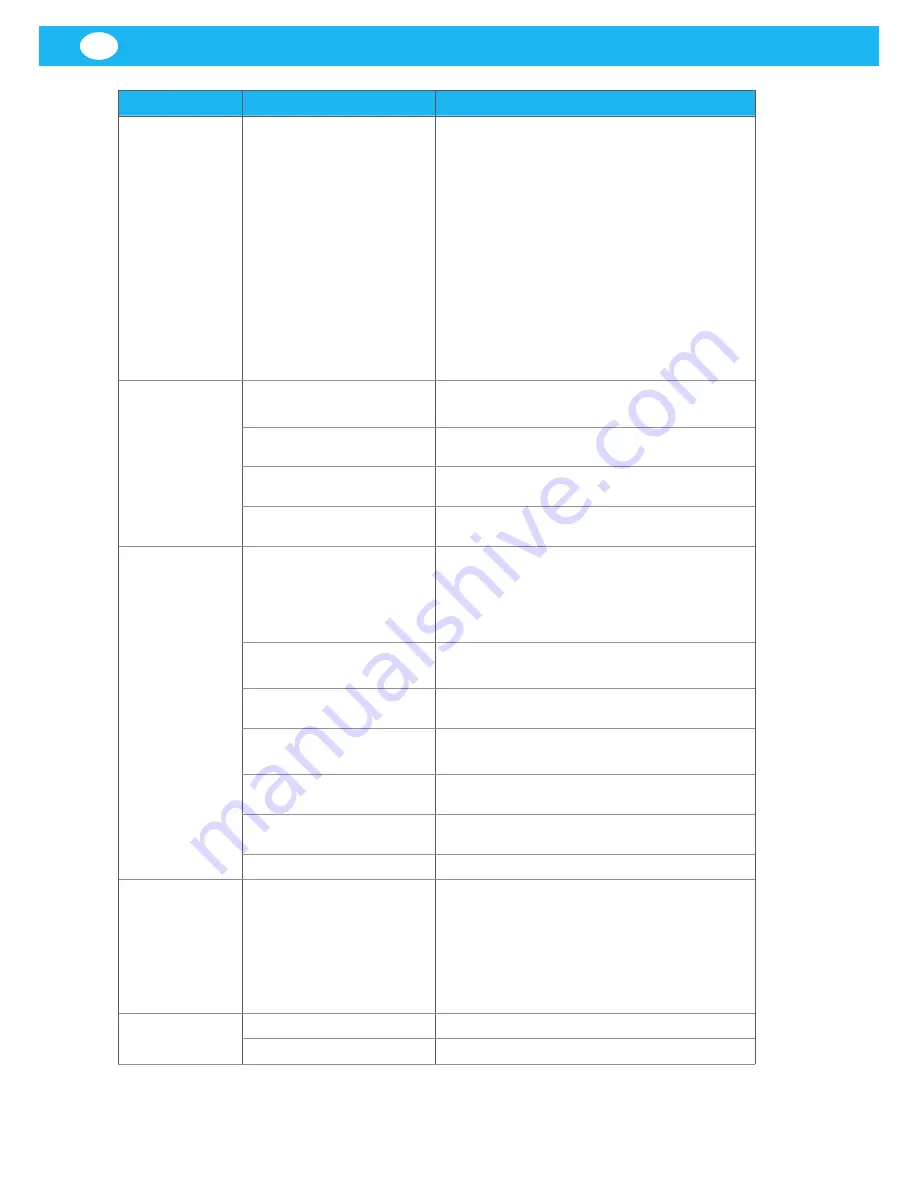
FlexPAK 800/1000
EN
26
Error
Possible cause
Solution
Defect pressure
sensor.
The pressure sensor is connected to PLC input 8
and at inverter input +AI1 terminal (2). The sensors
measurement range is 0 to -40 kPa. The signal goes from
10 to 0 V and 0 to -40 kPa, which gives 10 V at 0 kPa and 0
V at -40 kPa.
Measure the voltage signal at the inverter, between
terminals 2 (+) and 7 (-). When the motor is off, the input
signal at terminal 2 has to be 10 V, and when the motor is
running, the signal is 0 to10 V depending on the pressure
level in the system.
To check whether the sensor input is working, disconnect
the pressure sensor wire at terminal 2 and connect a
jumper between terminals 2 and 1. Press the OK button on
the PLC to reset the alert.
If the alert disappears, the pressure sensor input is
working and you will have to replace the pressure sensor.
Low vacuum or air
flow.
Deposits or blockage in ducts on
the way to the unit.
•
Clean the ducts.
•
Check the transport velocity.
The duct system is not properly
dimensioned.
Re-dimension the duct system or add an extra suction
source.
Valves in the duct system are not
working.
Check the duct system valves.
The filter cleaning does not work
or is insufficient.
Check the function of the filter cleaning.
Filter cleaning does
not work.
•
Problem with (PS) cable
•
DIR_time settings
If the unit does not go into Idling mode and filter cleaning
does not take place after 10 seconds, break the PS cable
manually by opening fuse holder F4. Wait at least
10 seconds. If switching to Idling mode occurs this time,
troubleshoot the PS cable. If switching does not occur,
check the time set on the display (DIR_time function).
The compressed air pressure or
flow is too low.
•
Adjust the pressure.
•
Check the hose dimension
The solenoid valve is not
connected properly.
Check the valve and air pressure.
The air lines, valve and/or cylinder
are blocked.
•
Clean or replace the air lines, valve and/or cylinder.
•
Filter incoming compressed air.
The cylinder and/or valve does
not work.
Replace the cylinder and/or valve.
Dust is hard to clean, normal
cleaning does not work.
Contact your nearest authorized distributor or Nederman
for technical advice.
The cleaning interval is too short.
Extend the cleaning interval.
Compressed air,
(Pr/t) is <1 bar.
See
‘3.3 Technical data’
. Too low compressed air pressure
can result in premature filter clogging. If the pressure
is lacking or too low, the piston cannot open the FCV
and lid properly. This results in insufficient cleaning and
premature filter clogging.
The CAS is connected to terminals X1:15 and X1:16. If no
CAS is installed, a jumper is linking the terminals to ensure
that the CAS message is not displayed in PLC Logo!.
No dust is collected
in the collector bin.
Filter cleaning does not work.
See section
‘6 Maintenance’.
Insignificant flow to the unit.
See ‘Low vacuum or air flow’.
Summary of Contents for FlexPAK 1000
Page 2: ...FlexPAK 800 1000 2 ...
Page 3: ...FlexPAK 800 1000 3 Figures 4 English 11 ...
Page 6: ...FlexPAK 800 1000 6 1 2 3 4 5 6 7 14 13 12 11 9 8 10 7 6 ...
Page 8: ...FlexPAK 800 1000 8 9 10 1643 1mm 65 662 1mm 26 2 1771 4 1mm 70 2 1 4 5 6 8 7 9 3 1 ...
Page 9: ...FlexPAK 800 1000 9 11 12 14 13 ...
Page 10: ...FlexPAK 800 1000 10 1 0 m 39 4 A B C 16 17 15 Min 2 1m 83 A A A A C ...
Page 32: ...FlexPAK 800 1000 EN 32 ...
Page 33: ......
Page 34: ...www nederman com ...