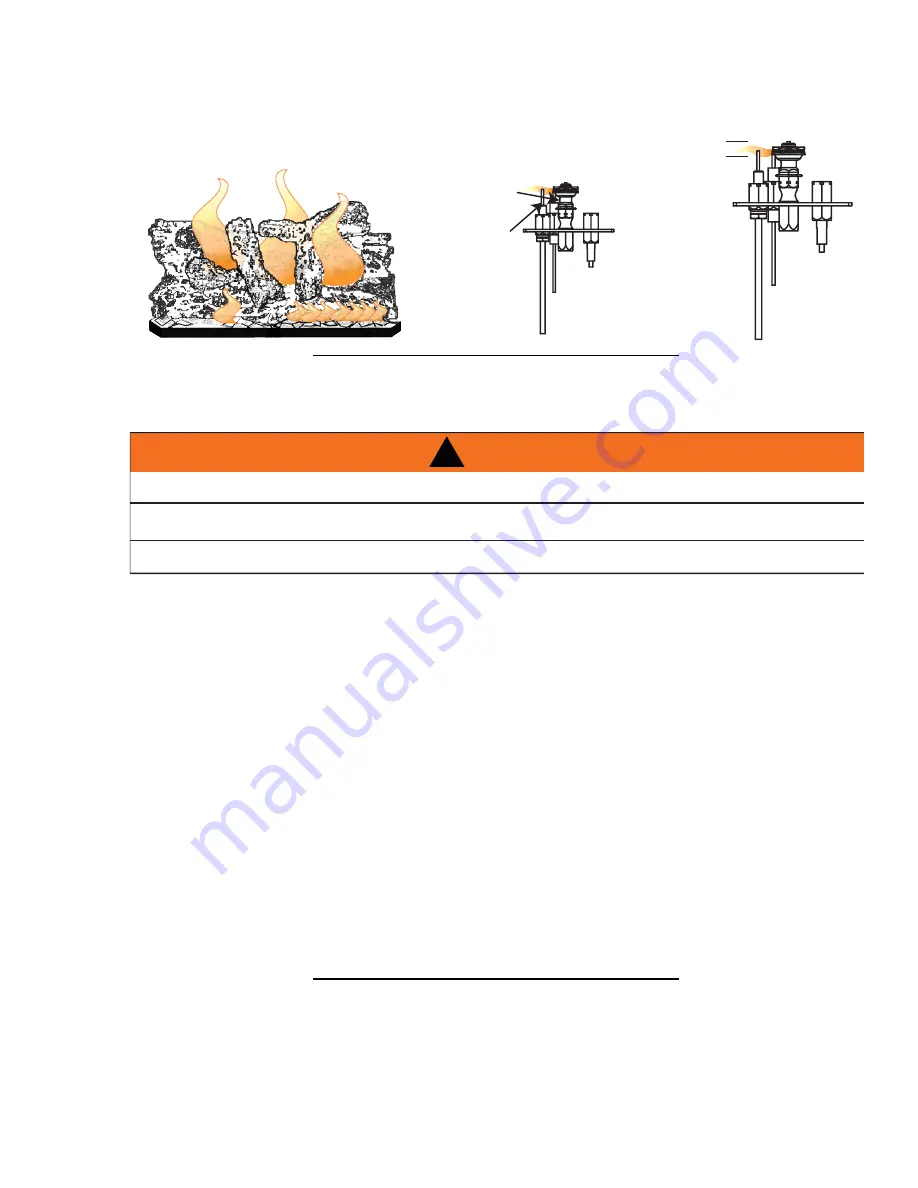
35
W415-0098 / E / 06.28.10
7.3 FLAME
CHARACTERISTICS
It’s important to periodically perform a visual check of the pilot and burner
fl
ames. Compare them to the illustra-
tions provided. If any
fl
ames appear abnormal call a service person.
3/8” - 1/2”
PILOT
BURNER
FLAME MUST ENVELOP
UPPER 3/8” TO 1/2” OF
FLAME SENSOR
FLAME
SENSOR
ELECTRODE
54.1
8.0 MAINTENANCE
CAUTION:
Label all wires prior to disconnection when servicing controls. Wiring errors can cause improper
and dangerous operation. Verify proper operation after servicing. This appliance and its venting system
should be inspected before use and at least annually by a quali
fi
ed service person. The appliance area must
be kept clear and free of combustible materials, gasoline or other
fl
ammable vapors and liquids. The
fl
ow of
combustion and ventilation air must not be obstructed.
1.
In order to properly clean the burner and pilot assembly, remove the logs, rocks and/or glass to
expose both assemblies.
2.
Keep the control compartment, media, burner, air shutter opening and the area surrounding the logs
clean by vacuuming or brushing, at least once a year.
3.
Check to see that all burner ports are burning. Clean out any of the ports which may not be burning or
are not burning properly.
4.
Check to see that the pilot
fl
ame is large enough to engulf the
fl
ame sensor and/or thermocouple /
thermopile as well as reaches the burner.
5.
Replace the cleaned logs, rocks or glass. Failure to properly position the media may cause carboning
which can be distributed in the surrounding living area.
6.
Check to see that the main burner ignites completely on all openings when turned on. A 5 to 10
second total light-up period is satisfactory. If ignition takes longer, consult your local authorized dealer /
distributor.
7.
Check that the gasketing on the sides, top and bottom of the door is not broken or missing. Replace if
necessary.
8.
If for any reason the vent air intake system is disassembled, re-install and re-seal per the instructions
provided for the initial installation.
40.1
MAINTENANCE
MAINTENANCE
MAINTENANCE
TURN OFF THE GAS AND ELECTRICAL POWER BEFORE SERVICING THE APPLIANCE.
APPLIANCE MAY BE HOT, DO NOT SERVICE UNTIL APPLIANCE HAS COOLED.
DO NOT USE ABRASIVE CLEANERS.
!
WARNING
Due to the high temperature that the hinges experience, wet lubricants such as oil and WD40 will cause the
hinges to seize and are therefore not suitable. Lubricate with a high temperature dry graphite, only.