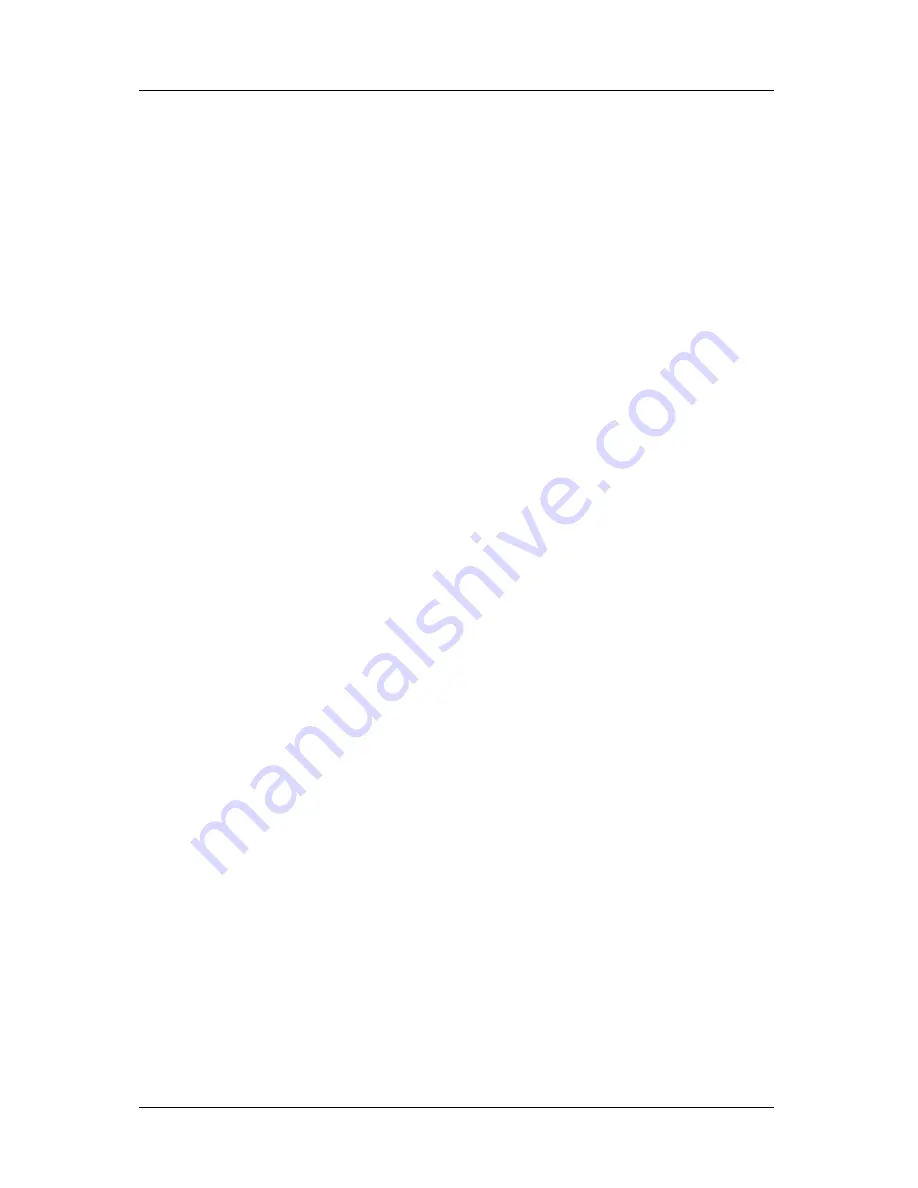
AB2 Driver Box User Manual
AB2 Operation
15
3.1.2.1 Enabling the Step Mode
Enable the Step operation mode, by shorting pin 16 to the ground.
3.1.3 Gate Mode Operation
In Gate Mode, as opposed to Step Mode the pulse width and pulse frequency
are user-defined. The driver output to the motor is turned on and off in time
intervals defined by an external switching signal.
The amplitude of the output corresponds to the analog command input value and
thus determines the speed of the motor.
The allowable parameter values for the external signal are as follows:
•
Voltage levels: 0V-on; 5V-off. Open collector logic is also optional.
•
Minimum pulse width: 50 µsec.
•
Maximum pulse frequency: 1 kHz.
3.1.3.1 Enabling the Gate Mode
Enable the Gate mode of operation by shorting pin 8 to the ground. Verify that
pin 16 is not shorted to the ground at the same time. Once pin 8 is shorted, the
driver is in Gate Mode. The external signal should now be conducted through pin
16.
3.1.4 DC Mode Operation
When operating in the DC mode, the driver enables the motor to converge to
10nm and less. The travel available in this mode is 300 nm from the point
reached by the motor while operating in the regular Velocity (AC) mode.
As shown in Figure 9, the position is a linear function of the command voltage,
with certain hysteresis; some asymmetry is normal and expected.
Summary of Contents for AB2
Page 2: ......