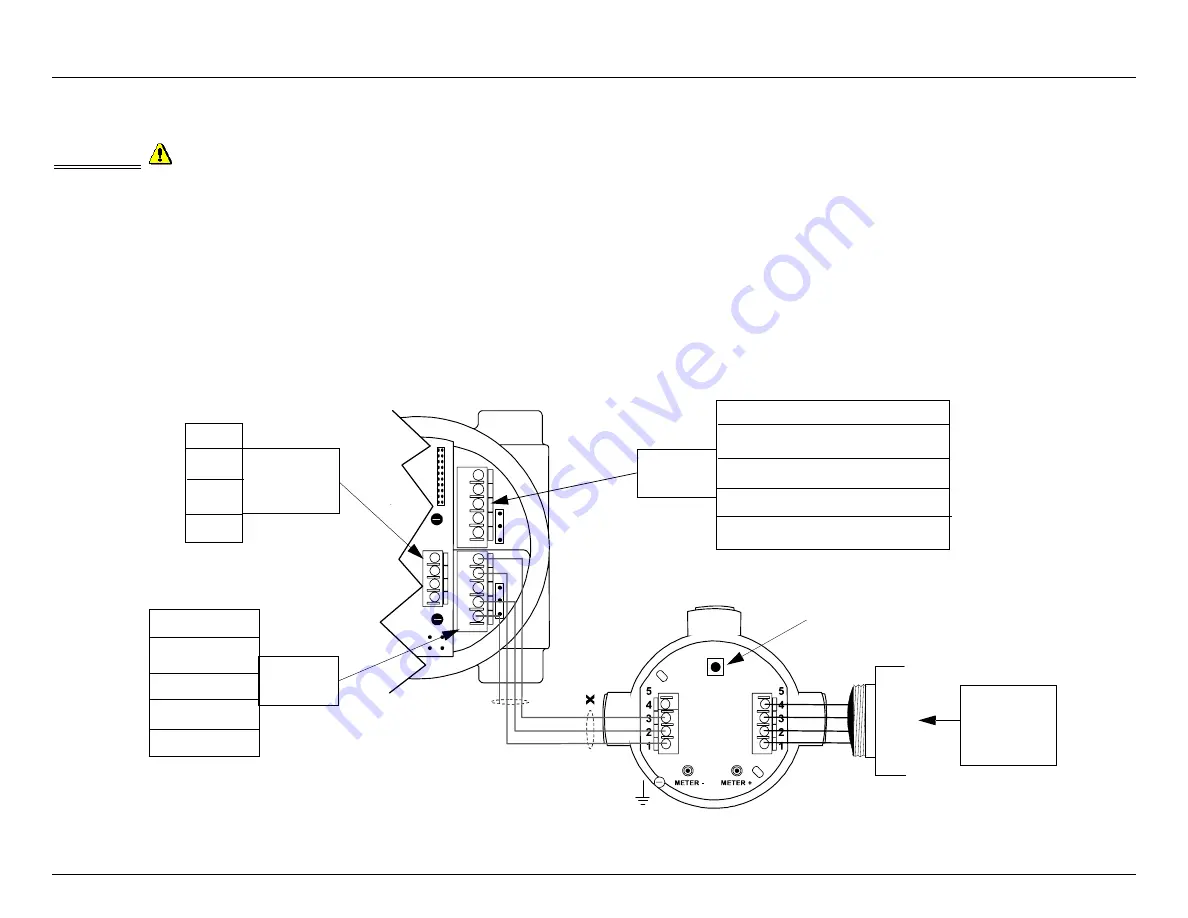
Net Safety Monitoring Inc
Modbus Controller & 4-20 Fire Head
4
W
IRING
—
C
ONTROLLER
WARNING:
Power to the unit must be OFF before wiring.
1. Once the Controller’s Housing Cover is removed, connect the Fire Head to
the Junction Box, the Junction Box to the Controller and the Output
Terminals to the output signal wires.
2. Replace the Controller’s Housing Cover and turn Controller On.
3. Ensure display reads
Start Delay
, Status LED is Red Slow Flash and
current output displays 3.0 mA. This is the start-up delay sequence which
will last approximately 90 seconds.
Shielded copper instrument wire (minimum 18 AWG) should be used for
separations up to 500 feet. Shielded copper instrument wire (minimum
16 AWG) should be used for separations up to 2000 feet. Consult the factory if a
greater separation distance is required. Ensure the appropriate wire is used for
Class 1/Division 1 hazardous applications.
Note:
If the 4-20 mA signal is not used, connect a jumper between the 4-20
terminal and the COM terminal on the Terminal Board.
RS-485 Communication
Connect devices in a chain via the Modbus terminals. The last device in the
chain requires end of line termination (refer to "MODBUS Termination" on
page 6).
Figure 4:
Wiring
—
Fire Head, Junction Box and Controller
MVI
+24V
COM
4-20
Blu
W
Blk
Red
RST
+24V
COM
4-20
ISO
+24V
SIG
Com -
Shld
Fire Head
Input
to
Junction Box
Internal Ground
(Green Wire)
Cut Shiel
d
Shield
Power
Terminals
Sensor
Terminals
+24V = +24V
Sig = 4-20
n/a
COM = COM
Shld
RST = Remote Reset
+24V = Power +
COM = Power -
4-20 = Current Output
ISO = +24V isolated 4-20 power
Terminals
Modbus RTU
to PLC
A
B
COM
-
Manual Vi Test Button
Summary of Contents for MAN-0069
Page 2: ......