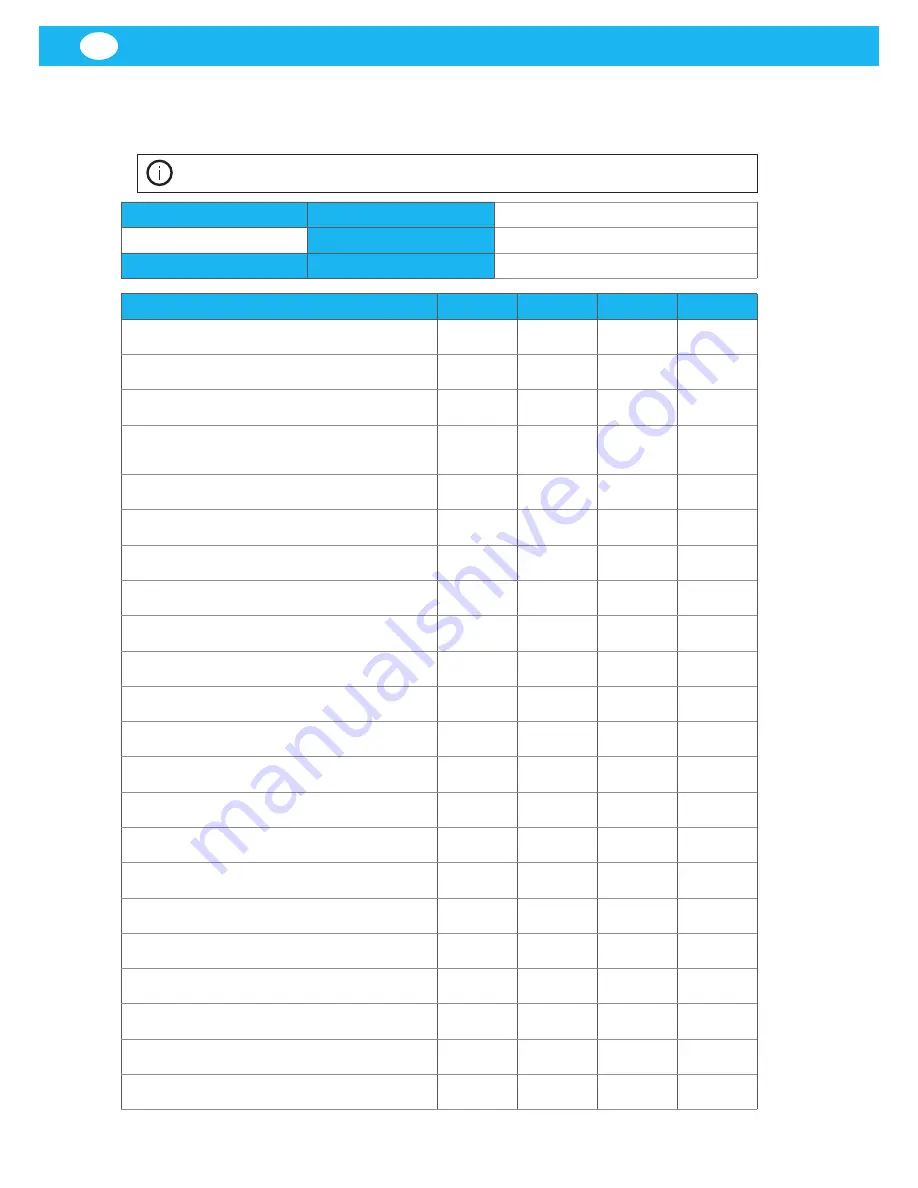
FlexPAK 800/1000
EN
30
Appendix B: Service protocol
Copy the service protocol, fill it in and save it as a service record.
NOTE!
If the results of the checks (for example, measured values) differ significantly from
previous results, investigate more carefully.
Unit No.
Date:
Operating hours:
Performed by:
Control items
Result
Result
Result
Result
Previous service record
Inspect/clean outside the unit
Remove dust deposits, clean work area
Remove corrosion by grinding, apply primer and touch up
paint
Vacuum, measure negative pressure
Cooling valve
Bearing motor
Fan
Cooling fan, motor
Bearing motor / fan
Safety switch
Box / housing
Main switch
Cable harness
Electrical connection points
Ground (earth) connection
Indicator lamps
Inverterr
Cooling air filter, functional control, frequency inverter
Cooling air filter, exchange
Rated current
Sealings
Summary of Contents for FlexPAK 1000
Page 2: ...FlexPAK 800 1000 2 ...
Page 3: ...FlexPAK 800 1000 3 Figures 4 English 11 ...
Page 6: ...FlexPAK 800 1000 6 1 2 3 4 5 6 7 14 13 12 11 9 8 10 7 6 ...
Page 8: ...FlexPAK 800 1000 8 9 10 1643 1mm 65 662 1mm 26 2 1771 4 1mm 70 2 1 4 5 6 8 7 9 3 1 ...
Page 9: ...FlexPAK 800 1000 9 11 12 14 13 ...
Page 10: ...FlexPAK 800 1000 10 1 0 m 39 4 A B C 16 17 15 Min 2 1m 83 A A A A C ...
Page 32: ...FlexPAK 800 1000 EN 32 ...
Page 33: ......
Page 34: ...www nederman com ...