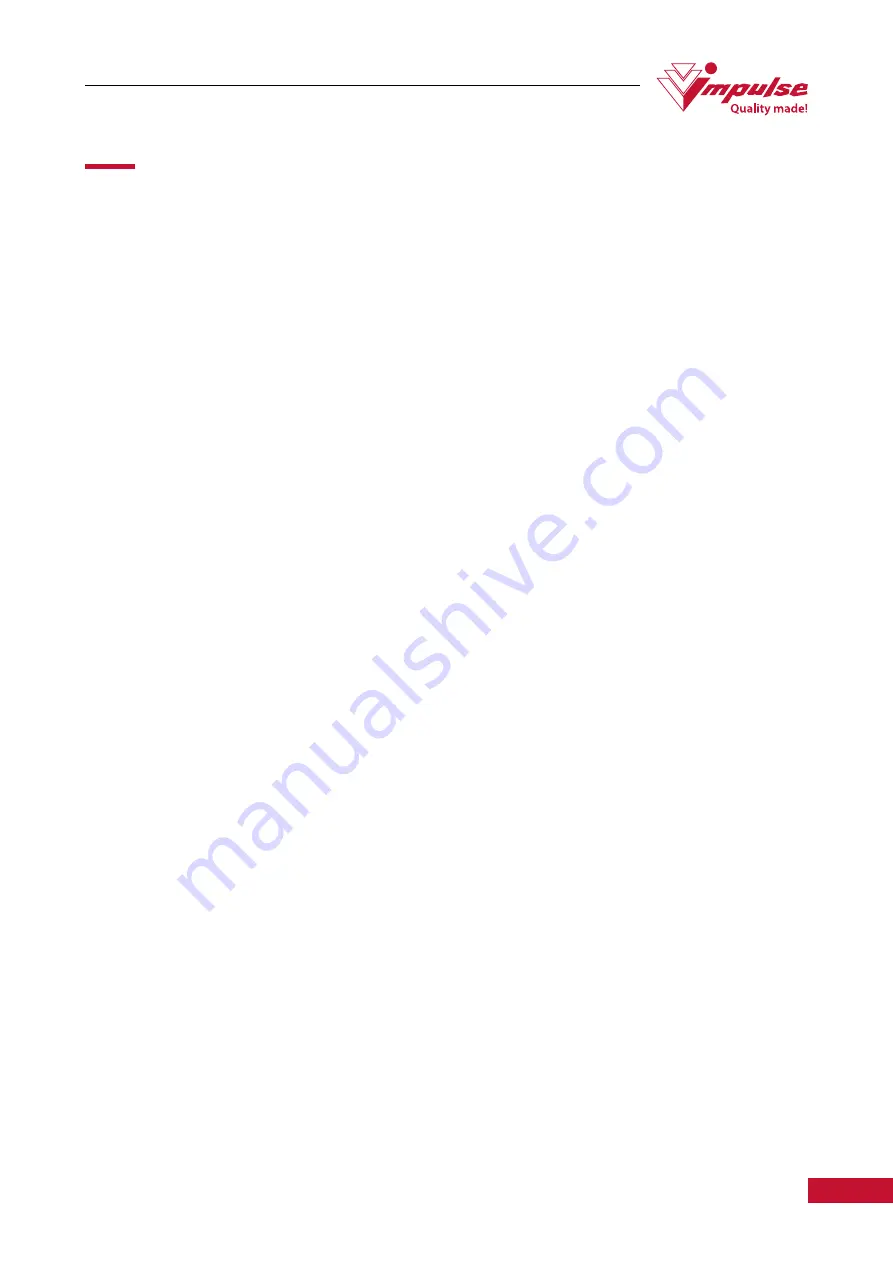
35
11
WARRANTY
The manufacturer guarantees performance of the hydraulic breaker for 36 months from sale
date, but no longer than 1500 operating hours if all operating rules are adhered to. Warranty for
the breakers housing, fasteners (screw bolts, bolts, nuts and washers), seals, including rings is 6
months. Warranty does not cover wear parts such as solid tool bushing, thrust washer, tool pin,
spring pin, and other metal parts and components which are subject to constant wear.
These warranties do not cover failures resulting from:
•
If you use your breaker for other than its intended purpose or if your equipment’s
specifications don’t meet breaker’s requirements.
•
If you mount the breaker on faulty equipment
•
Improper service or operation
•
Poor maintenance
•
Use of low-quality oil and lubricants
•
Disregarding oil purity and viscosity requirements
•
Modifying the breaker without manufacturer’s approval
•
Damages caused by using aftermarket replacement parts
•
Equipment failure due to improper use of breaker
Note: any data or specifications in this manual may be subject to change without prior notice.