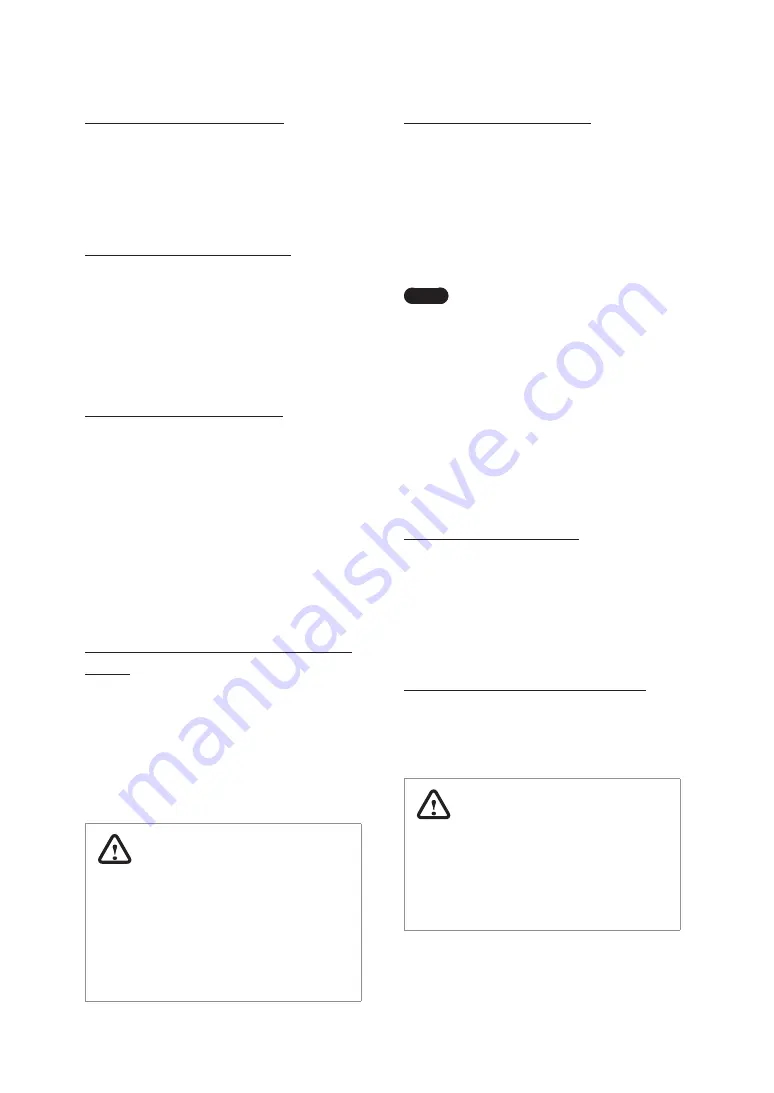
20 Maintaining the Boiler
Checking the Water System
1. Verify all system components are correctly
installed and operational.
2. Check the cold fill pressure for the system. Verify
it is correct (must be a minimum of 12 psi).
3. Watch the system pressure as the boiler heats
up (during testing) to ensure pressure does not
rise too high.
Note
●
If the system contains glycol,
test for proper concentration as
recommended by manufacturer.
●
Excessive pressure rise indicates
expansion tank sizing or performance
problem.
4. Inspect automatic air vents and air separators.
Remove air vent caps and briefly press push
valve to flush vent.
5. Replace caps. Make sure vents do not leak.
Replace any leaking vents.
Checking Expansion Tank
●
Expansion tanks provide space for water to move
in and out as the heating system water expands
due to temperature increase or contracts as the
water cools.
●
Perform annual checks as recommended by
manufacturer to ensure proper operation.
Checking the Pressure Relief Valves
1. Inspect the relief valve and lift the lever to verify
flow. Before operating any relief valve, ensure
that it is piped with its discharge in a safe area to
avoid severe scald potential.
WARNING
Explosion Hazard
A dripping or leaking pressure relief valve must
be replaced. Do not plug or remove the valve.
Failure to follow these instructions can result in
fire or explosion, and personal injury or death.
Inspecting the Boiler Interior
1. Remove the front cover and inspect the interior
of the boiler.
2. Vacuum any sediment from inside the boiler
and components. Remove any obstructions.
Cleaning the Condensate Trap
1. Inspect the condensate drain line, condensate
fittings, and condensate trap.
2. Remove any sediment in the trap.
3. Fill with fresh water until the water begins to
pour out of the drain.
Checking all Piping for Leaks
Eliminate all system or boiler leaks. Continual fresh
makeup water will reduce boiler life. Minerals
can build up in sections, reducing heat transfer,
overheating heat exchanger, and causing heat
exchanger failure. Leaking water may also cause
severe property damage.
1. Inspect all water and gas piping and verify to be
leak free.
2. Look for signs of leaking lines and correct any
problems found.
Checking the Flue Vent System and Air
Piping
1. Visually inspect the entire flue gas venting
system and air piping for blockage,
deterioration or leakage. Repair any joints that
show signs of leakage. Verify that air inlet pipe is
connected and properly sealed (if installed).
2. Verify that boiler vent discharge and air intake
are clean and free of obstructions.
WARNING
●
Failure to inspect for the above conditions
and have them repaired can result in severe
personal injury or death.
●
Do not operate the boiler if the intake or
exhaust pipe is displaced, has holes, is
clogged, or is corroded.
Summary of Contents for NCB-190/060H
Page 29: ...Memo ...
Page 30: ......