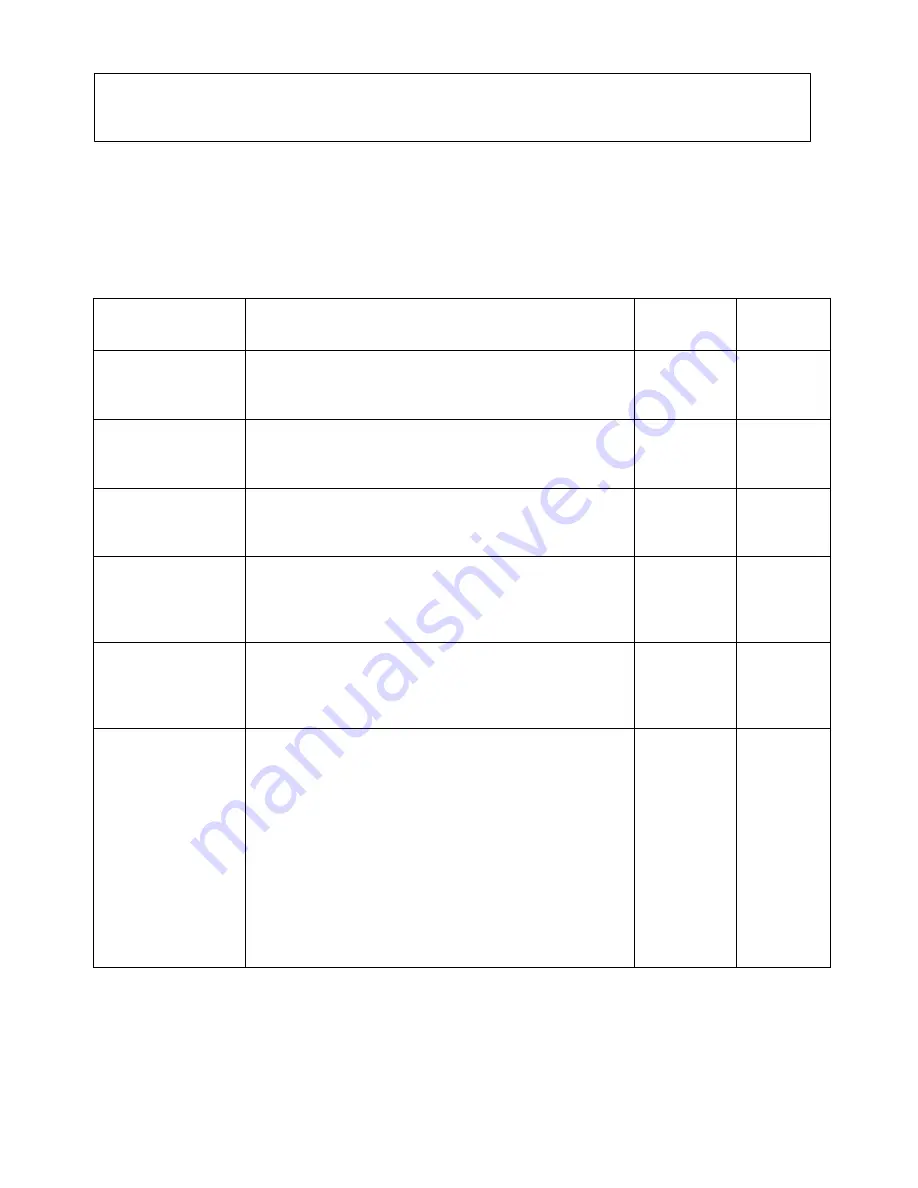
NW Global Vending – TECHNICAL MANUAL
This document was produced by MARK AC for the exclusive use of the technical personnel in the after-sales service.
. No part of this document may be divulged to a third party or reproduced partially or entirely without the prior permission of NW GLOBAL VENDING
. All rights reserved.
New dispenser “KORO”
07/10/2005
page 35 / 42
The vending machine KORO was designed to operate for a long time without malfunctions; however in order to
ensure excellent reliability periodic maintenance is necessary.
Such maintenance must be performed according to the number of selections made and the time lapsed.
Periodic and correct maintenance ensures reliability, constant quality and also guarantees safety standards over
time.
The following table indicates the functional units that must be subjected to periodic maintenance and the
frequency of maintenance. For the operations to be carried out, refer to the specific
Functional unit manuals.
Name of unit
DESCRIPTION OF OPERATION
N. of
selections
Max
frequency
Espresso brewer
unit
1)
Check state of filters and wear of silicone O-ring seal
2)
Replace upper and lower filters and related seals
3)
Descale the internal vent hole and lubricate with specific
food-safe grease
5000
8000
30.000
1 month
6 months
annual
Fresh brewer unit
1)
Check state of filters and wear of silicone O-ring seal; see
details in the functional unit manual for FB coffee brewing
2)
Open the unit and check the state of wear and internal
lubrication and if necessary replace and lubricate
4000
40.000
1 month
annual
Mixer unit
1)
Check the water tightness in the axial bush and the
correct assembly, if necessary replace.
2)
Check the wear of the motor brushes and clean off the
excess of carbon powder
50.000
annual
Boiler and
solenoid valve
assembly
If the boilers and the solenoid valves operate with soft water
or are fitted with specific softener filters, the should be no
need of periodic maintenance; otherwise periodically check
the grade of scaling and if necessary proceed to complete
descaling
According to
the water
hardness
Every 6
months
Steam exhauster
unit
There is not need of any particular maintenance
For perfect functioning, it is necessary that the powder
removal boxes be emptied periodically.
In addition, daily cleaning ensures also maximum hygiene of
the machine.
Every day
Coffee grinder
assembly
The motor was designed to operate for more than 200000
grinding cycles and the grinding wheels can ensure correct
grinding for at least 50000 cycles.
However, these values can vary because of possible
impurities in the coffee (pebbles, pieces of hard wood, etc.),
therefore it is advisable, except for premature wear, to
check and if necessary replace the grinding wheels every
50000 cycles.
Every 200000 cycles check the state of wear of the
ratiomotor brushes, if necessary replace and clean off the
wear residues.
In addition, every month check the correct positioning of the
grinding wheels and if necessary adjust to the correct
setting by means of the knurled knob.
50000
200000
4000
Every year
month
Extraordinary maintenance is carried out in the event of possible malfunctions.
For the most typical problems the vending machine is fitted with sensors that inform the software about any
malfunction. The following tables list the possible malfunctions and possible remedies.
27 – ROUTINE & EXTRAORDINARY
MAINTENANCE PROGRAM