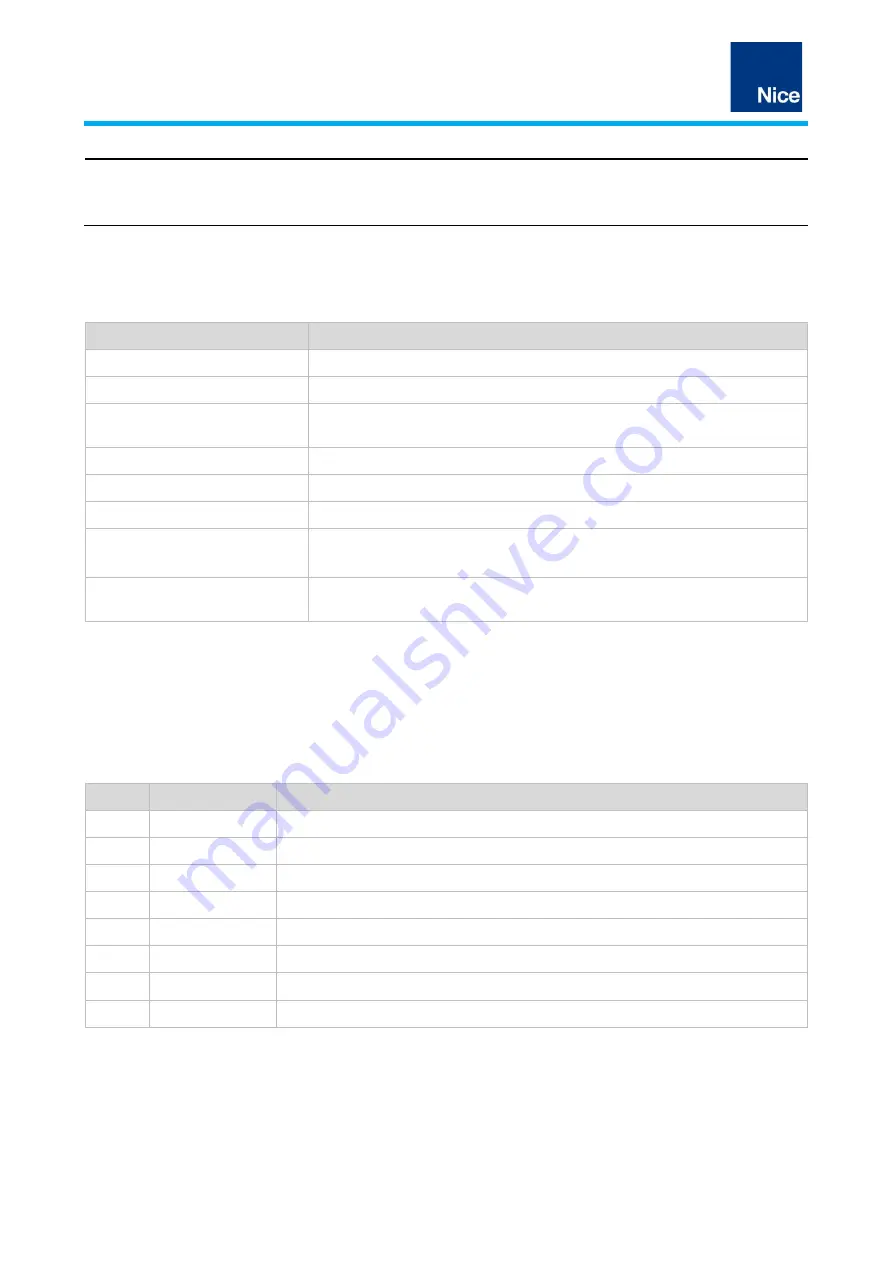
LP21/LP22
Pag.
19
a
37
LP21/LP22 Installation instructions en
Sensors
NOTE
LED position
The LEDs for the loop channel 1 are located at the top or side of the device, for loop channel 2 are in the
middle.
8.2
DIP switch settings
Function
Description
Sensitivity
Switch-on threshold for signal output when the loop is covered
Frequency level
Frequency of the loop resonant circuit in two levels
Hold Time until readjustment
Maximum duration of the output signal until automatic frequency
adjustment of the loop channel
Output signal 2 mode
Switching between continuous signal and pulse signal at output 2
Time of output signal 2
Time of output signal for activated pulse signal on output 2
Output signal inversion
Reversing the switching logic for the output signals (inversion)
Direction detection
Switching between presence and direction detection for both outputs
(2 channel variant LP22)
Direction logic
Evaluation logic of the direction of travel when loop is covered according
to the specific application (read the operating instructions!)
Tab.7: Description of the settings
8.2.1
DIP switch assignment of the LP21 variants
The single-channel variants have an 8-pole DIP switch for configuring the detector.
DIP
Designation
Function
1
Sense a
Loop 1 sensitivity
2
Sense b
Loop 1 sensitivity
3
Frequency
Frequency step
4
Hold time
Hold time until readjustment
5
Output 2
Output signal 2 mode
6
Edge 2
Output signal 2 time
7
Inv. Out 1
Output signal 1 inversion
8
Inv. Out 2
Output signal 2 inversion
Tab.8: DIP switch assignment (default)