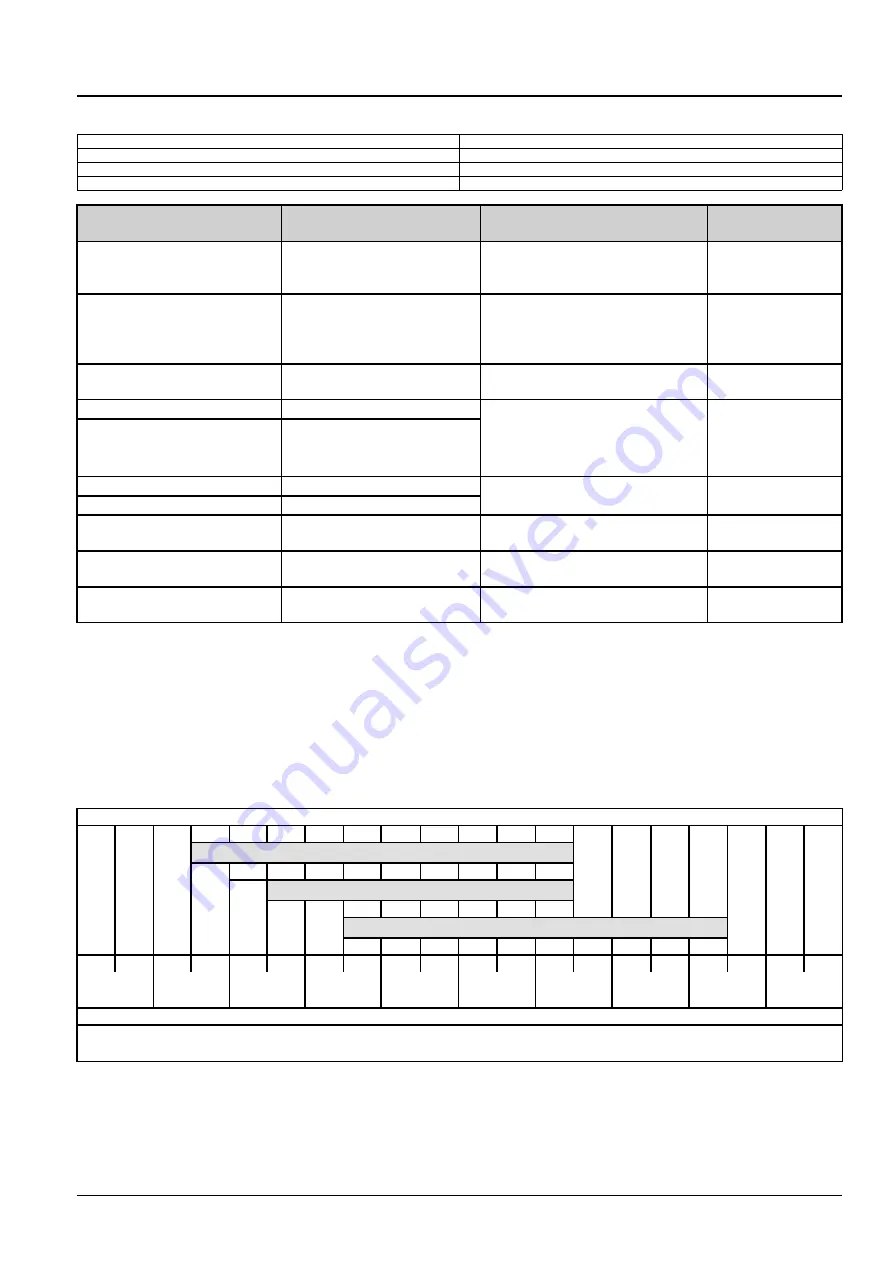
INTRODUCTION
Capacities
T8.295
LA
T8.325
LA
T8.355
LA
T8.385
LA
System
Quantity
Recommended fluid
International
specification
Engine lubrication – with filter
25.0 L
(
6.6 US gal
)
NEW HOLLAND AMBRA
MASTERGOLD™ HSP ENGINE
OIL SAE 15W-40
ACEA E7 API CI-4
CES 20078
Cooling system
27.0 L
(
7.1 US gal
)
50%
of water and
50%
of
NEW HOLLAND AMBRA
ACTIFULL™ OT EXTENDED
LIFE COOLANT
ASTM D 6210
– Monoethylene
glycol
Transmission
172.0 L
(
45.4 US gal
)
NEW HOLLAND AMBRA
MASTERTRAN® ULTRACTION
SAE 10W-30 API
GL-4
Front axle – central reservoir
17.5 L
(
4.6 US gal
)
Front axle – final drives (hubs)
Class 4.75
4.3 L
(
1.1 US gal
)
Class 5.0
4.5 L
(
1.2 US gal
)
NEW HOLLAND AMBRA
HYPOIDE 140
SAE 10W-30, API
GL-4
Fuel tank – main (*)
359.6 L
(
79.1 UK gal
)
Fuel tank – auxiliary (*)
445.0 L
(
117.6 US gal
)
Petroleum diesel fuel (B7
Biodiesel)
-
Grease fittings
As required
NEW HOLLAND AMBRA GR-9
MULTI-PURPOSE GREASE
NLGI 2
Air conditioning – refrigerant
gas
2100 g
CNH R
EFRIGERANT
HFC-134
A
-
Air conditioning – compressor
lubricant
285 mL
S
ANDEN
SP-15 L
UBRICANT
-
(*) Theoretical fuel tank volume. Use only as a reference for the net volume of the tank.
NOTE:
To avoid damage to your machine, always use the same type of coolant. When you top up, use pure water.
If you change the additive used, clean the cooling system first.
NOTE:
Always check that the implement does not use more oil than is available in the tractor. The transmission
should have at least the minimum oil level in order to operate.
The correct engine oil viscosity grade is dependent upon ambient temperature. See the table below for the recom-
mended viscosity at different ambient air temperature ranges.
SAE 5W30
SAE 10W - 30
SAE 15W-40
-40 °C
-40 °F
-30 °C
-22 °F
-25 °C
(
-13 °F
)
-15 °C
(
5 °F
)
0 °C
32 °F
10 °C
50 °F
20 °C
68 °F
30 °C
86 °F
40 °C
104 °F
50 °C
122 °F
In environments with extreme air temperatures that require long periods of use of the machine, use
SAE 50
oil for
extremely high temperatures and
SAE 5W30
for extremely low temperatures.
47681318 16/05/2017
35