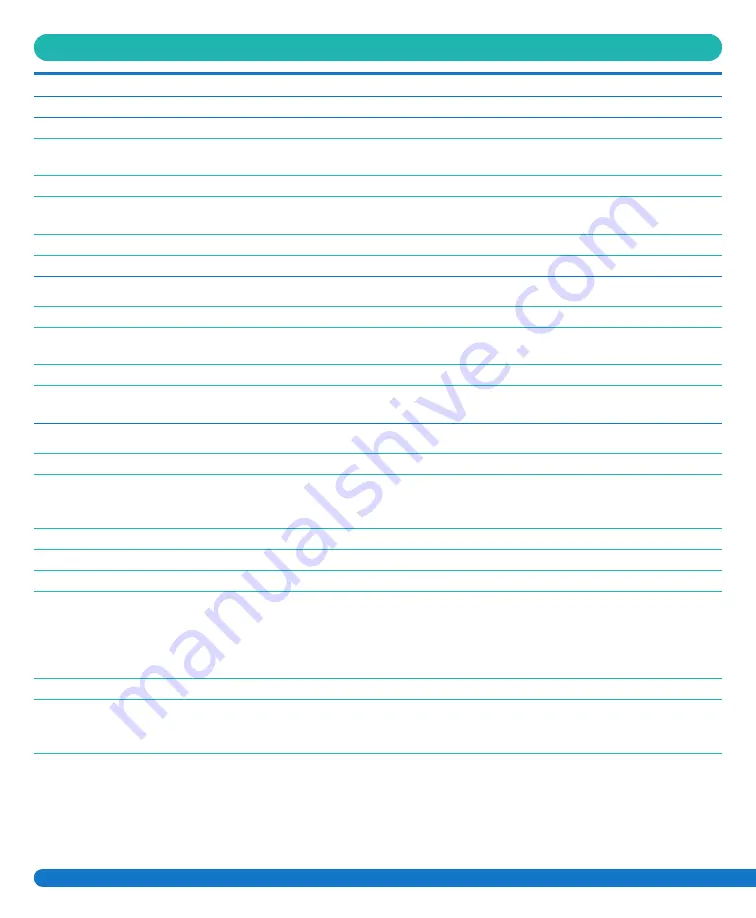
10
Appendix A - Controller Programming:
Parameters Explained
Parameter
Value
Range
Example
Input Switch Behaviors
Tank Level Switch delay (actuation and de-actuation)
Seconds
2.0
This specifies the time that the tank switch must be closed or open before the controller accepts it as a valid
condition. The function is to prevent nuisance tripping of the RO especially in small tanks or turbulent tanks
Pressure Switch delay (actuation and de-actuation)
Seconds
3
This specifies the time that the pressure switch must be closed or open before the controller accepts it as a valid
condition. Since pressure switches usually have built-in hysteresis this value is set at 0.
Pretreat Switch delay (actuation and de-actuation)
Seconds
2
This is the time that the pretreat switch must be OPEN before the controller accepts it as a valid condition.
Pump/Inlet Solenoid Behaviors
Pump start delay
Seconds
10
On RO start-up, after the tank switch opens, the inlet solenoid valve is energized. When the inlet pressure switch
closes this begins the “Pump start delay”. If the pressure switch remains closed, the pump will start after 10 seconds.
Inlet Solenoid stop delay Seconds 1
This value sets the delay for the inlet solenoid valve to be de-energized following the de-energizing of the motor on RO
shut down. The purpose is to prevent the pump from operating against a closed suction as the pump spins down.
Low Inlet Pressure Behaviors
Pump start retry interval (restart delay after LP fault)
Seconds
60
When the inlet pressure switch opens, the controller de-energizes the motor and the inlet solenoid valve remains open.
The controller will continue to monitor the inlet pressure switch. After the switch is closed for the duration of the
“Pump start retry interval” the motor is reenergized.
Low pressure fault shutdown, # of faults
Faults
5
Low pressure fault shutdown, time period to count faults
Minutes
10
Low pressure fault shutdown, reset after shutdown
Minutes
60
These three values work together to determine how the RO handles Low Pressure conditions. The first two values,
“# of faults” and “time period to count faults”, sets the limit for the number of low fault conditions over time that are
required to place the RO in “Low Pressure Fault Shutdown”. The third value sets the duration of the “Low Pressure
Fault Shutdown” which is the period that the RO will remain idle before trying to restart. The purpose of the Low
Pressure Fault Shutdown is to prevent an RO from turning OFF/ON repeatedly without any limit.
Low pressure time-out fault
Seconds
60
If the inlet valve is open, but the pressure isn’t sufficient to close the inlet pressure switch, the RO would run
indefinitely on line pressure. This value sets the time limit for the RO to operate with the inlet valve open with Low
Pressure as indicated by an Open inlet pressure switch before a Low Pressure Fault is added to the counter above
Summary of Contents for NRO ROC-3HE
Page 1: ...Nelsen NRO ROC 3HE System Controller Documentation Systems with 3 hp Motors and Above...
Page 4: ...2 Figure 1 Simplified Schematic...
Page 5: ...3 Figure 1 1 Field Wiring Diagram...
Page 7: ...5 Typical Configuration Figure 3 Controller Detail CPU 4 Typical Configuration...
Page 8: ...6 Figure 4 Controller Detail Terminal Board TB 1 See Fig 1 for schematic...