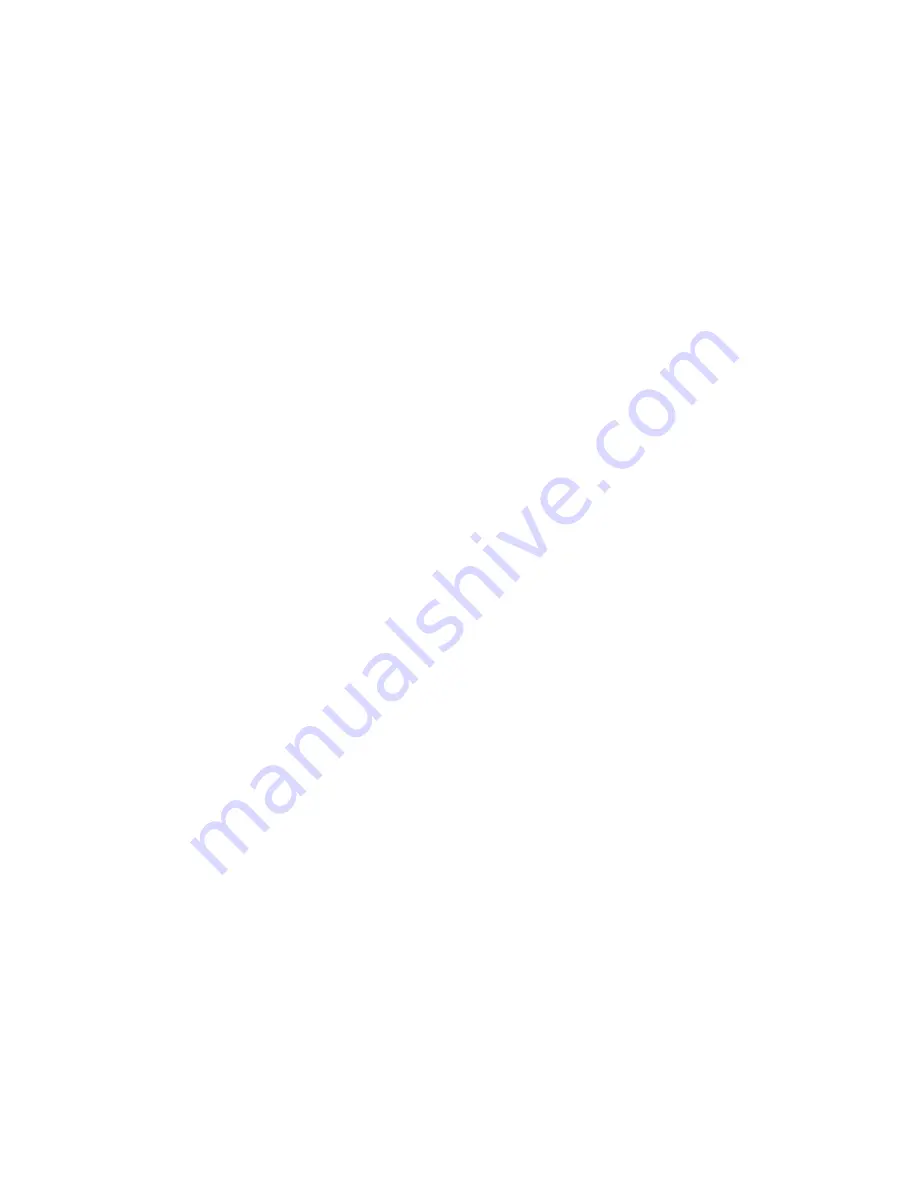
4
www.national.com
3.0 Quick Start
Refer to Figure 1 for locations of the power
connection, signal input and USB port.
IMPORTANT NOTE:
Install the Wavevision 4 Software before
connecting this product to the PC. See
Appendix B – Installing Wavevision.
For quick start operation:
1. Connect the 12V DC power source
(included with the development board) to the
rear Power Connector labeled (8-12V DC).
2. Connect a stable sine wave source capable
of supplying the desired input frequencies at
up to 8 dBm. Connect this signal to the front
panel SMA connector labeled “I CH.”
through a band pass filter. The exact level
needed from the generator will
depend upon
the insertion loss of the filter used.
3 Connect the USB cable (included) from the
USB port to the PC. If this is the first time
the board has been connected, Windows
may install the drivers for this product at this
time.
5. Push the Power Switch to the ON position
on the rear panel and check that the Green
LED between the switch and the power
connector illuminates.
6. Start the Wavevision 4 Software
7. Once loaded the “Firmware Download”
Progress bar should be displayed. See
Appendix B for more information.
8. Upon Firmware Download completion, the
control panel for the board should
automatically be displayed on the PC and
the CLK LED on the front panel should be
flashing.
8. Set the signal source for the analog input to
8 dBm at the desired frequency. Observe
the ‘Out of Range’ LED “OVR” on the front
panel is illuminated. If this LED is not on,
increase the input signal source until it is.
9. Reduce the input level until the ‘OVR’ LED
just turns off.
10. From the Wavevision 4 pull-down menu
select “Acquire” and then samples. The
system will then capture the input waveform
and display the results in the time domain.
11. For FFT Analysis click the FFT Tab.
4.0 Functional Description
The ADC081500 Development Board schematic
is shown in Section 7.0.
4.1 Input circuitry
The input signal(s) to be digitized should be
applied to the front panel SMA connectors
labeled “I CH.” and “Q CH.”. These 50 Ohm
inputs are intended to accept a low-noise sine
wave signals. To accurately evaluate the
dynamic performance of this converter, the input
test signals will have to be passed through a
high-quality bandpass filter with at least 10-bit
equivalent noise and distortion characteristics.
This evaluation board as delivered is set up for
operation with two single-ended analog inputs,
which are converted to differential signals on
board.
Signal transformer T2, is connected as a balun,
and provides the single-ended to differential
conversion. The differential PCB traces to the
ADC analog input pins have a characteristic
differential impedance of 100 Ohms.
No scope or other test equipment should be
connected anywhere in the signal path while
gathering data.
4.2 ADC reference
The ADC081500 has an internal reference that
can not be adjusted. However, the Full-Scale
(differential) Range may adjusted with the
Software Control Panel Refer to Section 9.0 for
more information
4.3 ADC clock
The ADC clock is supplied on board and is fixed
at 1.5GHz. An external clock signal may be
applied to the ADC through the SMA Connector
labeled “CLOCK” on the front panel. The balun-
transformer (T1) converts the single ended clock
source to a differential signal to drive the ADC
clock pins
Note that it is very important that the ADC clock
should be as free of jitter as possible or the
apparent SNR of the ADC081500 will be
compromised.
4.4 Digital Data Output
The digital output data from the ADC081500 is
connected to a Xilinx 4 FPGA. Up to 4K Bytes of
data can be stored and then uploaded over the
USB interface to the Wavevision 4 software. The
FPGA logic usage is low allowing further code to
be written and tested for product development.
Summary of Contents for ADC081500DEV
Page 6: ...6 www national com 7 0 Schematic Drawing ADC081500DEV Onboard Clock VCO PLL ...
Page 7: ...7 www national com 7 1 Schematic Drawing ADC081500DEV Analog Inputs I Q Digital Trigger Input ...
Page 8: ...8 www national com 7 2 Schematic Drawing ADC081500DEV ADC connected to Virtex4 FPGA ...
Page 9: ...9 www national com 7 3 Schematic Drawing ADC081500DEV USB Interface ...
Page 10: ...10 www national com 7 4 Schematic Drawing ADC081500DEV Power Supplies 1 ...
Page 11: ...11 www national com 7 5 Schematic Drawing ADC081500DEV Power Supplies 2 ...
Page 12: ...12 www national com 7 6 Schematic Drawing ADC081500DEV Expansion Header Interface ...
Page 13: ...13 www national com 8 0 Bill of Materials Page 1 of 2 ...
Page 14: ...14 www national com 8 1 Bill of Material Page 2 of 2 ...
Page 22: ...22 www national com 10 3 System Block Diagram ...