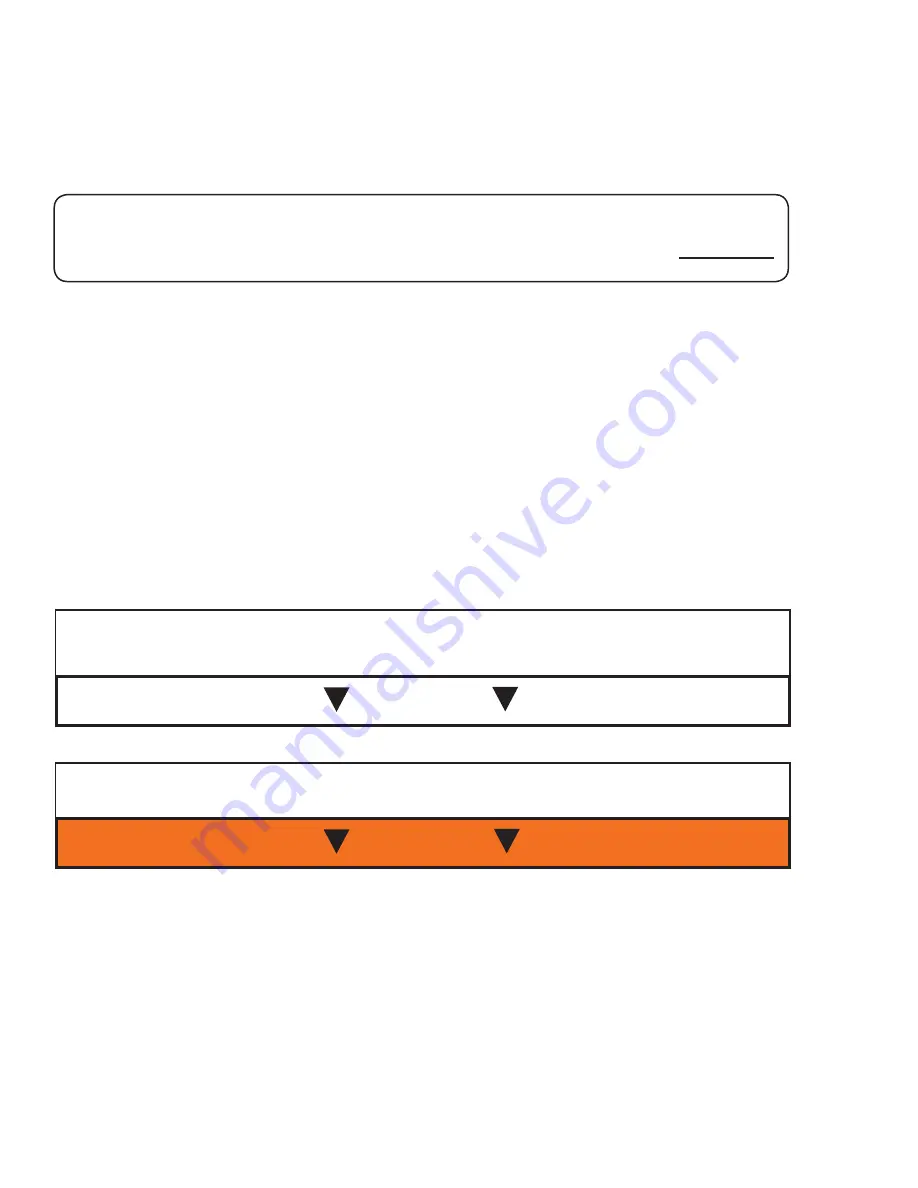
W415-0919 / D / 03.27.13
1 3
ALW
AYS DISCONNECT THE ELECTRICAL
SUPPLY
TO
THE FURNACE BEFORE REMOVING
THE BURNER COMPARTMENT
ACCESS DOOR.
THE FURNACE GAS TRAIN IS DESIGNED
TO
OPERATE
AS A
SEALED UNIT . BE SURE
THAT
THE BURNER COMP
ARTMENT
ACCESS DOOR IS PROPERL
Y IN PLACE BEFORE
ATTEMPTING T
O REST
ART
THE FURNACE.
CAUTION
!
!
The furnace achieves its high effi
ciency in three general areas. First, there is no wasteful standing pilot. The
furnace consumes no gas in between cycles. Secondly, the furnace is designed to allow very small amounts of
excess air in the combustion process. Older furnaces had heat exchangers which were commonly 40% larger
than necessary for complete combustion. While this prevented the creation of carbon monoxide, the heated
excess air was expelled up the chimney where it could not benefi
t the interior of the home. Special safety
controls now prevent the formation of carbon monoxide.
The third general area is the recovery of the latent heat contained in the fl
ue gas, which is comprised of water
vapor and carbon dioxide. By condensing the fl
ue gas in the furnace recovery coil, heat that would otherwise be
wasted to the outdoors, is captured and redirected into the duct system where it contributes to home comfort.
Each pound of condensation formed releases approximately 970 Btu’s.
Y our furnace may condense up to ½
gallon (5 pounds) of water per hour if running continuously.
This condensation must be properly disposed into a sump or drainage system. The condensate lines must
remain clear and free fl
owing. Do not allow plastic drain lines to become pinched or kinked. A
blocked drain
line can cause the furnace to operate erratically, or not at all.
WARNING
!
!
7.
Match up the blower rails with the hangers on the underside of the blower division panel, then slide the
blower assembly back into position.
8.
Replace the screws fastening the blower assembly to the blower division panel.
9.
Secure harnesses to blower division and junction box. Connect thermostat wiring to the control board.
10. Replace the blower access door
.
11.
Restore electrical power to the furnace.
12. Routine cleaning of the interior of the recovery coil should not be necessary
. If evidence develops indicating that
a cleaning is necessary , it should be done by a trained and quali
fi ed service technician. Evidence may include
large amounts of dirt or debris building up in the condensate drain line.
IMPORTANT
:
Your furnace should be cleaned and inspected annually by a trained and quali
fi ed
service
technician. Y
our service technician has the knowledge and test equipment to determine the
condition of your furnace.