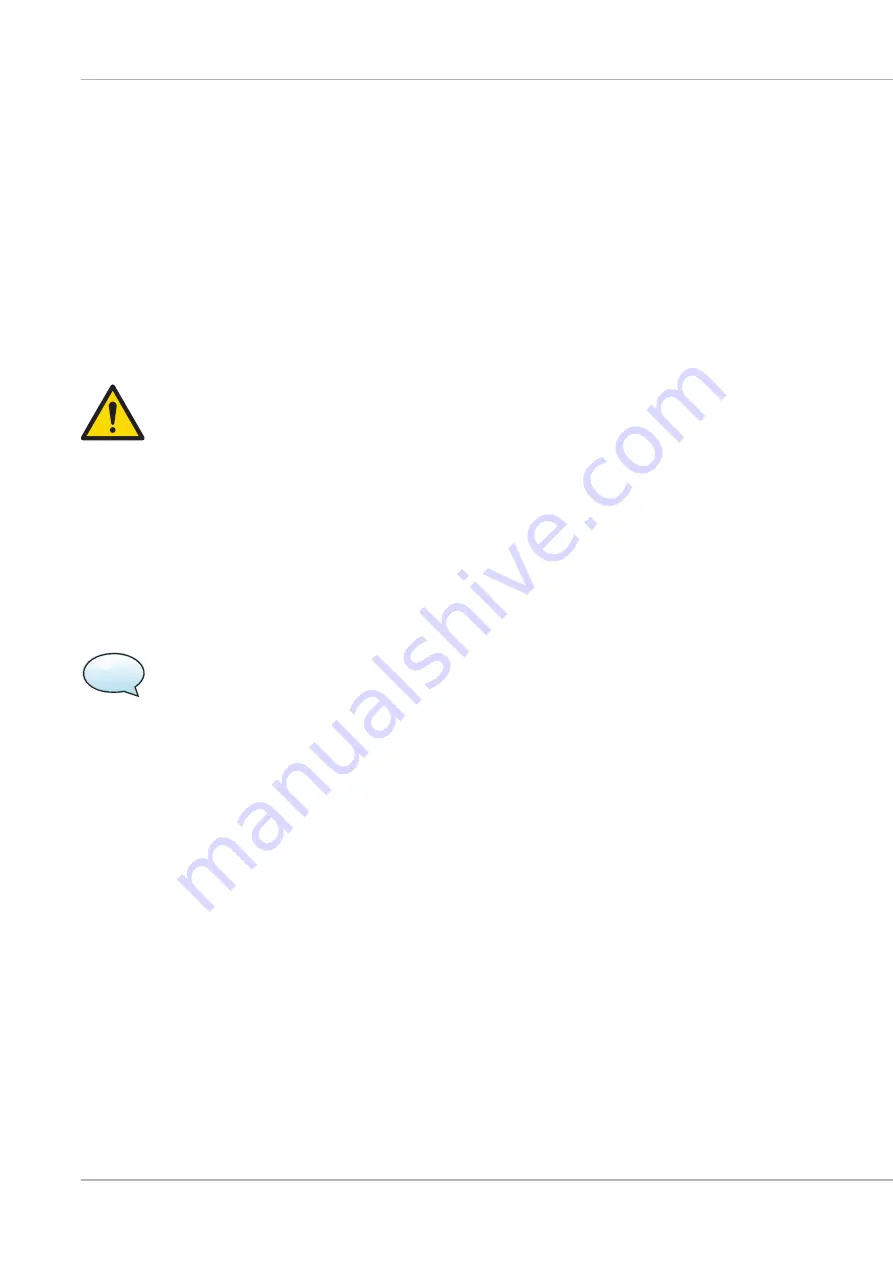
Page 4
17-110 -0143
2. General safety
2.1 Intended use of the Product
The generator is exclusively intended for the production of Nitrogen gas from compressed air, which is free
from bulk water, oil and solid matter constituents.
The product should be sited within a building (see section 7.1 Site selection). The generator must be operated
only in accordance with the data on the rating label and in accordance with the contractual conditions. Any
operations that do not comply with those stated on the product rating label will render the warranty void.
No modifications must be made to the product. Any modifications may reduce the operational safety of the
product and invalidate the manufacturer’s warranty, potentially resulting in damage to the product and serious
personal injury.
For your own safety, when carrying out work on this product, all relevant national safety regulations
must be complied with relating to pressurized and electrical systems.
This product is only designed to operate at pressures of between 87 - 145 (6 - 10barg) or
232 psig (16 barg) dependant on the generator model.
2.2 Personnel
Only authorized, competent and trained personnel are permitted to work on the product. This user guide is
intended solely for such personnel and is to be used only as a reference; it should not be used to replace
conventional training.
2.3 Safe handling
Please ensure that relevant safe engineering practices and handling procedures are employed when handling,
installing and operating the product.
Ensure that the equipment is depressurized and electrically isolated, prior
to carrying out any of the scheduled maintenance instructions specified within this user guide.
A suitable lifting aid must be used to minimize the risk of physical injury or damage to the
product.
Summary of Contents for GEN2-1110
Page 1: ...GEN2 NITROGEN GENERATOR USER GUIDE...
Page 26: ...Page 26 17 110 0143 Notes...
Page 27: ...Page 27 17 110 0143 Notes...