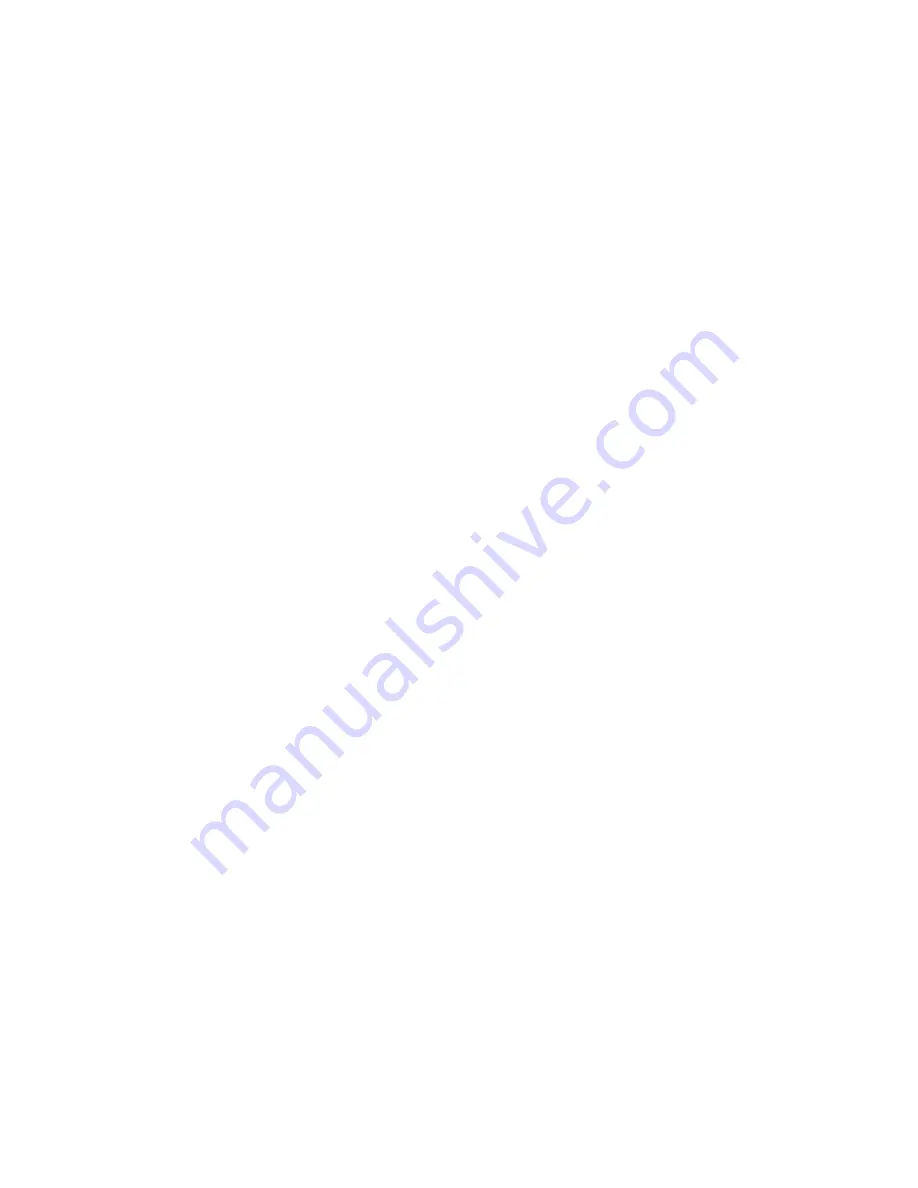
12 000 WATT AM BROADCAST TRANSMITTER
XL12
Page 2-7
01 January 2002
2.1.8.5 System Reset:
The
system reset
circuit
generates reset pulses which are applied to the
AC/DC power, exciter and RF power stages. It also
resets any alarm circuit that is/was latched in its
alarm state. It must be configured to be controlled
by a single ended input (see figure 2-1) or by a
differential input (see figure 2-2). The
SYSTEM RESET
terminals are TB2-1(+) and TB2-2(-). The
associated 3-pin header/2-socket shunt post on the
remote interface PWB is E13.
2.1.8.6 Alarm Recall:
The
alarm recall
circuit
allows the user to reinstate an active remote alarm
condition for any alarm(s) that caused the last RF
shutback and is not currently being displayed or
affecting the RF output. It must be configured to be
controlled by a single ended input (see figure 2-1) or
by a differential input (see figure 2-2). The
ALARM
RECALL
terminals are TB2-3(+) and TB2-4(-). The
associated 3-pin header/2-socket shunt post on the
remote interface PWB is E14.
2.1.9 OTHER REMOTE CONTROLS:
An
RF inhibit control can be connected, at the user's
discretion. This input will influence the transmitter's
RF output regardless of the selected control location
(
LOCAL
or
REMOTE
).
2.1.9.1 External PDM (RF) Inhibit Control:
The external PDM inhibit circuit reduces the 'on'
time of the PDM signal to near zero, effectively
turning off the RF output (a residual RF leak of
approximately 10 watts may be present) the instant
an active condition is applied. This state is
maintained as long as the active condition exists. It
must be configured to be controlled by a single ended
input (see figure 2-1) or by a differential input (see
figure 2-2).
PDM INHIBIT
terminals are TB2-5(+) and
TB2-6(-). The associated 3-pin header/2-socket
shunt post on the remote interface PWB is E15.
NOTE
The external PDM inhibit input is intended to be used
in conjunction with antenna switching circuitry to
ensure minimal RF output current flows during
opening/closing of contacts in the transmitter's RF
feed cable. An active 'PDM inhibit' condition must be
applied prior to contact opening (disconnecting the RF
load) and must be maintained until contact closure has
occurred and an appropriate impedance has been
connected to the transmitter's RF output. The RF
output will be instantly restored to its original level
when the active condition is removed.
2.1.10 RF PERFORMANCE MONITORING:
The transmitter provides outputs to monitor RF
performance. They include DC voltages which are
representative of the forward power level, the
reflected power level and the DC voltage being
applied to the RF amplifiers. In addition, a true RF
sample of the RF output's voltage waveform is
available for external monitoring. These outputs are
available on the remote interface PWB.
2.1.10.1 RF Monitor Sample :
A true sample of
the RF output's voltage waveform, including its
modulation envelope, is provided at a BNC connector
(
RF MONITOR
) on the remote interface PWB. The
RF
monitor
output is intended to be applied to a station
modulation monitor with a 50-ohm input impedance.
It may also be monitored by an oscilloscope during
maintenance procedures. The
RF monitor
output
can be set to provide 5.0 volts RMS for each preset
power level, provided the power levels are preset to
a level between 1000 and 12 000 watts.
2.1.10.2 Forward Power Level:
A buffered DC
voltage that is representative of the forward power
level is available on TB4-1 (
BFRD FWD PWR
) [TB4-2
(
GND
) is the return path]. This voltage is a non-linear
(square law) function and will be 13.7 ±0.5 VDC
when the forward power is 12 000 watts. The
impedance of the monitoring circuit must be greater
than 1000 ohms.
2.1.10.3 Reflected Power Level:
A buffered
DC voltage that is representative of the reflected
power level is available on TB4-3 (
BFRD REFLD PWR
)
[TB4-2 (
GND
) is the return path]. This voltage is a
non-linear (square law) function and will be
5.25 ±0.5 VDC when the reflected power is 1500
watts. The impedance of the monitoring circuit must
be greater than 1000 ohms.
2.1.10.4 Power Amplifier Volts:
A buffered DC
voltage that is directly proportional to the DC voltage
being applied to the RF amplifiers in the RF power
modules is available on TB4-5 (
BFRD PA VOLTS
)
[TB4-4 (
GND
) is the return path]. This voltage will be
2.85 VDC when the DC voltage being applied to the
RF amplifiers is 129 VDC. The impedance of the
monitoring circuit must be greater than 1000 ohms.
Summary of Contents for XL12
Page 194: ...Figure SD 2 Electrical Schematic Exciter Stage Page SD 2 01 January 2002...
Page 195: ...Figure SD 3 Electrical Schematic RF Drive Stage Page SD 3 01 January 2002...
Page 196: ...Figure SD 4 Electrical Schematic RF Power Stage Page SD 4 01 January 2002...
Page 197: ...Figure SD 5 Electrical Schematic Control Monitor Functions Page SD 5 01 January 2002...
Page 198: ...Figure SD 6 Electrical Schematic AC DC Power Stage Page SD 6 01 January 2002...
Page 199: ...Figure SD 7 Electrical Schematic Remote Interface PWB NAPI25A Page SD 7 01 January 2002...
Page 200: ...Figure SD 8 Electrical Schematic Exciter Interface PWB NAPI22E Page SD 8 01 January 2002...
Page 201: ...Figure SD 9 Electrical Schematic RF Drive Tuning PWB NAPI60 Page SD 9 01 January 2002...
Page 202: ...Figure SD 10 Electrical Schematic Distribution PWB NAPI50B Page SD 10 01 January 2002...
Page 203: ...Figure SD 11 Electrical Schematic DC Power Supply PWB NAPS16C Page SD 11 01 January 2002...
Page 210: ...Figure MD 3 Assembly Detail NAC101 Control Monitor Panel Page MD 3 01 January 2002...
Page 212: ...Figure MD 5 Assembly Detail NAPI25A Remote Interface PWB Page MD 5 01 January 2002...
Page 213: ...Figure MD 6 Assembly Detail NAE73A Exciter Panel Page MD 6 01 January 2002...
Page 214: ...Figure MD 7 Assembly Detail NAPI22E Exciter Interface PWB Page MD 7 01 January 2002...
Page 215: ...Figure MD 8 Assembly Detail NAE83 RF Drive Panel Page MD 8 01 January 2002...
Page 216: ...Figure MD 9 Assembly Detail NAAA02 RF Drive Amplifier Page MD 9 01 January 2002...
Page 219: ...Figure MD 11 Assembly Detail NAPS10B Regulated Power Supply PWB Page MD 11 01 January 2002...
Page 220: ...Figure MD 12 Assembly Detail NAPI50B Distribution PWB Page MD 12 01 January 2002...
Page 221: ...Figure MD 13 Assembly Detail Fan Tray P N 183 8350 Page MD 13 01 January 2002...
Page 222: ...Figure MD 14 Assembly Detail NAF102 RF Output Filter Top View Page MD 14 01 January 2002...
Page 223: ...Figure MD 15 Assembly Detail NAF102 RF Output Filter Rear View Page MD 15 01 January 2002...
Page 224: ...Figure MD 16 Assembly Detail NAFP90 Forward Reflected Power Probe Page MD 16 01 January 2002...
Page 225: ...Figure MD 17 Assembly Detail NAX161 Static Drain Choke Page MD 17 01 January 2002...
Page 228: ...Figure MD 20 Assembly Detail NAPP02 RF Current Probe PWB Page MD 20 01 January 2002...
Page 229: ...Figure MD 21 Assembly Detail Capacitive Divider Assembly 176 8253 Page MD 21 01 January 2002...
Page 231: ...Figure MD 23 Assembly Detail NASR108 AC DC Power Supply Top View Page MD 23 01 January 2002...
Page 232: ...Figure MD 24 Assembly Detail NASR105 01 Power Transformer Assembly Page MD 24 01 January 2002...
Page 233: ...Figure MD 25 Assembly Detail 3 Rectifier UP28 Page MD 25 01 January 2002...
Page 234: ...Figure MD 26 Assembly Detail NAPS16C DC Power Supply PWB Page MD 26 01 January 2002...
Page 235: ...Figure MD 27 Assembly Detail NAPI48B DC Power Supply Monitor PWB Page MD 27 01 January 2002...