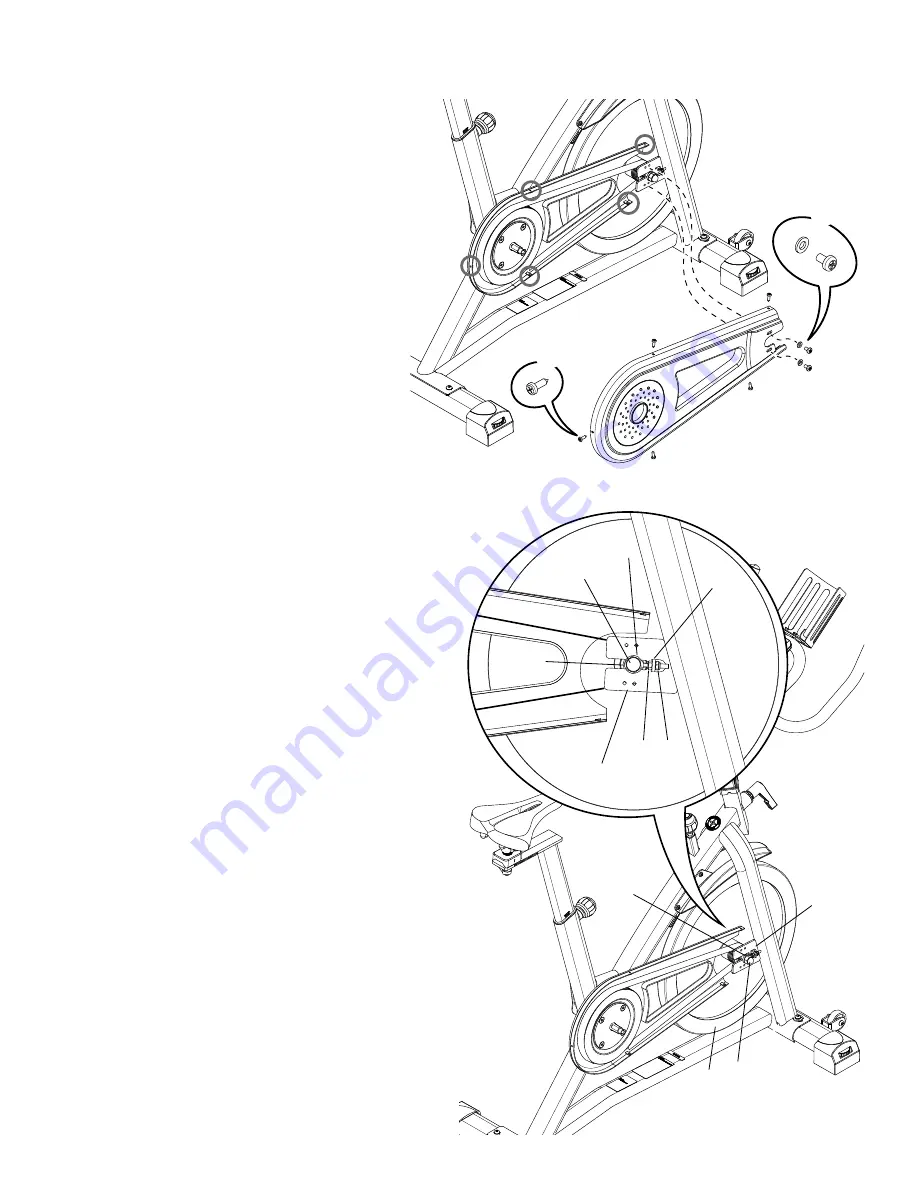
46
X5
X2
9.
Loosen and remove the hardware that attaches the Drive Belt Cover
to the Drive Belt Inside. Carefully remove the Drive Belt Cover and set it
safely aside for reassembly.
10.
0DUNWKHSRVLWLRQRIWKH)O\ZKHHO7HQVLRQHUV*RQWKHÀ\ZKHHO
brackets (H) on the Frame. Record the number of threads showing on
the Tensioner eyebolt on each side of the Tensioner support (H1) on the
bracket.
G
I
+
+
G
I
J
+
L
K1
K2