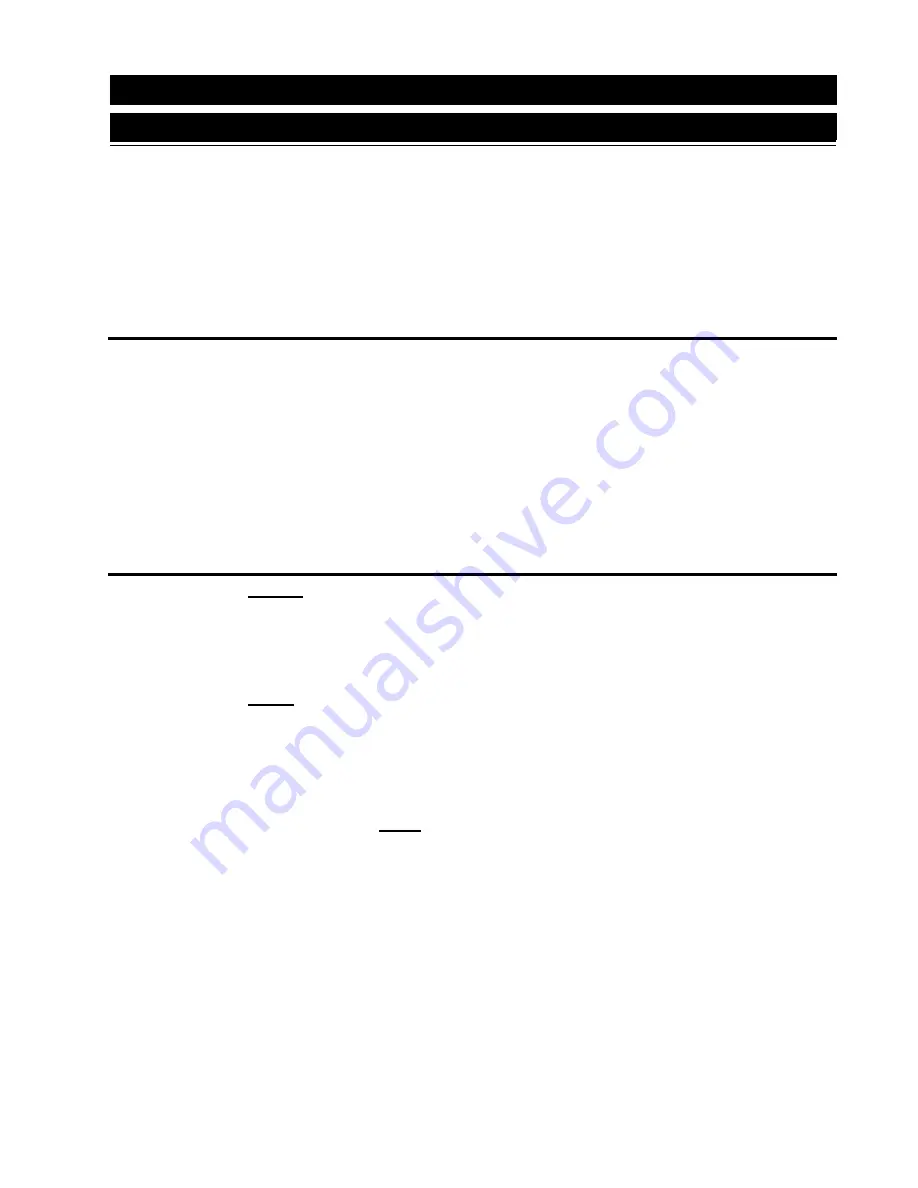
W415-0616 / C / 06.04.08
41
TROUBLESHOOTING CONTINUED
SYMPTOM
Feed rate dial has
no effect on the
fi re (timer control
only)
The convection
blower is not
functioning nor-
mally
The heater will
not operate when
hot
TEST SOLUTION
- Secure all connections to the power control module.
- Perform a resistance test to the potentiometer by placing the two test leads
from a multi meter into the leads of the potentiometer. The potentiometer should have a
range of 850 KΩ (± 10%).
Potentiometer
Readings:
Full counter-clockwise (switched off) = open circuit, overload or infi nite
resistance
Low fi re .......... 900 KΩ to 1,050 KΩ
High fi re ......... 56 KΩ to 62 KΩ
If the range is not close or does not vary then replace the potentiometer.
- Using the wiring diagram, compare all the connections between the controller, switch,
and the convection blower.
- If the convection motor will not run, apply 115V AC to the motor directly. Replace the
blower controller if the motor runs. The convection blower has failed if the motor does
not run. Replace the blower.
- If the convection blower runs on high at all times (no control with the blower controller),
check the connections from the 160°F (71°C) sensor (located on the upper left side on
the rear of the fi re wall) and convection blower controller to the blower. Disconnect one
of the wires from the sensor and if control of the convection blower returns to the
blower controller, replace the sensor.
- If the motor is still on high, re-connect the sensor and replace the convection blower
controller.
General
- Check the hopper for fuel.
- Incorrect air damper setting may cause excessive air to consume the fi re too quickly
before the next drop of fuel. Therefore leaving the fuel completely unburned in the burn
pot and will cause the fuel to burn cold and very slowly. Fuel also may build up and
smother the fi re.
NOTE:
The unit may require a change to the vent system or installation of fresh air to
correct air to fuel ratio problems.
- Combustion blower failure may occur because it is not turning fast enough to generate
the proper vacuum in the fi re box. Do a visual check to see if the motor is turning.
- Check vacuum levels in the exhaust channel by bypassing the vacuum switch, then
remove the vacuum hose from vacuum switch. When checking the vacuum exhaust
place the open end of the vacuum hose on the gauge (readings must be above 0.10"
W.C. on low fi re).
(NOTE: if the motor fails to reach a 0.10" W.C., then replace the
combustion blower).
- Poor quality fuel may not produce enough heat to keep the stove burning or
operational.
- If the exhaust temperature sensor fails try bypassing the sensor located on the exhaust
blower. If the stove operates properly, the unit may require cleaning or a new sensor.
Contact your local deal for service.
- Unplug the stove, open the left side panel and jump the two brown leads that are
attached to the 140°F (60°C) temperature sensor. If the stove operates replace the
140°F (60°C) sensor.
Summary of Contents for Auburn NPS40
Page 1: ...W415 0616 C 06 04 08 1 10 00 W415 0616 C 06 04 08...
Page 4: ...W415 0616 C 06 04 08 4 WARNINGS AND SAFETY PRECAUTIONS...
Page 5: ...W415 0616 C 06 04 08 5 WARNINGS AND SAFETY PRECAUTIONS...
Page 33: ...W415 0616 C 06 04 08 33 Figure 49 NORMAL OPERATING SOUNDS...
Page 34: ...W415 0616 C 06 04 08 34 WIRING DIAGRAM Figure 51...
Page 36: ...W415 0616 C 06 04 08 36 COMMON REPLACEMENTS PARTS...
Page 38: ...W415 0616 C 06 04 08 38 NPI40 REPLACEMENTS PARTS...
Page 39: ...W415 0616 C 06 04 08 39 NPI40 ACCESSORY PARTS COMMON ACCESSORY PARTS...
Page 44: ...W415 0616 C 06 04 08 44 NOTES...