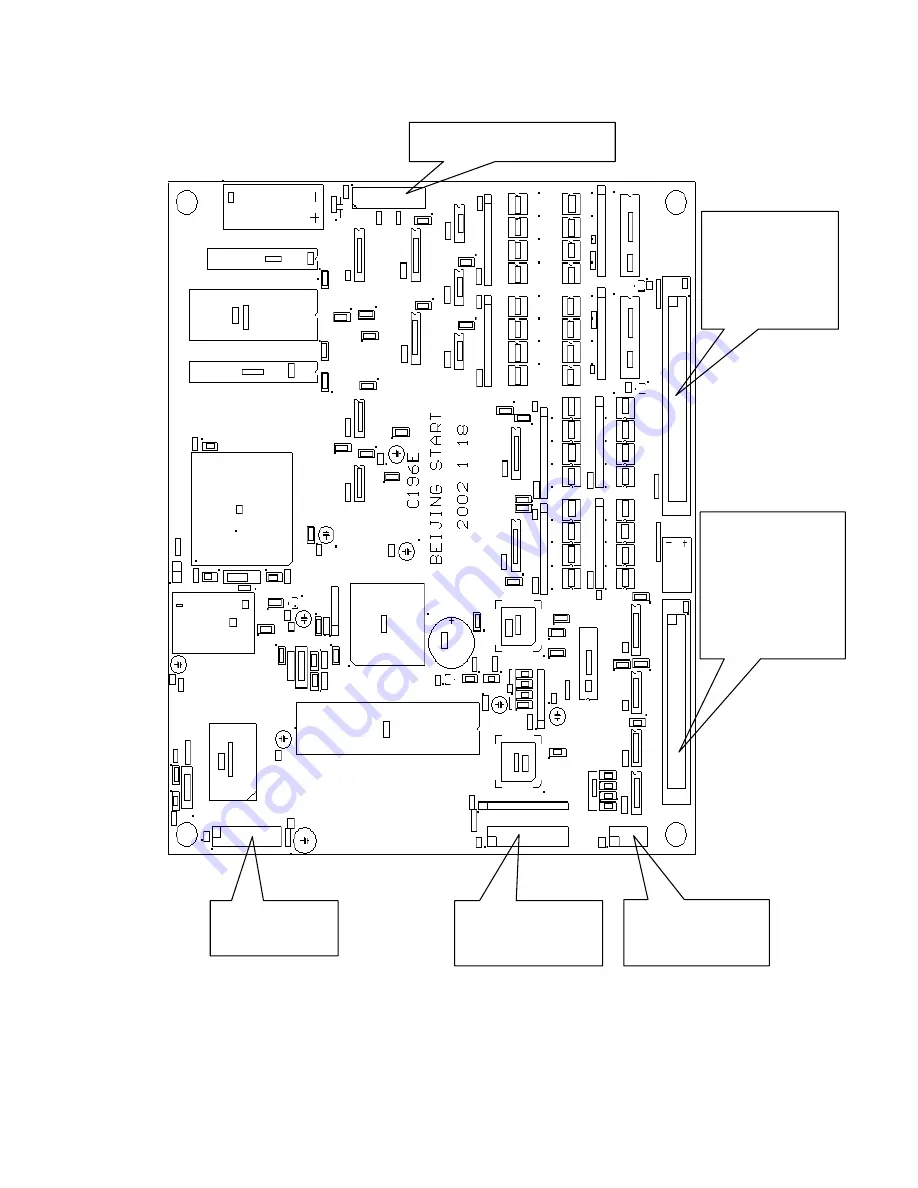
37
5.3
CNC main-board
J1 DC power source input DC5V
J2
J2
J2
J2
photo-electricity isolation
16 way input
16 way output
D/A
D/A
D/A
D/A
output
J3
J3
J3
J3
photo-electricity isolation
step motor signal
Coder signal
Hand-pulse signa
llll
RS232
RS232
RS232
RS232
J4 F1
J4 F1
J4 F1
J4 F1----F6
F6
F6
F6
Little
keyboard
J5
J5
J5
J5
Character/numb
er
J6 LCD interface
www.EngineeringBooksPdf.com