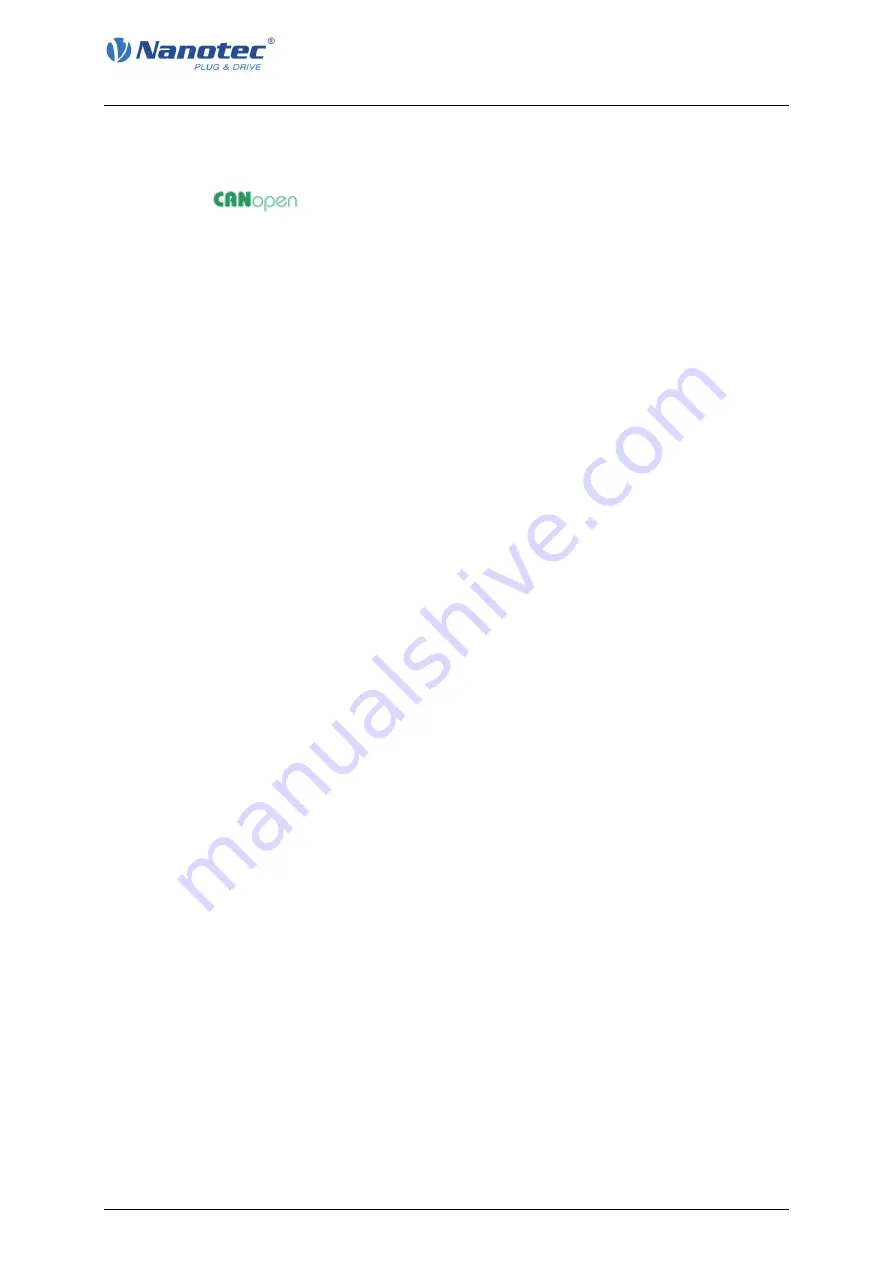
Technical
Manual
PD4-N5918
Overview
Issue: V 1.4
7
Activation via CANopen
It is possible to include the stepper motor control in a CANopen environment with the
PD4-N. The connection can be established either via 2 wires of the I/O connection
cable or in a customer-specific version also via an M12 connector (5-pole).
More detailed information on this can be found in the CANopen reference and in the
NanoCAN user manual.
In addition, the Plug & Drive motor via CANopen has another safety function: Even
when the voltage supply of the PD4-N is interrupted, the processor continues to be
supplied with power via the communication line and the position data cannot be lost so
that the machine does not need to be referenced after being switched on.
Settings
The operating behavior of the motor can be set and optimized according to individual
requirements by setting the motor-related parameters. The parameters can be set
using the NanoPro or NanoCAN software and significantly reduce commissioning
time.
More detailed information on this can be found in the separate NanoPro or NanoCAN
user manual.
Rotation monitoring
Even if stepper motors do not lose steps during normal operation, the integrated
speed control provides additional security in all operating modes, e.g. against motor
stalling or other external sources of error. The monitoring function detects a stalled
motor or step loss after tenth of a step at the most (for 1.8° stepper motors with 500
pulses/rotation).
Automatic error correction is possible after the drive profile is ended or during the
drive.