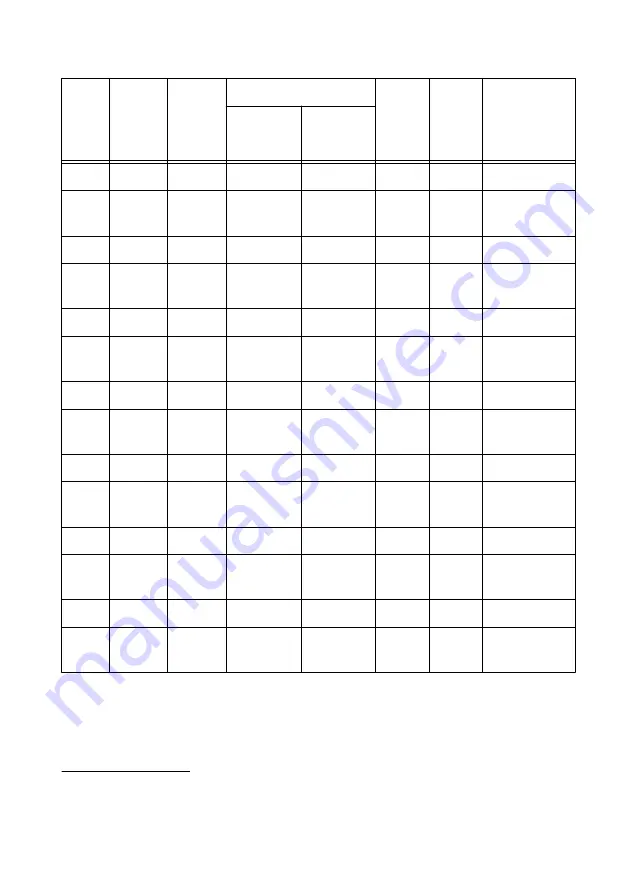
Table 6. 1 M
Ω
Bandwidth Verification
Config
Sample
Rate
(S/s)
Vertical
Range
(V
pk-pk
)
Test Point
As-
Found
Limits
(dB)
As-Left
Limits
(dB)
Measurement
Uncertainty
(dB)
4
Frequency
(MHz)
Amplitude
(dBm)
1
125 M
0.2
0.05
-13
—
—
—
2
250 M
0.2
98.1
-13
-3.0 to
1.0
-2.5 to
0.9
±0.134
3
125 M
0.7
0.05
-2.1
—
—
—
4
250 M
0.7
98.1
-2.1
-3.0 to
1.0
-2.5 to
0.9
±0.133
5
125 M
1.4
0.05
3.9
—
—
—
6
250 M
1.4
98.1
3.9
-3.0 to
1.0
-2.5 to
0.9
±0.134
7
125 M
5
0.05
9
—
—
—
8
250 M
5
98.1
9
-3.0 to
1.0
-2.5 to
0.9
±0.133
9
125 M
10
0.05
9
—
—
—
10
250 M
10
98.1
9
-3.0 to
1.0
-2.5 to
0.9
±0.134
11
125 M
40
0.05
9
—
—
—
12
250 M
40
98.1
9
-3.0 to
1.0
-2.5 to
0.9
±0.134
13
125 M
80
0.05
9
—
—
—
14
250 M
80
98.1
9
-3.0 to
1.0
-2.5 to
0.9
±0.134
4
Measurement uncertainty is based on the following equipment and conditions:
•
Rohde & Schwarz NRP-Z91 at 20 °C to 25 °C.
•
Harmonics from the signal generator are less than -30 dBc.
26
|
ni.com
|
PXIe-5172 Calibration Procedure