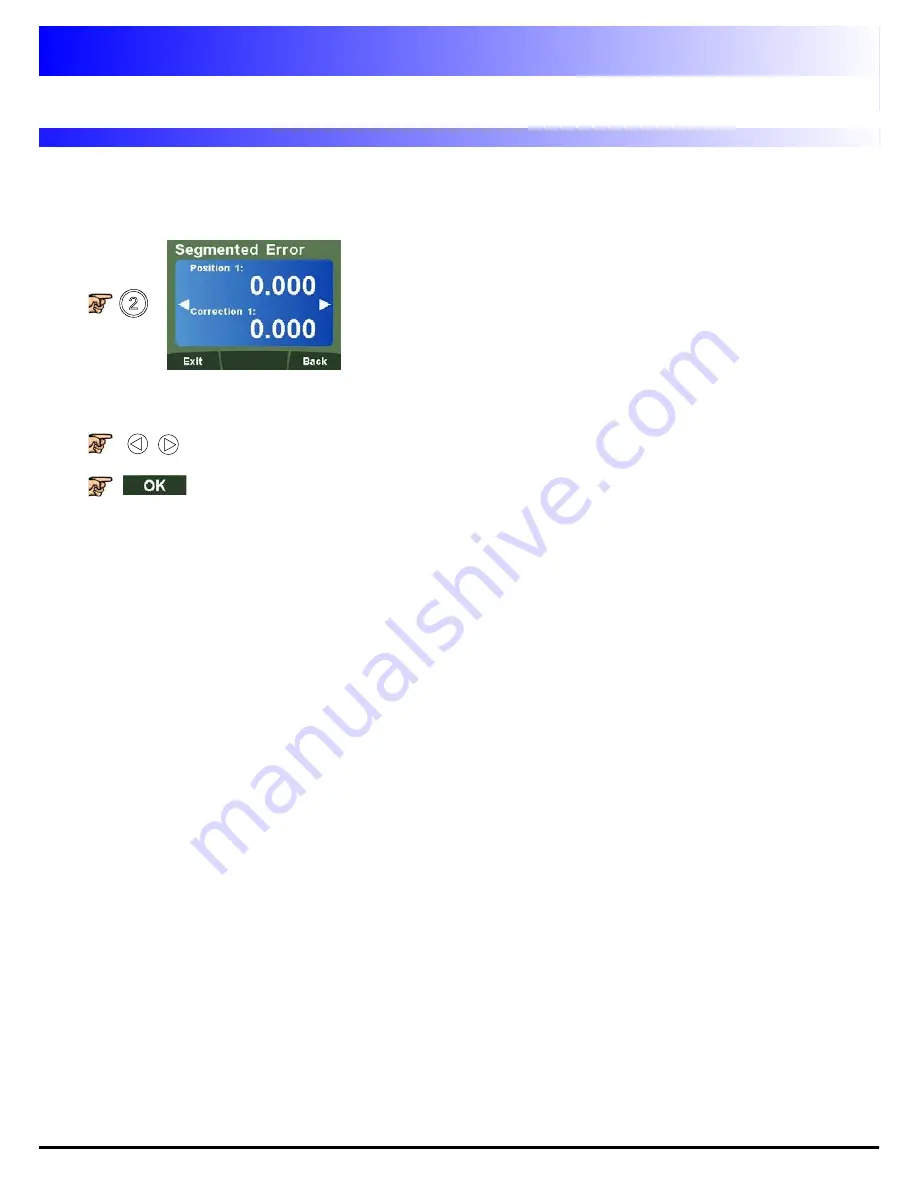
Setting Up The Unit
17
Program Mode
Position 1:
Enter a value using the numeric key-
pad for the 1st correction point (I.E 5.000)
Correction 1:
Enter a value using the numeric
keypad for the correction value (I.E -0.010)
Note:
The correction value is limited to a
minimum of 0.005mm (0.0002”)
to navigate between points. A maximum of 200 points are available.
to accept the compensation at the point reached.
The program mode enables the user to define the correction points manually and then enter them into
the DP1200. The position is where the correction point occurs, and the correction point is the value to
be corrected at that point.
Summary of Contents for dp1200
Page 1: ...User Manual DP1200 Digital Readout...
Page 2: ......