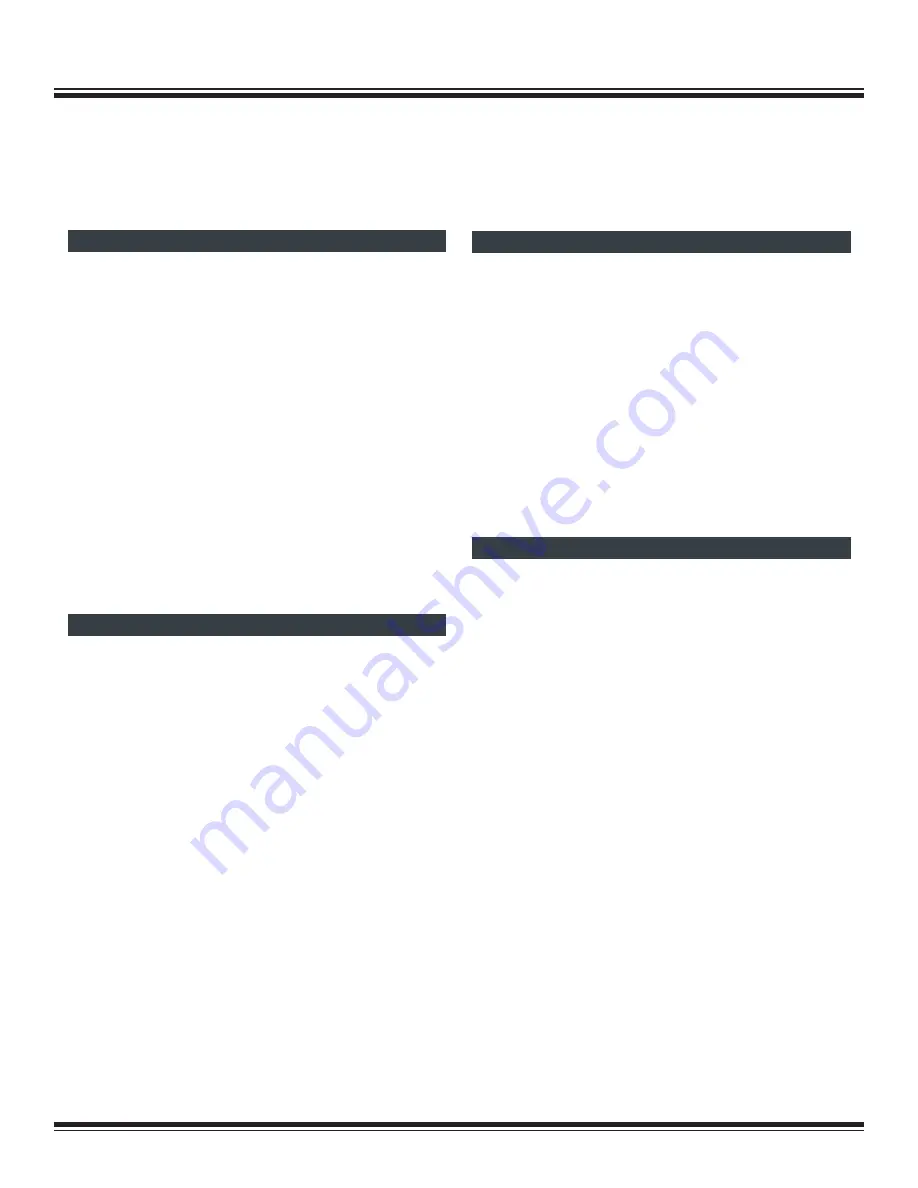
Safety
Environment
Avoid use in dangerous environments.
Do not use in rain, damp or wet locations, or in the presence of
explosive atmospheres (gaseous fumes, dust, or flammable mate
-
rials). Remove materials or debris that may be ignited by sparks.
Keep work area tidy and well-lit - a cluttered or dark work area may
lead to accidents. Extreme heat or cold may affect performance.
Protect others in the work area and be aware of surroundings.
Provide barriers or shields as needed to protect others from debris
and machine operation. Children and other bystanders should be
kept at a safe distance from the work area to avoid distracting the
operator and/or coming into contact with the machine. Operator
should be aware of who is around them and their proximity. Sup
-
port personnel should never stand next to, in front of, or behind
the machine while the machine is running. Operator should look
behind them before backing up.
Do not come within 3 ft. of the machine’s perimeter during
operation.
Guard against electric shock.
Ensure that machine is connected to a properly grounded outlet.
Prevent bodily contact with grounded surfaces, e.g. pipes, radia
-
tors, ranges, and refrigerators. When scoring or making cuts,
always check the work area for hidden wires or pipes.
6
GENERAL RULES FOR SAFE OPERATION
Before use, anyone operating or performing maintenance on this equipment must read and understand this manual, as well as any labels pack-
aged with or attached to the machine and its components. Read the manual carefully to learn equipment applications and limitations, as well
as potential hazards associated with this type of equipment. Keep manual near machine at all times. If your manual is lost or damaged, contact
National Flooring Equipment (NFE) for a replacement.
Personal
Dress properly and use safety gear.
Do not wear loose clothing; it may be caught in moving parts.
Anyone in the work area must wear safety goggles or glasses and
hearing protection. Wear a dust mask for dusty operations. Hard
hats, face shields, safety shoes, etc. should be worn when speci-
fied or necessary.
Maintain control; stay alert.
Keep proper footing and balance, and maintain a firm grip. Ob
-
serve surroundings at all times. Do not use when tired, distracted,
or under the influence of drugs, alcohol, or any medication that
may cause decreased control.
Keep hands away from all moving parts and tooling.
Wear gloves when changing tooling. Remove tooling when ma-
chine is not in use and/or lower cutting head to the floor.
Do not force equipment.
Equipment will perform best at the rate for which it was designed.
Excessive force only causes operator fatigue, increased wear, and
reduced control.
Equipment
Use proper parts and accessories.
Only use NFE-approved or recommended parts and accessories.
Using any that are not recommended may be hazardous.
Ensure accessories are properly installed and maintained.
Do not permanently remove a guard or other safety device when
installing an accessory or attachment.
Inspect for damaged parts.
Check for misalignment, binding of moving parts, loose fasteners,
improper mounting, broken parts, and any other conditions that
may affect operation. If abnormal noise or vibration occurs, turn
the machine off immediately. Do not use damaged equipment until
repaired. Do not use if power switch does not turn machine on and
off. For all repairs, insist on only identical NFE replacement parts.
Maintain equipment and labels.
Keep handles dry, clean, and free from oil and grease. Keep cut-
ting edges sharp and clean. Follow instructions for lubricating and
changing accessories. Motor and switches should be completely
enclosed at all times with no exposed wiring. Inspect cord regu-
larly. Labels carry important information; if unreadable or missing,
contact NFE for a free replacement.
Avoid accidental starting; store idle equipment.
When not in use, ensure that the machine is unplugged and
breaker is set to OFF. Store in a dry, secured place. Remove tool
-
ing when storing, and keep away from children.
Maintenance & Repairs
Begin maintenance work only when the machine is shut
down, unplugged, and cooled down.
Use proper cleaning agents.
Ensure that all cleaning rags are fiber-free; do not use any aggres
-
sive cleaning products.
Schedule regular maintenance check-ups.
Ensure machine is properly cleaned and serviced. Remove all
traces of oil, combustible fuel, or cleaning fluids from the machine
and its connections and fittings. Retighten all loose fittings found
during maintenance and repair work. Loose or damaged parts
should be replaced immediately; use only NFE parts.
Do not weld or flame-cut on the machine during repairs, or
make changes to machine without authorization from NFE.
406746_6700_RevC