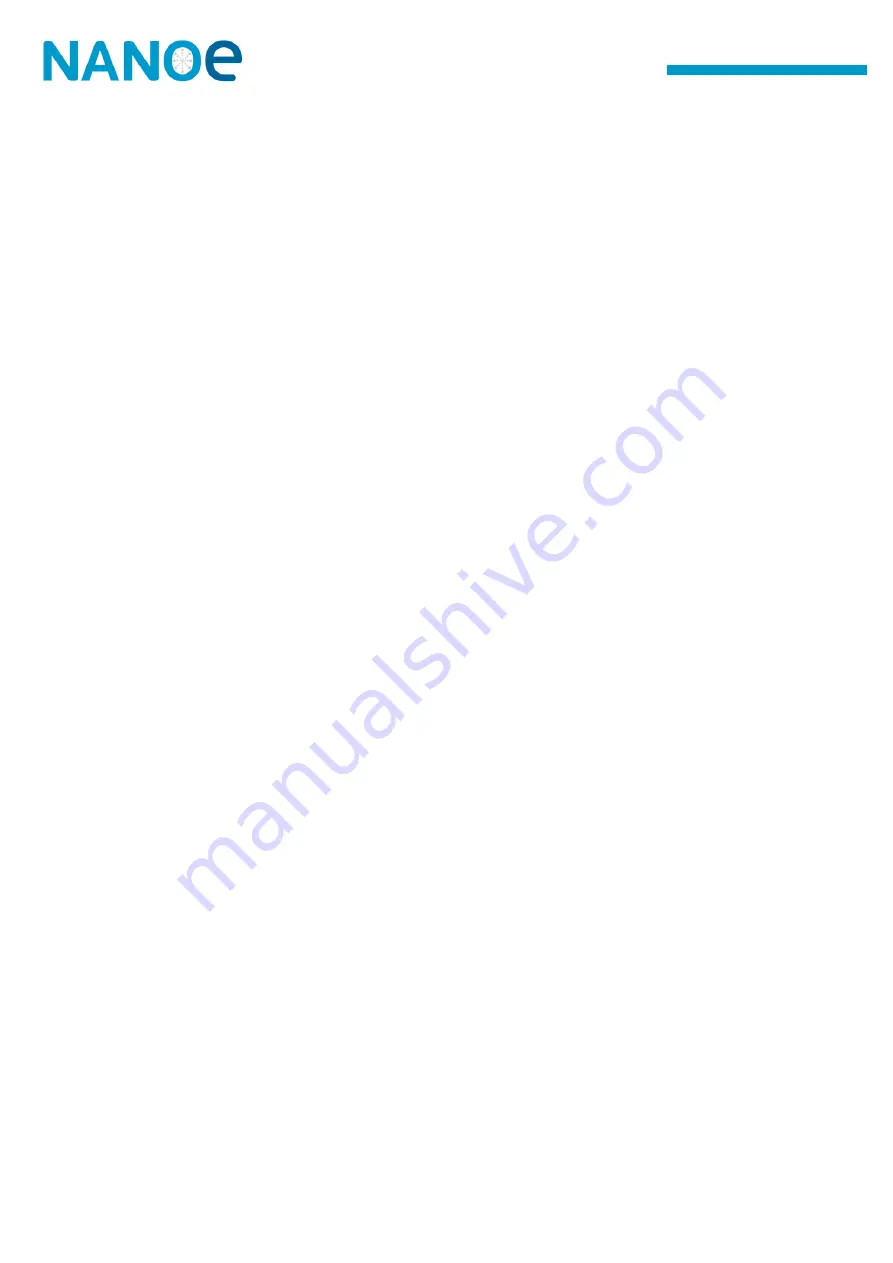
2
Zetasinter System
®
Content
1.
Furnace Description ..................................................................................................................................... 3
2.
Technical Specifications ............................................................................................................................... 3
3.
Safety ........................................................................................................................................................... 4
a.
Intended use
b.
Assembling
c.
Operation
d.
Maintenance
4.
Assembling................................................................................................................................................... 7
5.
Temperature controller ............................................................................................................................... 9
6.
Alumina tube and refractory blocks .......................................................................................................... 14
7. Vacuum pump & flowmeter ....................................................................................................................... 19
8.
Bubbler
…………………………………………………………………………………………………………………
..
…………………………
..
…
..
…
21
9.
MoSi2 Heating elements
……………………………………………………………………………………………………………………………
. 22
10. Troubleshooting ....................................................................................................................................... 23
11. Electrical schematic diagram .................................................................................................................... 25
12. Quick start procedure .............................................................................................................................. 26
13. EU Declaration of conformity (No 2018-11-a) ......................................................................................... 27