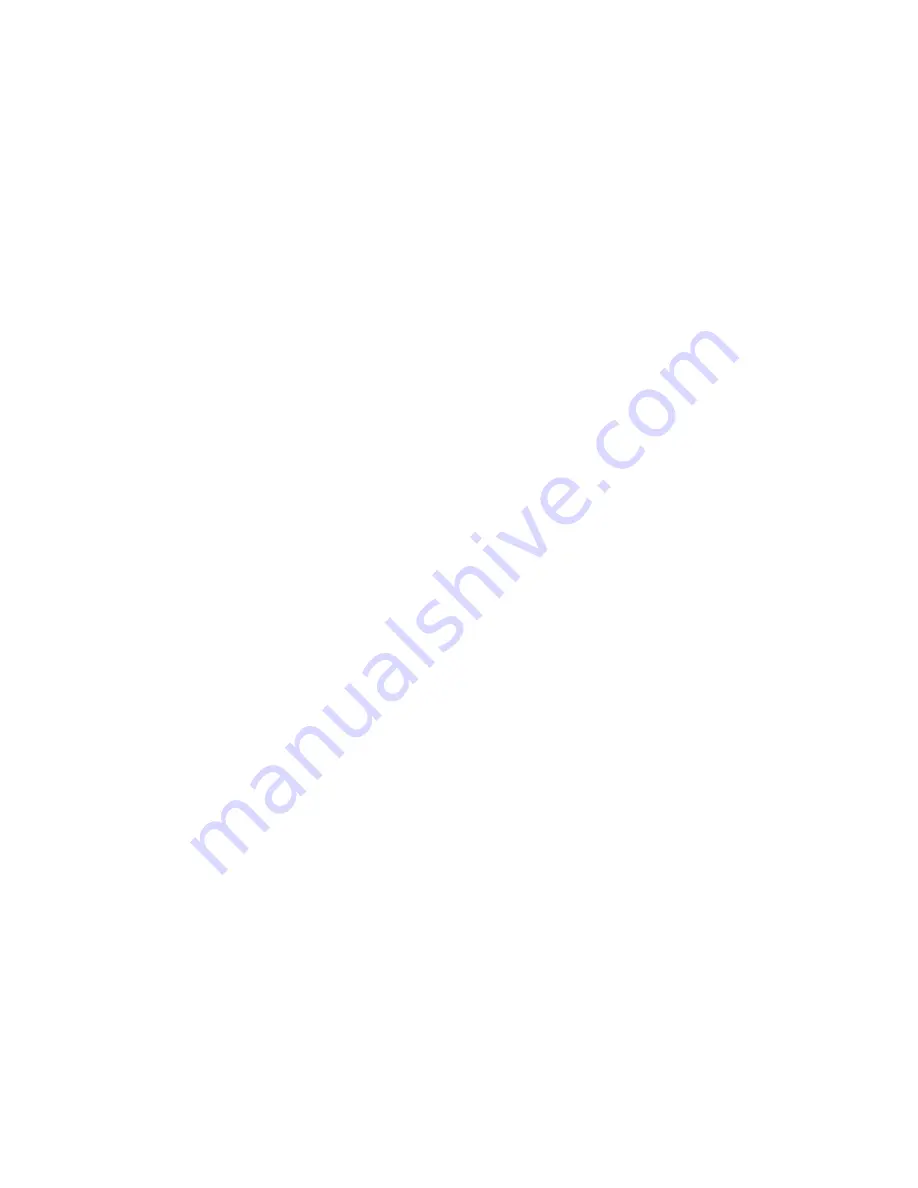
Page 38
Install the Bottom-Half of the Bearing Liners on the
Opposite-Drive-End Side:
1. Lift the shaft up slightly (about 0.005 inch) on both ends of the
rotor to the point where shaft and bottom half of the liner do not
touch each other.
2. Make sure the surfaces are clean. Apply STP® Oil Treatment
over the running surface on shaft where the liner will sit.
3. Set the liner on the shaft so it rests on the housing. Use eyebolts
for lifting. The ID numbers on the lining face outward.
4. Remove the lifting eyes from the liner. Move the rotor gently
from side to side and up and down as necessary, and slide the
liner down into the housing. If the liner doesn’t turn easily, check
the position of the shaft and the alignment of the housing.
5. Lower the shaft onto the liner.
Install the Top Half of the Bearing Liner on the Drive
End Side:
1. Apply STP® Oil Treatment on the running surface of the shaft
where the top half of the liner will sit.
2. After making sure the engraved numbers on the top and bottom
halves correspond and are on the same side, place the top liner
over the bottom liner.
3. Put Loctite® 242 on the split line screws, insert the screws, and
tighten.
Install the Top Bearing Housings:
1. Apply STP® Oil Treatment on the top of the bearing liner.
2. Spread Loctite® 587 Blue on the bottom housing where it will
mate with the top housing.
3. Put the top housing in place, making sure the dowel pin in the
inside diameter of the top housing lines up with the pin hole in
the bearing liner. Put Loctite® 242 on the split lines screws, and
fasten the housings together, leaving the screws snug but not
tight.
Torque the split line screws to 1100 ft-lbs.
Install the Seal Carrier Assemblies:
1. Cut the gasket, if necessary to fit it over the shaft. Coat it with
Loctite® Hi-Tack gasket sealant or equivalent, and fit it over the
shaft.
2. Attach the gap seal and labyrinth seal with the labyrinth seal
nearest the bearings. Put the two halves of the seals together,
and slip the garter springs around the seals to fasten them. (The
outside seal carrier on the drive end side only gets a labyrinth
seal.)
3. Put Curil T Sealant on the inside diameter of the seal carriers
where they will contact the seals, (one bead in the narrow
(inside) groove and one bead in each of the three wider (outside)
grooves. Also put Curil T Sealant on the surface of the labyrinth
seal on both sides of the spring.
Summary of Contents for 4P10
Page 8: ...Page 8...