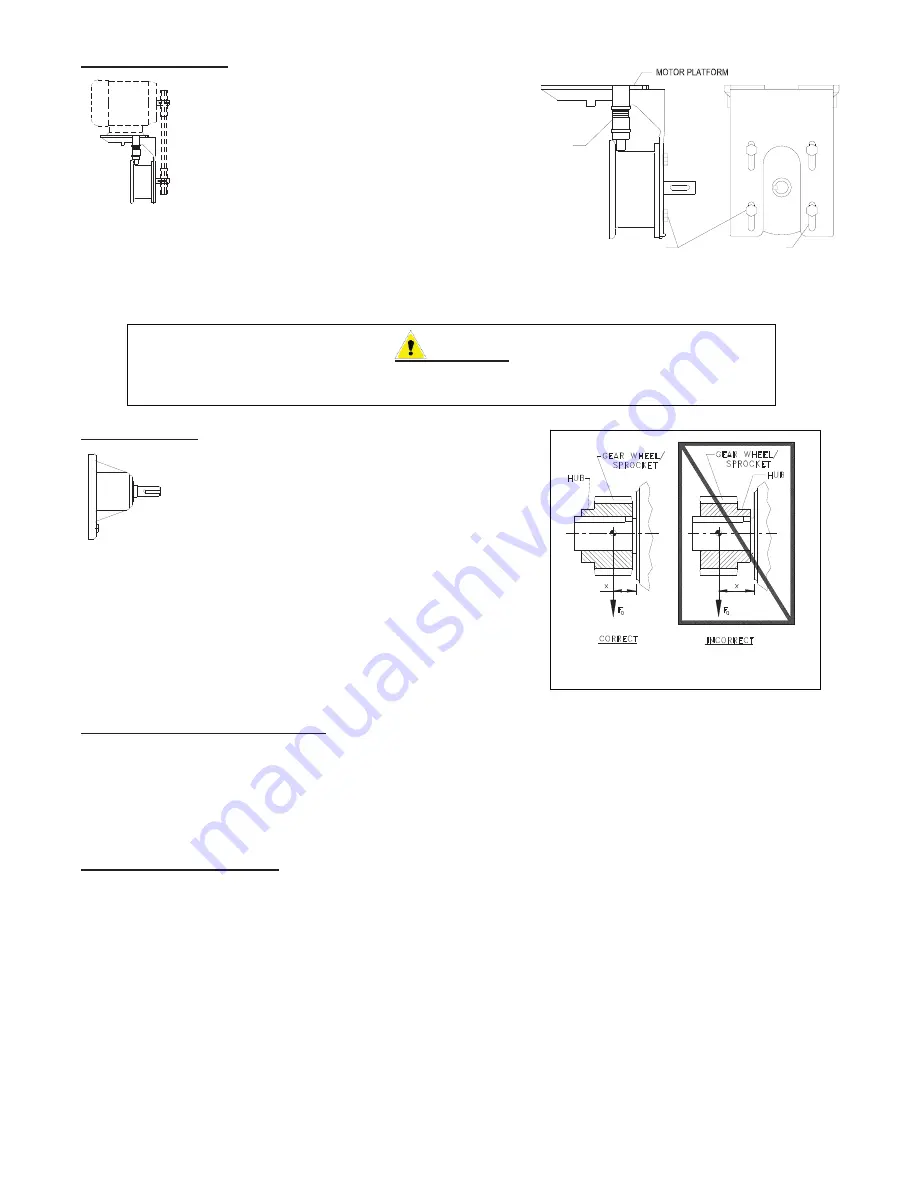
BIM 1009/2007/09
Page 4 of 8
www.nord.com
Figure 1.
Mounting a coupling or a sprocket
on a shaft.
MK Motor Mount Platform
For proper installation of the belt drive, consult the V-belts
manufacturer. NORD MK motor mounts are adjustable in
two ways. Slotted holes are provided at the input cylinder
for the initial height adjustment. There are two fine
adjustments at the Yolk to increase/decrease tension.
Two Spanner head wrenches will be needed to
tighten/loosen the fine adjustments. The four bolts
holding the motor platform to the input cylinder must be
loosened in order to use the fine adjustments.
The motor mounting platform has tapped holes to accept the foot pattern of the
standard footed NEMA or IEC motor. All MK mounting input shaft diameters
are metric.
Align the sheaves or sprockets square and paraIIeI by placing a straight edge across their faces. Alignment of bushed sheaves and sprockets
should be checked after bushings have been tightened. Check horizontal shaft alignment by placing a IeveI vertically against the face of the
sheave or sprocket. Adjust beIt or chain tension per the manufacturer’s specified procedure. After a period of operation, recheck alignment
and adjust as required.
Solid Shaft (W-Type)
The shaft will be inch or metric, depending on how the unit was
ordered. Measure and verify the shaft before mounting anything
on the shaft. Below are the tolerances used for the solid shafts.
All solid input shafts have a tapped hole on the end for customer
use. The chart below indicated the tap size for each shaft. Keys
are also supplied with solid shaft.
Outboard pinion and sprocket fits should be as recommended by the manufacturer.
The components should be heated according to the manufacturer’s
recommendations, generaIIy 250
q
F to 300
q
F, (120
q
C to 150
q
C) before assembling to
the shaft. The coupling hub or sprocket should be mounted per Figure 1.
On larger gearboxes, there is grease fitting on the W-Type inputs to grease the
outboard bearing. About 0.75 ounce (20 - 25g) of synthetic grease should be added
every 1,000 service hours. There is a sticker adjacent to the grease fitting detailing
which grease should be used.
The standard bearing grease is Kluber Petamo
GHY 133N synthetic grease. Bearings should be re-greased with a compatible
product.
Output and Input Shaft Diameter Tolerance
Metric (mm)
d
18 = +0.012/+0.001
!
18
d
30 = +0.015/+0.002
!
30
d
50 = +0.018/+0.002
!
50
d
80 = +0.030/+0.011
!
80
d
120 = +0.035/+0.013
!
120
d
180 = +0.040/+0.015
Inch
d
1.750 = +0.0000/-0.0005
!
1.750 = +0.0000/-0.0010
Solid Shaft DriII and Tap Shaft End
Metric (mm)
d
16 = M5
!
16
d
21 = M6
!
21
d
24 = M8
!
24
d
30 = M10
!
30
d
38 = M12
!
38
d
50 = M16
!
50
d
85 = M20
!
85
d
130 = M24
Inch
d
0.500 = #10-24 x 0.4 deep
!
0.500
d
0.875 = ¼-20 x 0.6 deep
!
0.875
d
0.938 = 5/16-18 x 0.7 deep
!
0.938
d
1.100 = 3/8-16 x 0.9 deep
!
1.100
d
1.300 = 1/2-13 x 1.1 deep
!
1.300
d
1.875 = 5/8-11 x 1.4 deep
!
1.875
d
3.500 = 3/4-10 x 1.7 deep
!
3.500 = 1-8 x 2.2 deep
WARNING:
NORD Gear does not furnish the safety guards for the traction mechanism. It is the
responsibility of the customer to install a safety guard to conform to OSHA standards.
YOKE
(FINE ADJUSTMENT)
BOLTS (4)
SLOTTED HOLES (4)
Summary of Contents for BTR Series
Page 2: ...THIS PAGE IS INTENTIONALLY LEFT BLANK...
Page 4: ......
Page 27: ...THIS PAGE IS INTENTIONALLY LEFT BLANK...
Page 28: ......