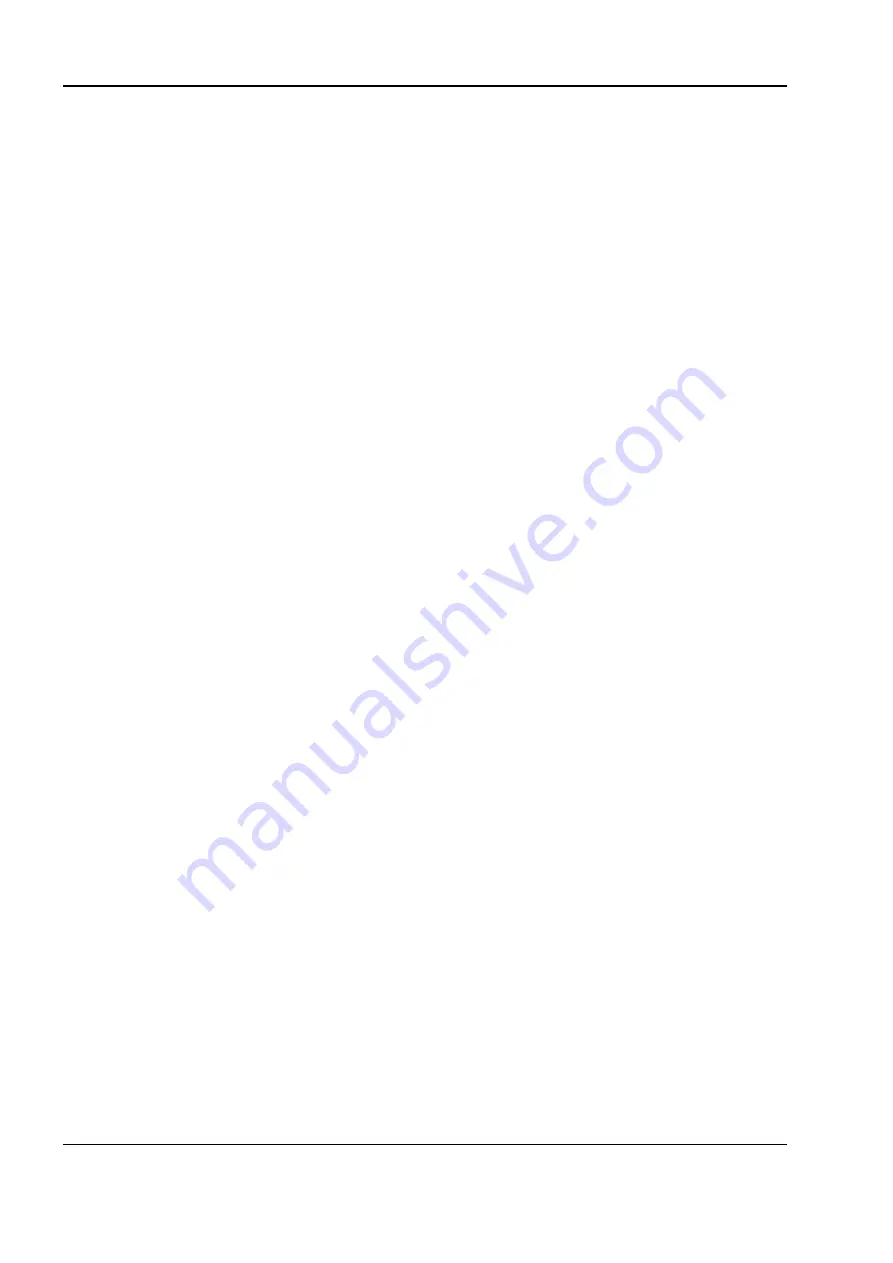
GENERALITIES
Carefully read personal and machine SAFETY PRECAUTIONS (at the beginning of this manual)
0 - 2
W130/W130TC
When working on slopes or near sudden level drops in the
terrain, avoid areas where ground is loose or soft since
overturn or loss of machine control could result.
If noise level is high and continuosly exceeds 90 dBA over
8 hours at the operator's ear, wear approved ear protection
in compliance with local regulations.
Where counterweights are provided, do not operate the
machine if they have been removed.
When transporting a loaded bucket, keept it as rolled-back
and low as possible for maximum visibility, stability and
safety of there machine. Ground speed should be ad-
equate to the load and ground conditions.
The load must always be properly arranged in the bucket;
move with extreme care when transporting oversize loads.
Use only the type of bucket recommended for the machine
and the materials to be handled. Follow the recommenda-
tions concerning loading capacity, arrangement of the
materials, characteristics of the ground and job to be
performed.
Do not lift and move loads overhead where persons are
standing or working, nor downhill when working crosswise
on slopes. In this case, the bucket should be unloaded on
the uphill side, whenever possible.
Start and stop the machine carefully when the bucket is full.
Do not move off without first reducing engine speed.
Overtaking manoeuvres should be performed only when
absolutely necessary and unavoidable. Beware possible
uneven terrains, poor visibility, presence of other machin-
ery or persons out of sight.
Operate the machine at a speed adequate to the working
site conditions and in any case slow enough to ensure
complete control at all times.
Check instruments at start-up and frequently during
operation. Stop the machine immediately should any
malfunction be signalled.
Never use the bucket as a man lift or to carry riders.
Never use the machine as a work platform or scaffolding,
nor for other improper use (such as pushing railway cars,
trucks or other machines).
Pay attetion to people within the machine operating range.
Load trucks from the driver’s side whenever possible.
Prior to operating the machine, check which obstacles
and/or difficulties you will encounter, such as narrow
streets, overhead doors, cables, piping, as well as ground,
bridges, paving and ramps bearing load limitations.
In case of road transfers, find out beforehand what condi-
tions are likely to be encountered, such as size restrictions,
heavy traffic, paving type, etc.. Beware fog, smoke or dust
that obscure visibility.
When crossing gullies or ditches, move at an angle with
reduced speed after ensuring ground conditions will per-
mit a safe traverse.
Do not operate the machine if you are extremely tired or feel
ill. Be especially careful towards the end of the working shift.
Do not operate a machine with misadjusted brakes.
Operate the machine at low speed which can ensure
complete control at all times.
Travel slowly over very rough terrain, slopes or near drop-
offs, in congested areas or on frozen or slippery surfaces.
When backing, always look to where the machine is to be
moved. Be alert of the position of bystanders. Should
someone enter the work area, STOP THE MACHINE.
Maintain a safe distance from other machines or obstacles
to ensure required visibility conditions. Give way to loaded
machines.
Maintain a clear vision of the surroundings of the travel or
work area at all times. Keep cab windows clean and
repaired.
When machines are operating in tandem, the pusher (rear)
must be equipped with the appropriate deflectors to protect
the front unit driver against the air stream coming from the
blower fan.
When pulling or towing through a cable or chain, do not
start suddenly at full throttle. Take-up slack carefully.
Carefuly inspect the towing items for flaws or problems
before proceedig.
Avoid kinking or twisting chains or cables. Do not pull
through a kinked chain or cable as the high stresses
existing in this condition may induce failures. Always wear
heavy gloves when handling chains or cables.
Chains and cables should be securely anchored. Anchor
points should be strong enough to withstand the expected
load. Keep anyone clear of anchor points and cables or
chains.
DO NOT PULL UNLESS THE OPERATOR’S COMPART-
MENTS OF THE MACHINES INVOLVED ARE PROP-
ERLY PROTECTED AGAINST POSSIBLE BACKLAS IN
CASE OF CABLE OR CHAIN FAILURE OR DETACH-
MENT.
Be alert of soft ground conditions close to newly con-
structed walls. The fill material and machine weight may
cause the wall to collapse.
In darkness, check area of operation carefully before
moving in with the machine. Use all lights provided. Do not
move into low visibility areas.
If the engine tends to stall for whatever reason under load
or at idle, immediately report this problem to the mainte-
nance managers for proper action. Do not operate the
machine until this condition has been corrected.
On machines fitted with suction radiator fans, regularly
check the engine exhaust system for leaks, as exhaust
fumes expelled towards the operator are toxic.
Operators must know thoroughly the performances of the
machine they are driving.
SAFETY RULES
Find manuals at https://best-manuals.com
Find manuals at https://best-manuals.com
Summary of Contents for W130
Page 4: ...Find manuals at https best manuals com Find manuals at https best manuals com ...
Page 6: ...Find manuals at https best manuals com Find manuals at https best manuals com ...
Page 36: ......
Page 41: ...This as a preview PDF file from best manuals com Download full PDF manual at best manuals com ...