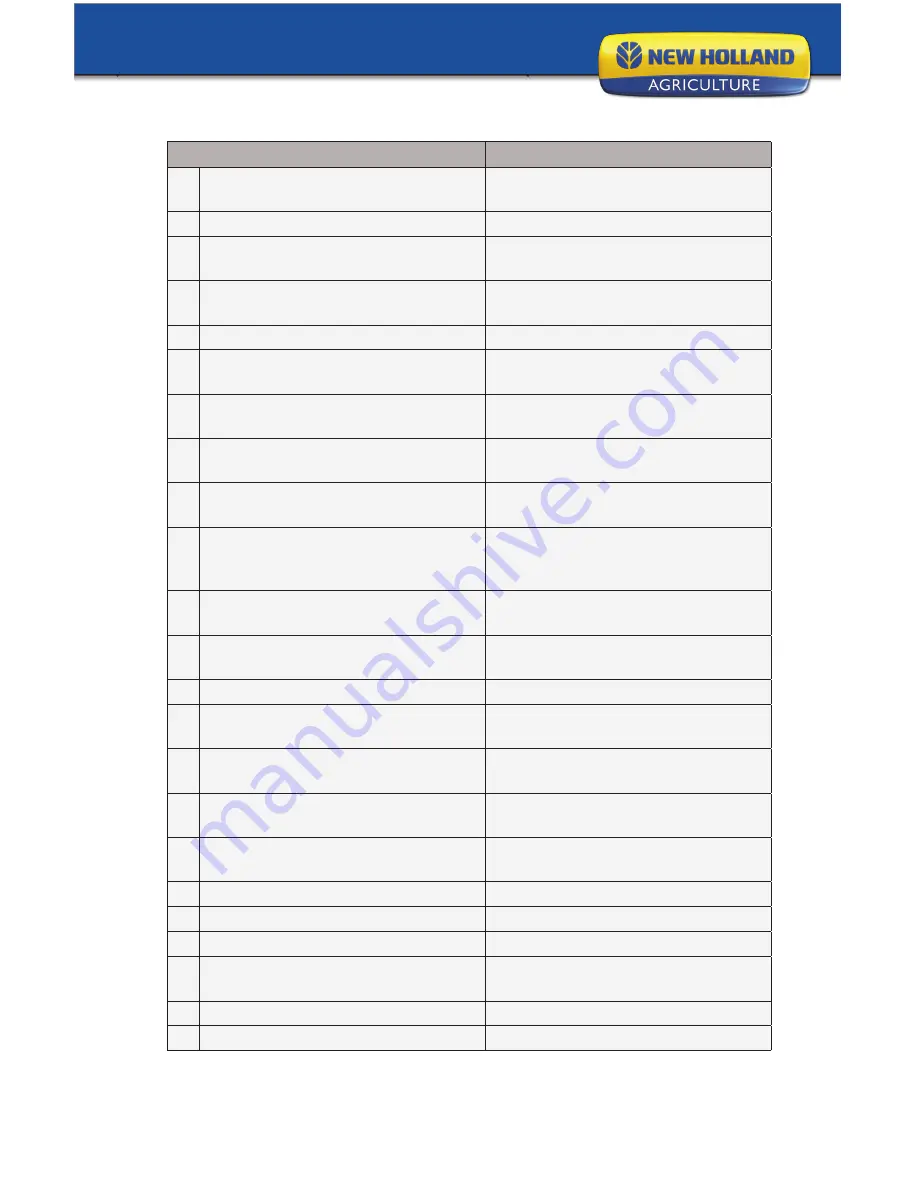
17
troubleshooting
Possible Cause
Possible Solution
A Low Oil Shutdown
Fill engine with the adequate amount
of oil.
B Cold Engine
Choke engine to start.
C No Fuel
Add gas to engine. Make sure fuel
shutoff valve is open
D Engine not turned ON
Place ON/OFF switch in the ON
position.
E Spark plug wire not attached
Attach spark plug wire to spark plug.
F Compressor viscosity too high for
ambient temperature.
Drain existing lubricant and refill with
proper lubricant.
G Belt tension too tight or sheaves not
aligned.
Check tension/ alignment.
H Air leaks in discharge piping.
Check tubing connections, Tighten
joints or replace as required.
I
Compressor components leaky,
broken, loose.
Inspect components. Clean or
replace as required.
J
Loose flywheel or motor pulley,
excessive end play in motor shaft or
loose drive belts.
Check flywheel, motor pulley, and
crankshaft drive belt tension/align-
ment. Replace or repair as required.
K Leaking check valve or check valve
seat blown out.
Replace check valve.
L Clogged or dirty inlet and/or dis-
charge line.
Clean or replace.
M Defective safety/relief valve.
Replace.
N Pressure switch unloader leaks or
does not work.
Realign stem or replace.
O Inadequate ventilation around
flywheel.
Relocate compressor for better
airflow.
P Leaking, broken or worn inlet un-
loader parts at check valve.
Inspect parts and replace as
required.
Q Excessive condensation in receiver
tank.
Drain receiver tank.
R Detergent lubricant in crankcase.
Replace with proper lubricant.
S Light duty cycle.
Increase duty cycle.
T Lubricant level too high.
Drain excess lubricant.
U Worn cylinder finish.
Deglaze cylinder with 180 grit
flex-hone.
V Low pressure inlet valve leaking.
Inspect, clean or repair as required.
W High pressure inlet valve leaking.
Inspect, clean or repair as required.