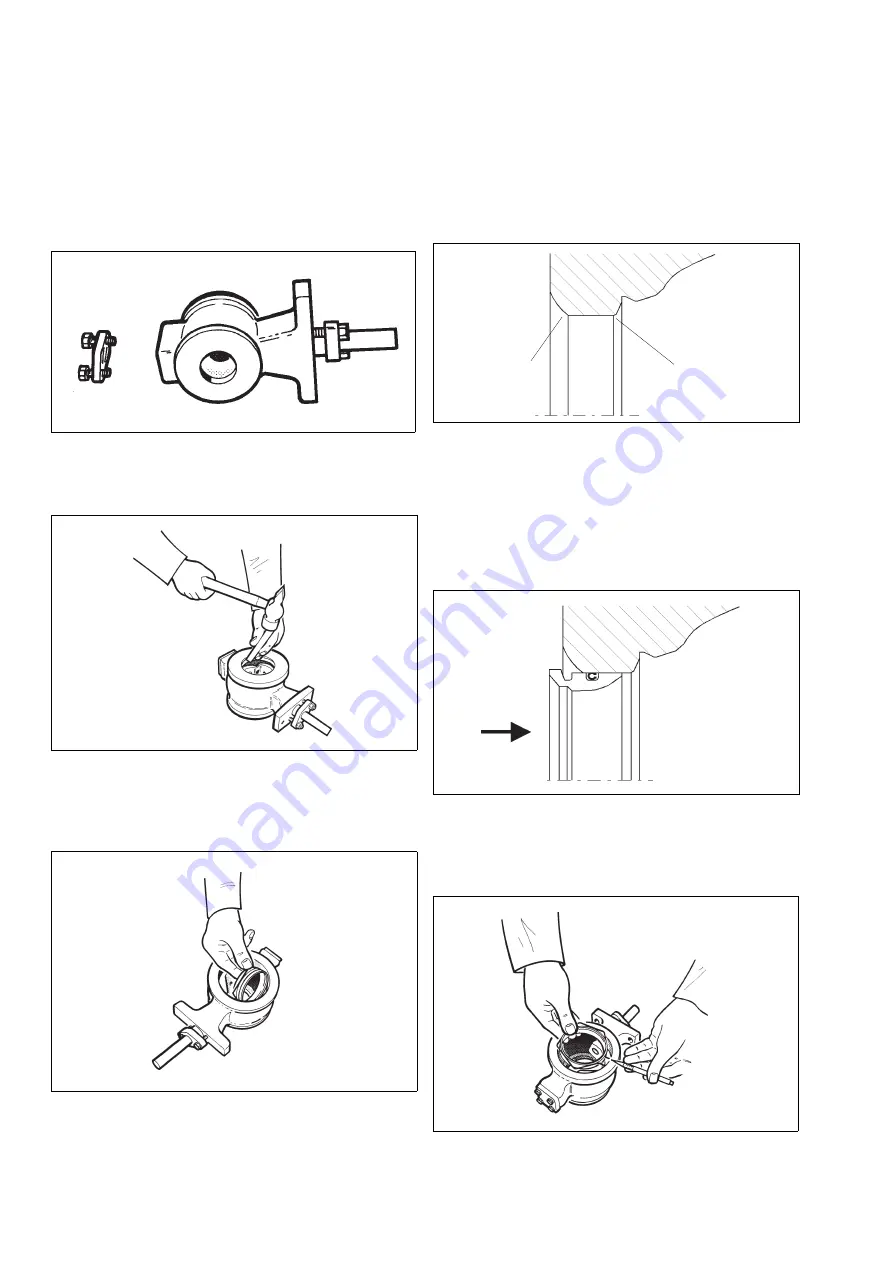
8
3 R 71 EN - Issue 9/2020
•
In DN 25-40 valves (excluding the low-Cv versions), unfasten the
flange (10) and push the segment into the back position (Fig. 12).
•
DN 25 / 1" valves can be dismantled, as described in 4.6, to
make the replacement of the seat easier. Dismantling is always
necessary when a DN 25 / 1" valve has a low-Cv segment. If a
DN 25 / 1" valve with a low-Cv segment has an extra bushing (ø
33 mm / 1.3") in the downstream bore, send the valve to the man-
ufacturer for repair.
•
Tap the seat (4) with a soft spindle all around the circumference
from the upstream side to make it fall into the body, Fig. 13.
•
Turn the valve and lift the seat from the body through the down-
stream flow port, Fig. 17.
•
Clean and check the removed parts.
Installing the seat
The back seal (6) of the segment seat (4) is normally a lip seal. The
seat is easier to install if the back seal is precompressed. An O-ring
seal does not need precompression.
•
Clean the flow port that houses the seat. Remove any burrs.
Round off the edges using a fine abrasive paper and clean the
flow port carefully, see Fig. 15.
•
Place the back seal (6) onto the seat (4).
•
Lubricate the flow port, seat (4) and back seal (6) and the lock spring (5)
with a volatile lubricant, e.g. Hyprez.
Make sure that the lubricants are compatible with the medium.
•
Only for a lip seal:
Push the seal carefully into the flow port for
about 15 minutes, Fig. 16. The following work phases must be
completed before the precompression is lost.
•
Place the lock spring (5) on the seat.
•
When the valve is opened, the ends of the spring must be by the
V-shaped opening, see Fig. 17.
Fig. 12
Removing the blind flange
Fig. 13
Knocking off the seat
Fig. 14
Lifting the seat
Fig. 15
Rounding the sharp edges
Fig. 16
Precompression of the lip seal
Fig. 17
Mounting the seat
sharp edges
must be
rounded off
sharp edges
must be
rounded off