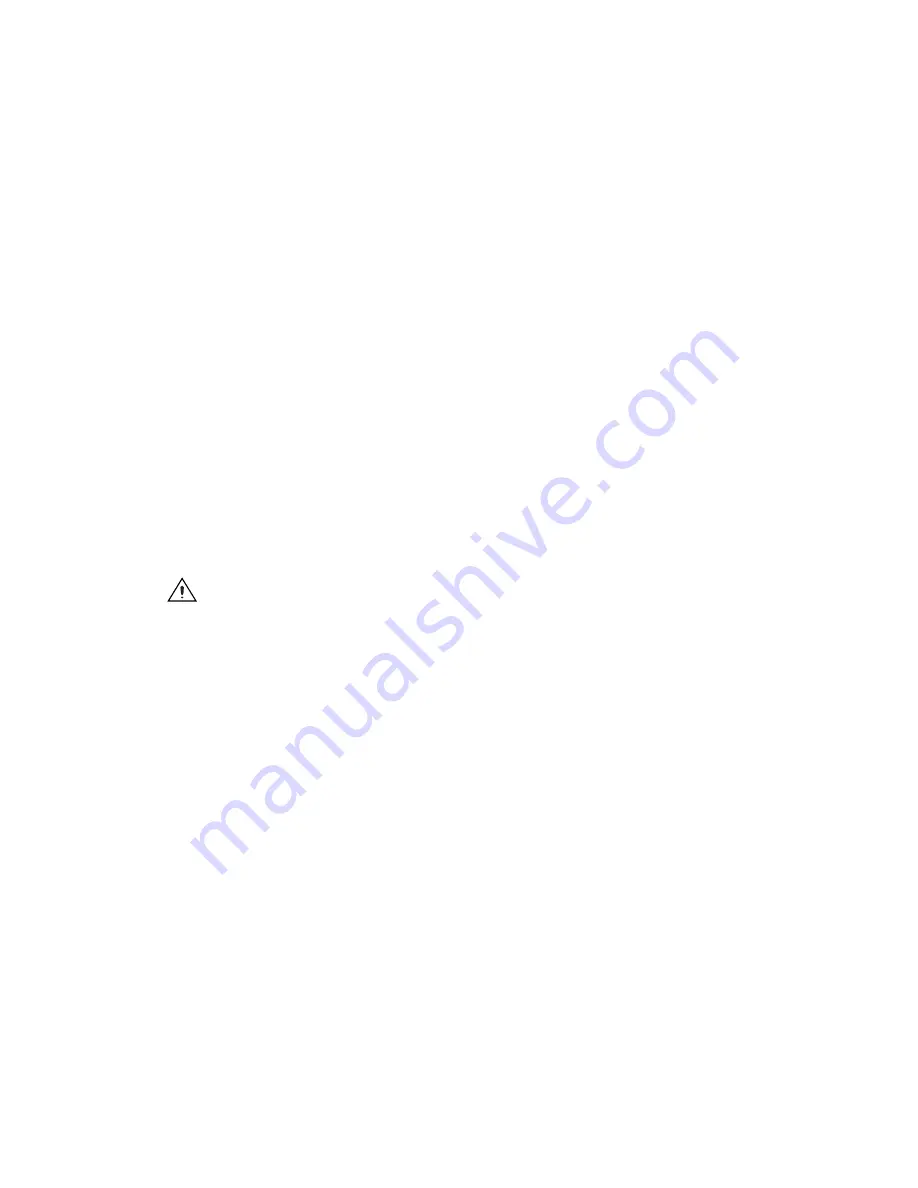
©
National Instruments Corporation
21
nuDrive Accessory User Guide
First, calculate the current gain and the resistor values needed to achieve
that gain:
So, you would use the closest resistor value below 78.1 k
Ω
for resistors R6
and R7.
Then, calculate the values for R40 and R42 as follows:
So, you would use the closest resistor values below 4.7 k
Ω
and 1 k
Ω
for
resistors R42 and R40 respectively.
Caution
Do not solder or unsolder the resistors on the servo amplifiers. Trim the leads to
the proper length, bend them at 90°, and plug them into the sockets.
Balancing the Amplifier Gain
The balance (DC offset) of the amplifier is trimmed to zero at the factory.
If you change the current gain and/or current limits settings, it may be
necessary to balance the amplifier again. If any motor tends to rotate slowly
after it is killed by the ValueMotion or FlexMotion servo controller, you
may need to balance the corresponding amplifier.
Figure 20 shows the location of the resistors and trimpots on your
SSA-8/100 board.
Gain
I
peak
V
max
-----------
6.4
10
-------
0.64
=
=
=
R
6 7
,
50
Gain
-------------
50
0.64
·
----------
78.1
=
=
=
R42
10
I
peak
×
20
I
peak
–
-----------------------
10
6.4
×
20
6.4
–
-------------------
4.7
=
=
=
R40
2
I
cont
×
8
I
cont
–
-------------------
2
2.7
×
8
2.7
–
----------------
1
=
=
=
Summary of Contents for nuDrive 2CF-001
Page 32: ......