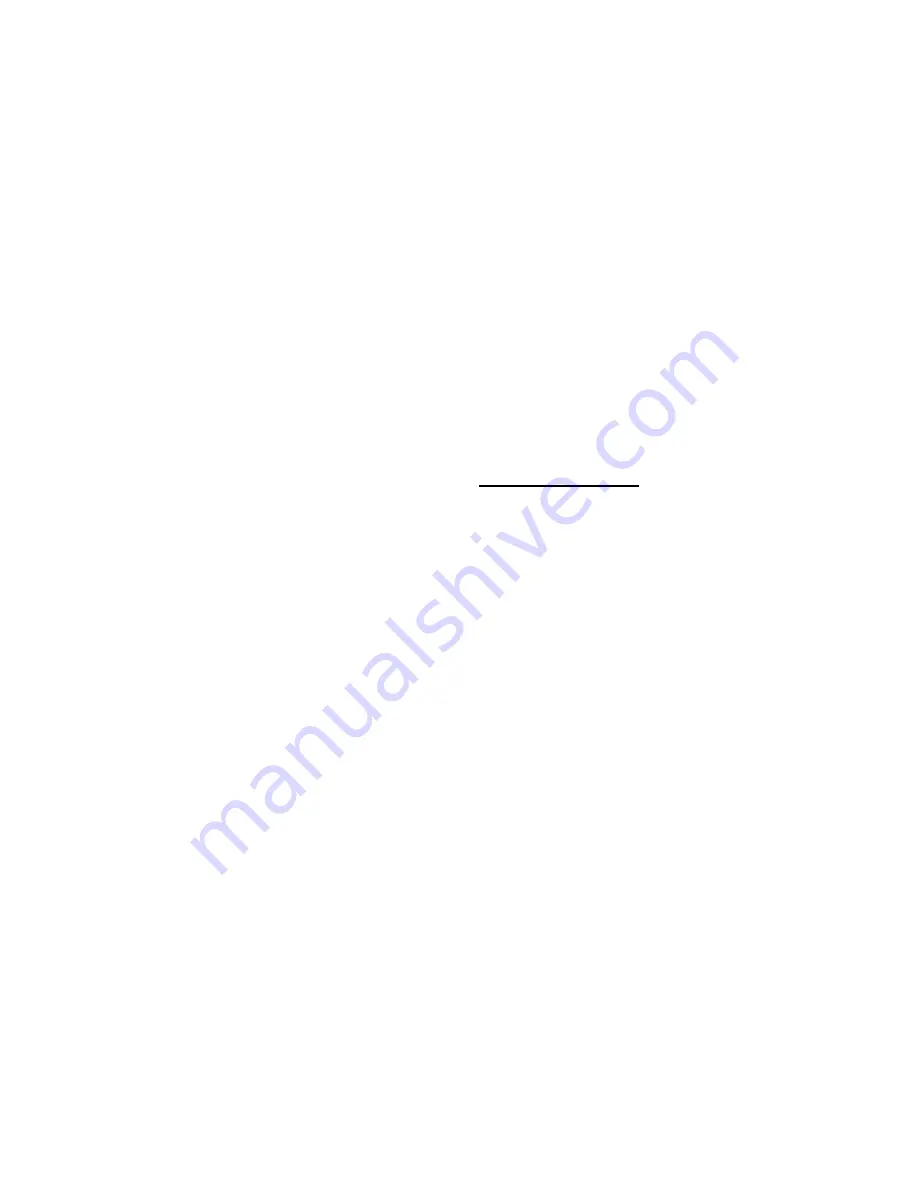
21
exchanger can be checked by locating a mirror
under the burners with a flashlight. An alternate
method is to remove the venting and top panel as
necessary to inspect from above. Also check the
vent system for defects at this time.
a.
If cleaning is required, shut off all electrical
and gas supply to the heater.
b.
To expose the heat exchanger:
Indoor Models:
Remove flue pipe, top of unit, rear upper jacket,
flue collector rear panel and heat exchanger
baffles.
Outdoor Models:
Remove vent top assembly, rear upper jacket,
flue collector rear panel and heat exchanger
baffles.
c.
Remove all burners:
It is usually more convenient to remove the
burner tray assembly. Disconnect sensor wire,
ignition cable (or thermocouple generator) and
pilot gas line. Disconnect manifold inlet union(s).
Remove the four (4) retaining screws. Grasp
burner/pilot assembly firmly at the front. Push it
back, disengaging it from the gas orifice. Lower
the front of the burner (to avoid damaging pilot
shield) then remove the burner tray.
CAUTION: Black carbon or green soot on a dirty
heat exchanger can, under certain conditions, be
ignited by a random spark or open flame. To prevent
this unlikely occurrence, dampen the soot deposits
with wet brush or fine water spray before servicing or
cleaning the heat exchanger.
With a wire brush, remove soot and loose scale from
heat exchanger. Clean fallen debris from bottom of
heater. Make sure burner ports are clear and pilot
assembly is free of debris.
d.
Reassemble in reverse order:
Be sure the heat exchanger baffles are
replaced.
8.
The gas and electric controls installed on heaters
are engineered for both dependable operation
and long life, but the safety of this equipment
completely depends on their proper functioning.
It is strongly recommended that the basic items
be checked by a competent serviceman every
year and replaced when necessary. The basic
controls are:
a.
Water temperature controls.
b.
Pilot safety system.
c.
Automatic electric gas valve(s).
d.
Flow sensing safety device.
9.
Low water cutoffs should be inspected every six
(6) months, including flushing of float types.
NOTE: Warranty does not cover any damage caused
by lack of required maintenance or improper operating
practices.
10. Both modulating and stage valve are adjusted at
the factory for minimum permissible rates and
should not be readjusted.
Section 5
Troubleshooting and
Analysis of Service
Problems
1.
For proper service and problem diagnosis of the
heater and heater system, the following tools are
required:
a.
Gas pressure test kit with range from zero to
14 W.C. Either a slack tub manometer or an
accurate gas pressure gauge is acceptable
with proper adapters which will connect to the
available fittings in the line and on the gas
valve.
b.
Multi-meter with the following ranges:
0 to 500 volts A.C.
0 to 1000 ohms continuity.
c.
Tube cleaning kit consisting of reamer,
stainless steel brush, speed handle and
handle extensions.
d.
Heater thermometer (with 1/2" NPT well)
100-240F.
2.
In addition, the heater should be equipped with a
system pressure gauge with proper ranges for
heater operation.