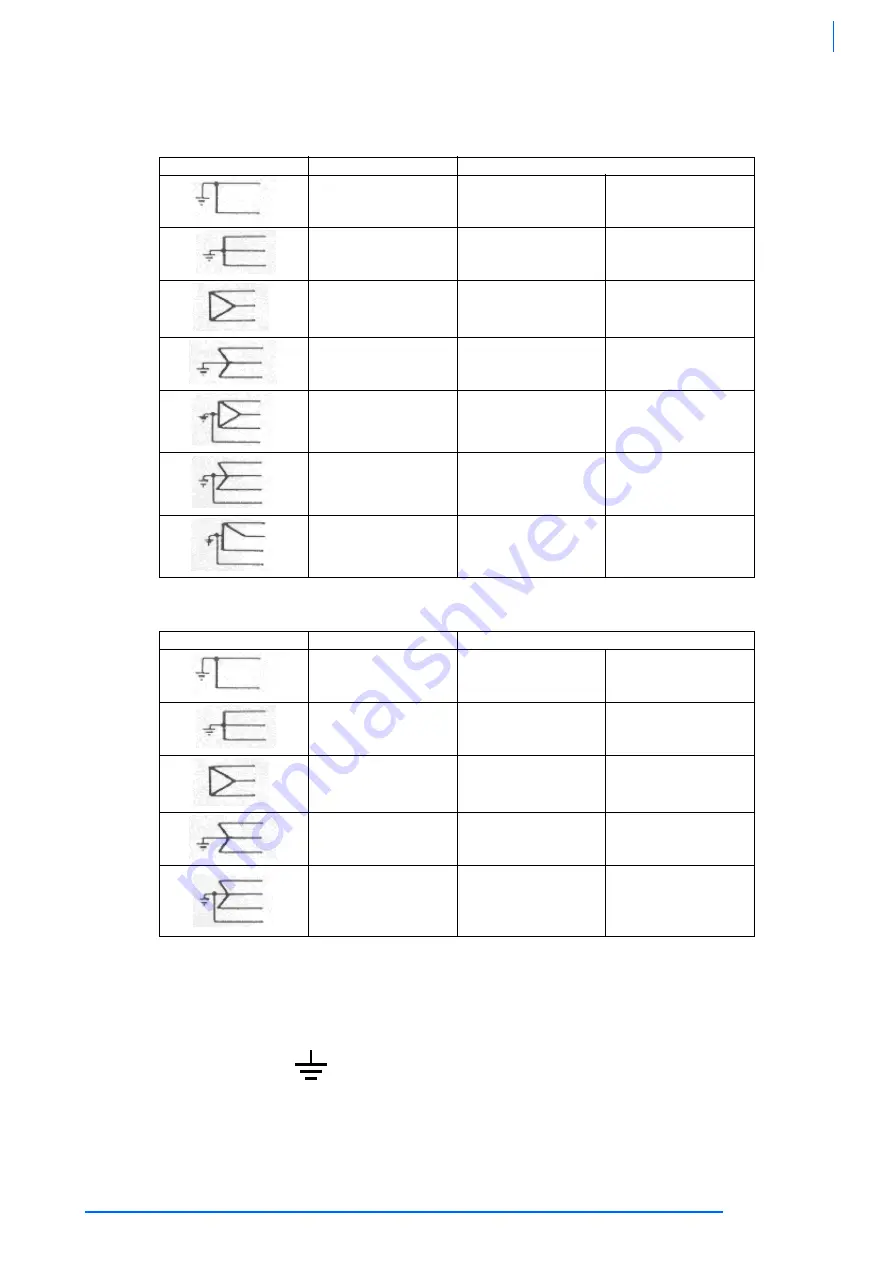
9
OPERATING AND MAINTENANCE MANUAL
Chapter 5
- Installation
NRC0020-0200 UL
The data in this manual are not binding and may be changed by the manufacturer without notice.
Reproduction of this manual, even partial, is strictly prohibited.
5 . 3
E l e c t r i c a l c o n n e c t i o n s
The unit's connection to the power supply must be made in compliance with laws and prescriptions in force in the place of installation, after
having consulted the electrical diagram supplied with the unit.
The voltage, frequency and number of phases must comply with the data on the unit's dataplate.
Main distribution systems in the USA:
Main distribution systems in Canada:
For the electrical power supply:
1.
To access the electrical panel, remove the lateral screws fixing the top cover to the side panels of the cabinet and remove the front
panel by undoing the screws securing the panel to the base.
To access the electrical panel components undo the nuts fixing its protective cover to the front panel.
2.
Connect the unit (terminal
in the electrical panel) to the electrical earthing system of the building;
3.
Make sure the level of protection against indirect contact at the source of the power feeding cable is equivalent at least toNEMA
Type 1;
4.
At the start of the power feeding cable or the power cable supplied with the unit install a device that protects the cable from
overcurrent (short circuits) (refer to the indications in the electrical diagram)
All protection devices must be approved (“listed”) for this purpose.
System
Rated Voltage
User voltage
120
115
110
240/120
230/115
220/110
600
480
240
575
460
230
550
440
220
480
460
440
480/277
208/120
460/266
200/115
440/254
190/110
240/120
230/115
220/110
240/120
230/115
220/110
System
Rated Voltage
User voltage
240
480
600
230
460
575
220
440
550
240/120
230/115
220/110
600
480
240
575
460
230
550
440
220
600
480
240
575
460
230
550
440
220
600/347
480/277
416*/240
208/120
575/332
460/266
400*/230
200/115
550/318
440/254
380*/220
190/110
Summary of Contents for NRC0020-0200 UL
Page 2: ......