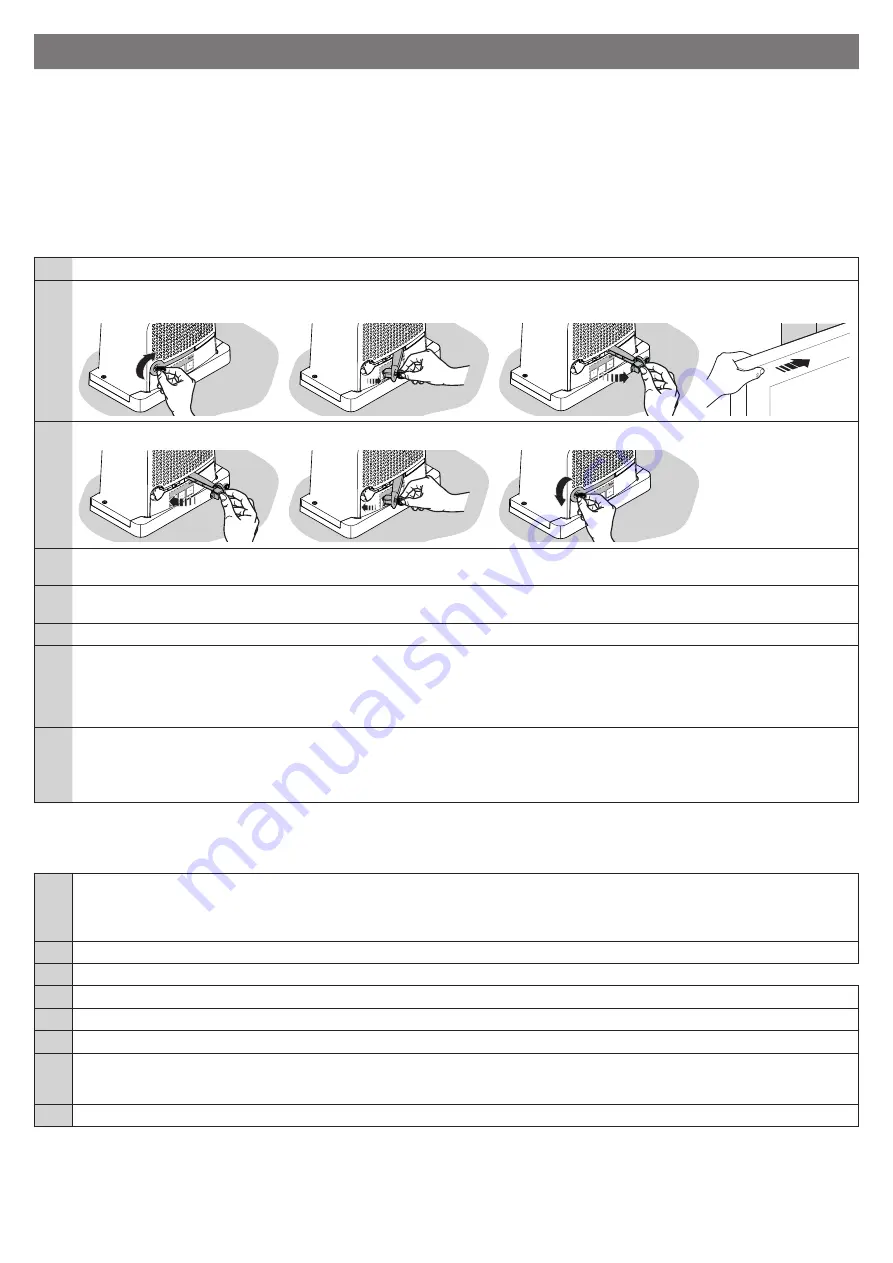
14
–
English
6
TESTING AND COMMISSIONING
These are the most important phases in automating the gate and ensuring maximum system safety.
They must be carried out by qualified and expert personnel that must decide on the tests required to verify the solutions adopted with regard to
the risks present and the compliance with laws, directives and regulations; in particular, all the requirements of the EN 13241-1 and EN 12453
standards.
The additional devices must undergo a specific test with regard to both their functions and interaction with ROBO: please refer to the instruction
manuals of the individual devices.
6.1 - Testing
The testing procedure can also be performed as a periodic check of the automation devices. Each component of the system (sensitive edges,
photocells, emergency stop, etc.) requires a specific testing phase. To do so, follow the procedures given in the instruction manuals.
Run the test as follows:
01.
Ensure that all specifications in chapter 1 “WARNINGS” have been observed in full
02.
Unlock the gearmotor and verify whether it is possible to manually move the gate open and closed with a force no greater than the value
shown in “Table 1 – Essential characteristics”
Pe
r S
bloc
car
e -
Po
ur
déb
ray
er
- To u
nbl
ock
Um
zu
ent
rie
gel
n -
Pa
ra
des
bloq
uea
r
Od
blo
kow
ani
e -
Om
te
deb
lok
ker
en
-
Отп
ере
ть
2
3
1
Pe
r S
blo
cca
re
- P
our
dé
bra
yer
- T
o u
nbloc
k
Um
zu
ent
rie
gel
n -
Pa
ra
des
blo
que
ar
Odb
lok
ow
ani
e -
Om
te
deb
lok
ker
en
-
Отп
ере
ть
2
3
1
Pe
r S
blo
cca
re
- P
our
dé
bra
yer
- T
o u
nbl
ock
Um
zu
en
trie
gel
n -
Pa
ra
des
blo
que
ar
Od
blo
kow
ani
e -
Om
te
deb
lok
ker
en
-
Отп
ере
ть
2
3
1
03.
Lock the gearmotor
Pe
r S
blo
cca
re
- P
our
dé
bra
yer
- T
o u
nbl
ock
Um
zu
en
trie
gel
n -
Pa
ra
des
blo
que
ar
Od
blo
kow
ani
e -
Om
te
deb
lok
ker
en
-
Отп
ере
ть
2
3
1
Pe
r S
blo
cca
re
- P
our
dé
bra
yer
- T
o u
nbloc
k
Um
zu
ent
rie
gel
n -
Pa
ra
des
blo
que
ar
Odb
lok
ow
ani
e -
Om
te
deb
lok
ker
en
-
Отп
ере
ть
2
3
1
Pe
r S
blo
cca
re
- P
our
dé
bra
yer
- T
o u
nbl
ock
Um
zu
en
trie
gel
n -
Pa
ra
des
bloq
uea
r
Od
blo
kow
ani
e -
Om
te
deb
lokk
ere
n -
Отп
ере
ть
2
3
1
04.
Using the key switch, control key or radio transmitter, test the opening and closing of the gate and make sure that it moves in the
intended direction
05.
The test should be carried out a number of times to make sure that the gate moves smoothly, that there are no points of excessive
friction and that there are no defects in the assembly or adjustments
06.
Check the operation of the safety equipment, one by one (photocells, sensitive edges, etc.)
07.
Check the operation of the photocells and any interference with other equipment:
1 - pass a dia. 5 cm length 30 cm cylinder along the optical axis, first close to the TX, then close to the RX
2 - check that the photocells trip in any condition, switching from active to alarm and back
3 - check that tripping the photocell results in the intended response of the control unit: e.g., when tripped during a closing stroke, the gate
changes direction
08.
If the dangerous situations caused by the movement of the door have been safeguarded by limiting the force impact, the user must
measure the impact force according to the EN 12453 standard.
If the adjustment of the “force” is used to assist the system for the reduction of the impact force, try to find the adjustment that gives
the best results.
6.2 - Commissioning
Commissioning can take place only after all testing phases have been terminated successfully (par. 6.1).
Partial or “makeshift” commissioning is strictly prohibited.
01.
Create and store (for minimum 10 years) the technical dossier of the automation that must include: overall design of the automation,
diagram of the electrical connections, risk assessment and relative solutions adopted, declaration of conformity of the manufacturer of
all the devices used (for ROBO use the attached CE Declaration of conformity); copy of the user instruction manual and
the automation maintenance plan
02.
Using the key switch or radio transmitter, test the opening and closing of the gate and make sure that it moves in the intended direction
03.
Prepare the declaration of conformity of the automation system and deliver it to the owner.
04.
Give the owner the user manual (tearout insert)
05.
Prepare and give the owner the maintenance schedule
06.
Prepare and give the owner the maintenance schedule
07.
The force adjustment is an important safety aspect and must be done with care by an expert technician.
Important!
- Adjust the force
to enable the gate to move as intended; higher forces than this can cause injury to animals and persons or damage to property if the
gate collides with an obstacle
08.
Before commissioning the gate, inform the owner in writing about the attendant residual risks.
Summary of Contents for ROBO600
Page 1: ...EN Instructions and warnings for installation For sliding gates Nice ROBO600...
Page 2: ......
Page 30: ...28 English NOTE...
Page 31: ...English 29...