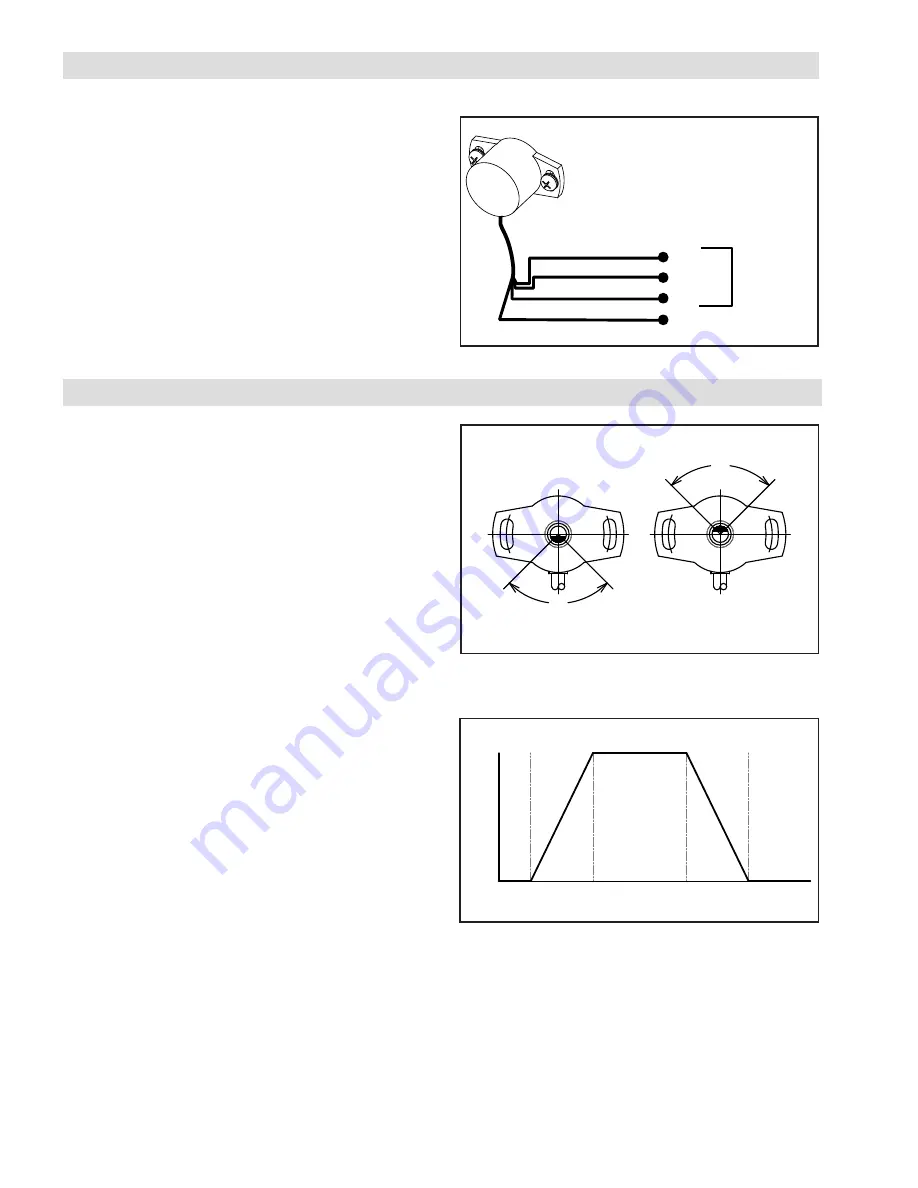
FORM NO. L-21261-B-0214
6
+24 VDC
SHIELD WIRE
BROWN
WHITE
GREEN
SIGNAL
DANCER
POSITION
CONTROLLER
COM
EARTH GROUND
Figure 6
1. Route the Dancer Position Sensor signal cable through
the machine.
2. Connect the signal cable to a controller (See Figure
6).
NOTE: The shield wire from the signal cable should
be earth grounded at the controller.
If noise is still present on the position signal, ensure
the sensor shaft has a low impedance connection to
earth ground through the machine frame.
ELECTRICAL CONNECTIONS
ADJUSTMENT
1. Apply power to the Dancer Position Sensor.
2. Refer to Installation for the proper alignment of the
sensor.
3. Using a voltmeter, measure the voltage across the
green (+) and brown (-) wires (See figure 6). The
voltage reading must match the supply voltage for
proper operation (See Specifications).
4. Measure the sensor output voltage across the white
(+) and brown (-) wires. With the dancer arm held in
its mid travel position, the sensor output should be
approxi5 VDC. If it is not, then slightly loosen
the sensor’s fasteners and rotate the sensor until the
voltage reading is +5 VDC. Refer to Figure 7 and 8
for mid travel position and sensor voltage output.
5. Tighten the fasteners securely to prevent the sensor
from moving.
6. Move the dancer arm through its full range of motion
and check that the voltage changes between 0 and
10 VDC. If the output voltage stops changing as the
dancer arm is moving, slightly loosen the sensor’s
fasteners and rotate the sensor. If this persists,
the angular movement of the dancer arm might
exceed the measurement range for the sensor (See
Specifications).
7. Trim back any unused wires to prevent electrical
shorting problems.
8. At this time the installation and adjustment of the
dancer position sensor is complete. Refer to the
controller manual for any further setup and calibration
procedures.
Figure 7 Dual Output Range
Figure 8 Sensor Output
60°
10V
0V
10V
0V
60°
30°
330°
0°
150°
210°
180°
0V
10V
5V
330°
0°
30°
150°
180°
210°
330°
Note: Sensor viewed from front.