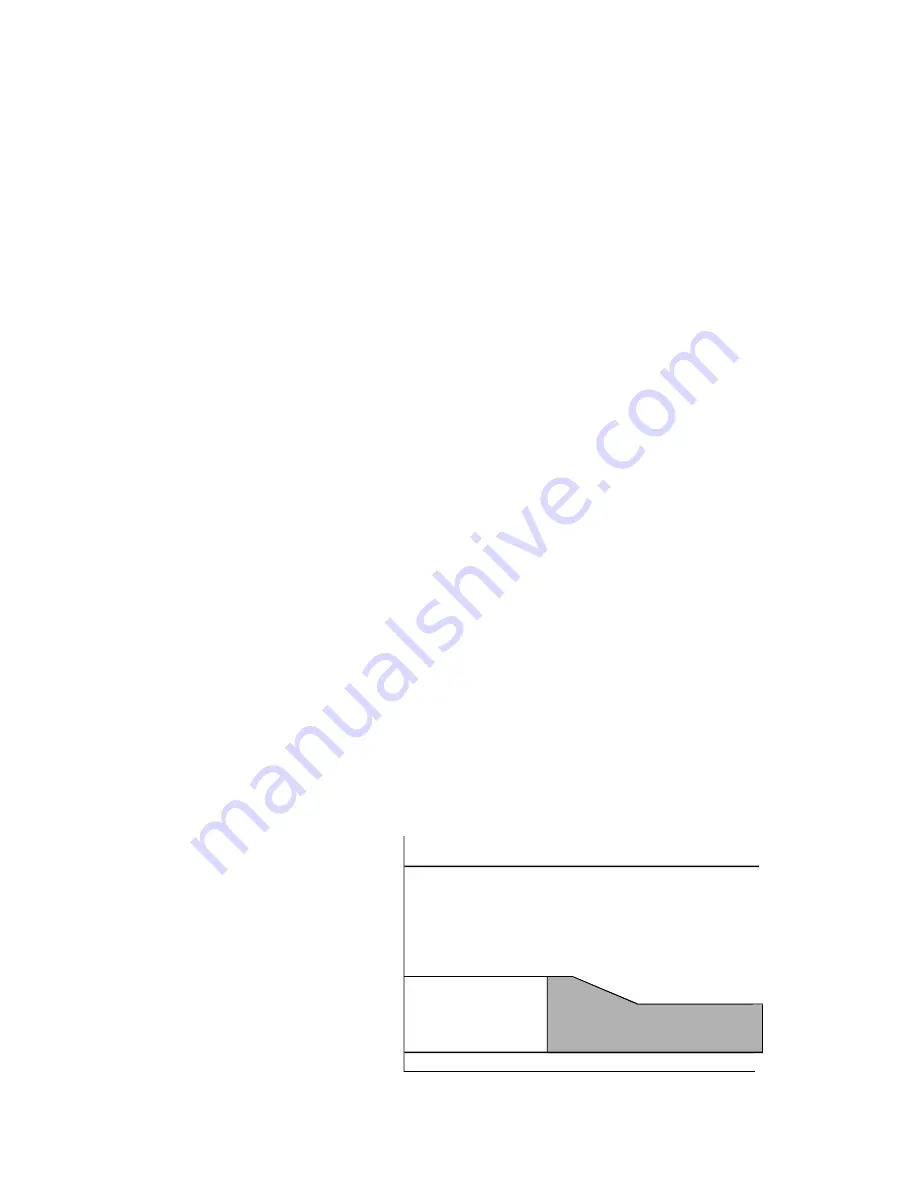
- 9 -
Unfavorably high total ionized solids (TIS) can accelerate the rate of galvanic
corrosion. These contaminants can function as electrolytes which increase
the potential for galvanic cell corrosion and lead to localized corrosion such
as pitting which can be observed at the studs and on the outside surface of
cooling coils. Eventually, the pitting will become so extensive that the coil will
leak refrigerant into the water reservoir.
For example, raw water in the U.S. averages 171 ppm (as NaCl). The recom-
mended level for use in a water system is between 0.5 to 5.0 ppm (as NaCl).
Recommendation: Initially fill the tank with distilled/deionized water. Do not
use untreated tap water as the total ionized solids level may be too high.
Maintain this water quality at a resistivity of between 1 to 10 megohm-cm
(compensated at 25°C) by using a purification system. Although the initial fill
may be as high as 10 megohm-cm (compensated at 25°C), the desired level
for long time usage is 1 to 3 megohm-cm (compensated at 25°C).
The above two recommendations will reduce the electrolytic potential of the
water and prevent or reduce the galvanic corrosion observed.
Water Quality Standards
and Recommendations
Permissible (PPM)
Desirable (PPM)
Microbiologicals
(algae, bacteria, fungi)
0
0
Inorganic Chemicals
Calcium
<40
0.6
Chloride
250
<25
Copper
1.3
1.0
Iron
0.3
<0.1
Lead
0.015
0
Magnesium
<12
0.1
Manganese
0.05
<0.03
Nitrates\Nitrites
10 as N
0
Potassium
<20
0.3
Silicate
25
<1.0
Sodium
<20
0.3
Sulfate
250
<50
Hardness
17
<0.05
Total Dissolved Solids
50
10
Other Parameters
pH
6.5-8.5
7-8
Resistivity
0.01*
0.05-0.1*
* Megohm-Cm (Compensated at 25°C)
15.00
10.00
3.00
1.00
0.10
0.05
Resistivity (megohm-cm @ 25°C)
Not Recommended, Increasingly Corrosive
Operations with Stainless Steel Systems
Operations with
Mixed Metals
Copper/Brass/
Stainless Steel
CONSULT MATERIALS ENGINEER
10
20
30
40
50
60
70
80
Water Quality Considerations
°C