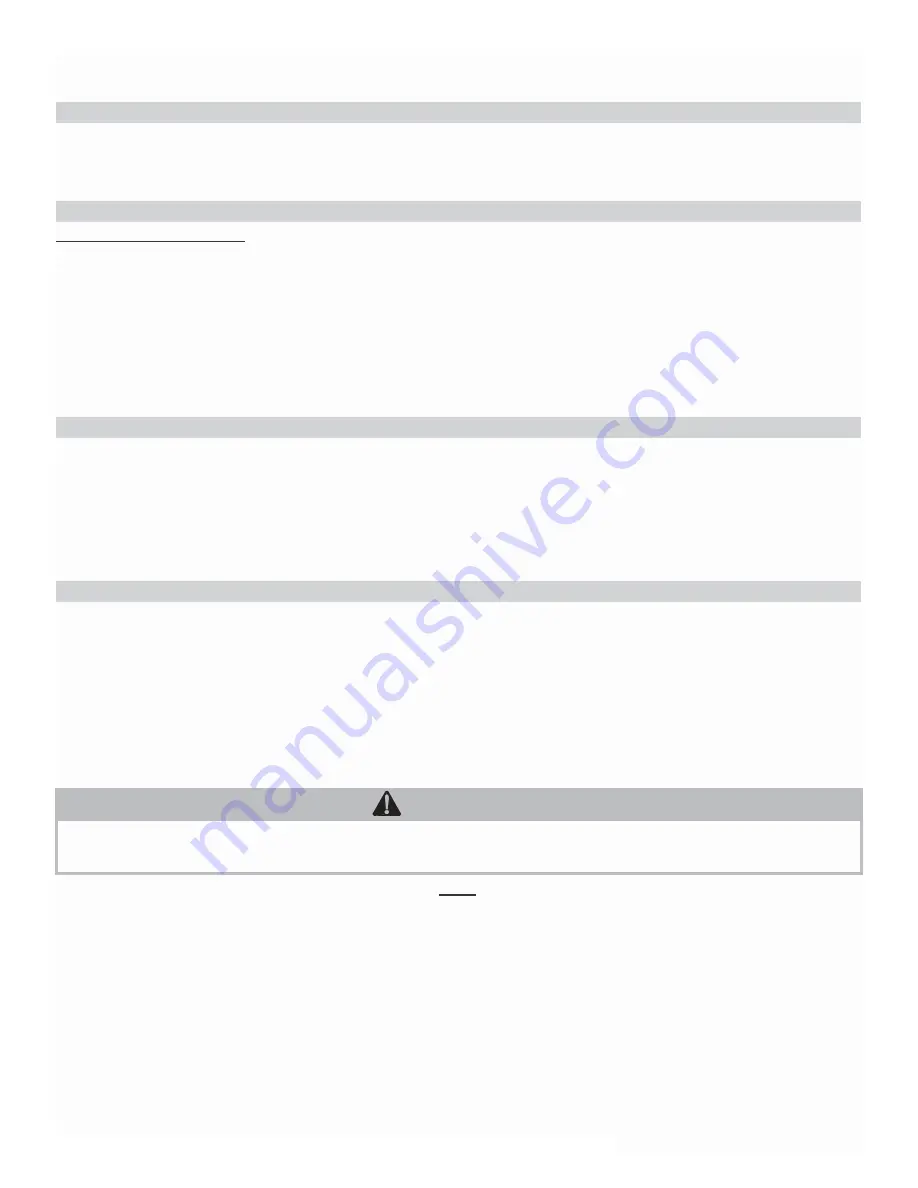
12)
It is recommended that you use one of the mentioned vent kits specifically for Voyager installations; either KGAVT0501CVT
(2 in.), KGAVT0601CVT (3 in.), or V1000.
CLEANER / CEMENT
Cement for all venting must be ALL PURPOSE Cement, and must conform to ASTM D-2235, D-2564 and F-493, and cleaner for the
piping and fittings must conform to ASTM F-656. For joining ABS to PVC, you must use transition green cement listed by NSF and
IAPMO and exceeds ASTM D-3138 to make solid liquid tight joints and gas tight joints.
APPROVEDVENTINGMATERIALS
Exhaust Vent and Extensions in Plastic 2", 3" and 4" Pipe Schedule 40 or 80.
1.
Non Foam Core PVC Pipe
2.
Non Foam Core CPVC Pipe
3.
Non Foam Core ABS Pipe
Vent Piping must conform to following
1.
PVC
Non Foam Core Pipe (Polyvinyl Chloride) to ASTM D-1785 or D-1784 Class 12454-B, Formerly designated Type 1,
Grade 1.
2.
CPVC
(Chlorinated Polyvinyl Chloride) Class 23447-B, Formerly designated Type IV, Grade 1 conforming to ASTM D-1784.
3.
ABS
(Acrylonitrile-Butadiene-Styrene) Class 3-2-2-2-2 conforming to ASTM D3965.
PIPE / FITTINGS
The first 84" (7’) of exhaust piping, must be of 3" ABS solid only (provided) or CPVC; (
NEVER cellular foam core pipe on exhaust
piping
), and conform to ASTM D-3965 for ABS or ASTM F-441 for CPVC, and fittings to ASTM D2661 & D3311 for ABS and ASTM F-
439 for CPVC, the balance of exhaust piping, and all of intake piping, use standard 3" PVC sch. 40 or 3" ABS schedule 40, conforming
to ASTM D2665, or ABS conforming to ASTM D-3965 & ASTM R-441 for ABS; and fittings conforming to ASTM D-2665 & D331. ABS
may also be used for intake venting as long as pipe conforms to ASTM D3965 & D2661 and fittings meet ASTM D2661 & D3311.
Foam core pipe may be used for the entire intake system providing it conforms to ASTM F-891, and is cemented together using above
materials.
FOR LONGER VENT LENGTHS
All venting must be 3", both intake and exhaust,
NEVER use any piping less than 3", or different size pipe on the intake and
exhaust
. You may use 4" venting on both intake and exhaust, to lower the pressure drop, to provide additional venting length.
It is
imperative when using 4", to follow these instructions very carefully. For longer venting lengths, the first 10’ of both the
intake and exhaust piping are 3". For the intake 10’ of 3" PVC plus one 90 degree or two 45 degree elbows and for the
exhaust 10’ of ABS solid NON FOAM CORE, or CPVC plus one 90 degree or two 45 degree elbows
. Then use a 4" x 3" PVC or
4" x 3" ABS reducing coupling. Then proceed with PVC 4" NON FOAM CORE pipe and fittings for both the intake and exhaust piping.
On 4" piping you may go an additional 125 equivalent feet of pipe and fittings, combined total length. The 4" fittings have a friction loss
allowance as follows:
4" 90 degree = 3’ , and a 4" 45 degree = 1’.
The total maximum venting length can be 125’, plus the first
10’ of each 3", and a maximum fitting allowance of the 3", total two 90 degree or four 45 degree before increasing to 4". Total
equivalent would be 30’ of 3" plus 125’ of 4".
WARNING
Never use different pipe sizes for intake and exhaust. The vent system
must be balanced by
friction loss equivalent.
NOTE:
THE METHODS DESCRIBED ARE SUGGESTED GENERIC METHODS ONLY. SPECIFIC JOB SITE OBSERVATIONS AND SIZ-
ING MAY REQUIRE ALTERNATE INSTALLATION METHODS. CONSULT THE FACTORY WITH SPECIFIC JOB REQUIRE-
MENTS FOR ADDITIONAL RECOMMENDATIONS.
PAGE: 7
Summary of Contents for ANSI Z 21.10.3
Page 2: ...PAGE 2 ...
Page 12: ...PAGE 12 ...
Page 15: ...PAGE 15 ...
Page 16: ...PAGE 16 ...
Page 17: ...PAGE 17 ...
Page 18: ...PAGE 18 ...
Page 19: ...PAGE 19 ...
Page 21: ...PAGE 21 Figure 3 A Direct Vent Terminal Clearances per ANSI Z21 10 3 2004 CSA 4 3 2004 ...
Page 22: ...PAGE 22 ...
Page 23: ...PAGE 23 ...
Page 24: ...PAGE 24 ...
Page 25: ...PAGE 25 ...
Page 26: ...PAGE 26 ...
Page 30: ...PAGE 30 PARTS ILLUSTRATIONS ...
Page 40: ...PAGE 40 ...