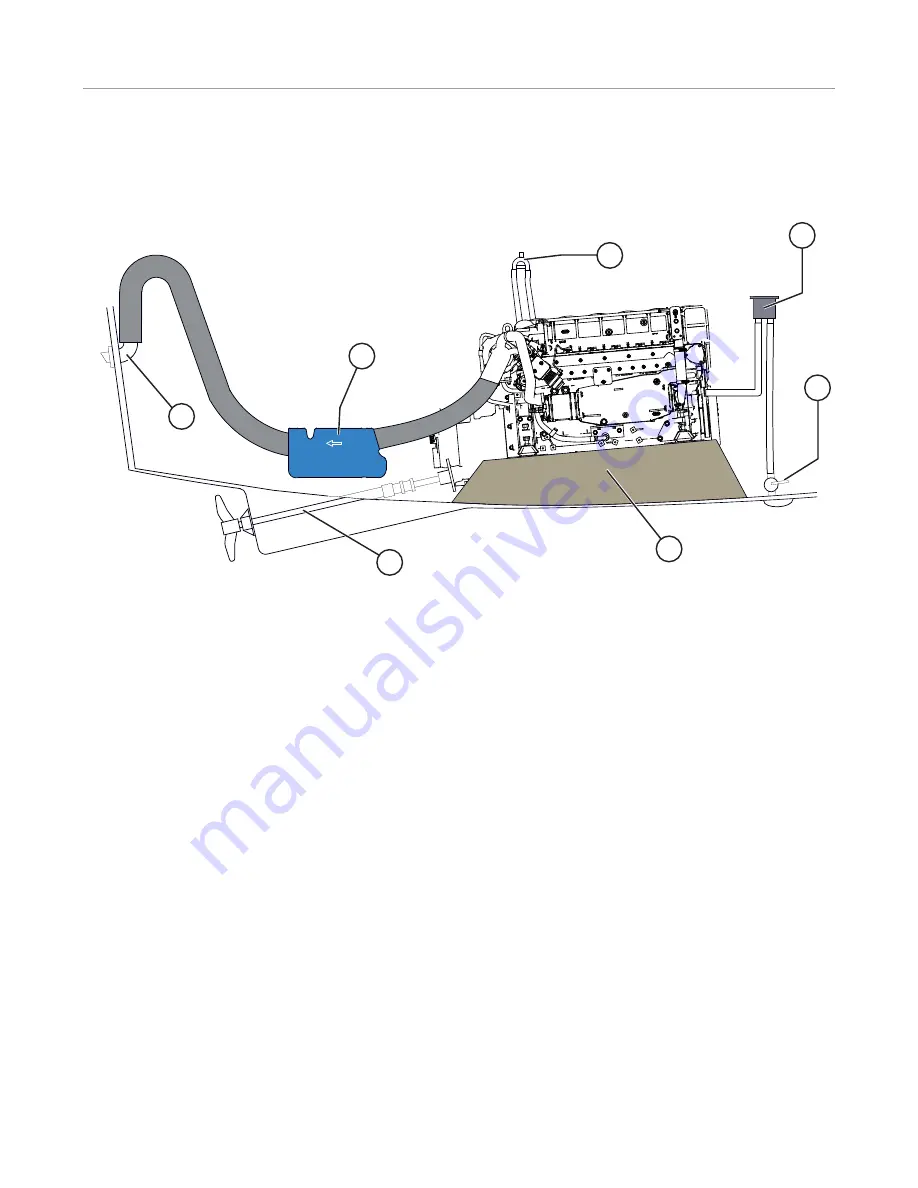
11
Presentation
Installation inspection
I
Attention! :
Your engine must be installed by an authorised shipyard or a qualifi ed Nanni Industries representative in
accordance with the on board assembly instructions. However, you can check some important points on the installation
of the engine.
1. Engine frame
The engine frame must be solid and able to absorb all the
dynamic stress as well as the weight of the engine. It must
be connected to the hull by an area as large as possible.
The engine must not be at an angle of more than 15° when
the boat is stopped.
2. Propeller shaft
The choice of propulsion system must be made according
to the restrictions arising from the engine, the boat, and the
use of the boat.
3. Waterlock exhaust box
The waterlock must be positioned as close to the engine
and as low as possible.
4. Hull outlet
The hull outlet must be located 15cm below the water line.
The tube between the exhaust box and the hull outlet must
form a swan-neck shape to avoid any water getting into the
exhaust system through the hull outlet.
5. Anti-siphon valve
Mandatory on boats whose engine is below the waterline.
The anti-siphon valve must be installed at the end of the
seawater system before injection in the exhaust elbow and
must be positioned above the waterline, between 0.5 and
2 metres.
6. Seawater filter
This must always be positioned at least 15 cm above the
waterline.
7. Through-hull valve
On yachts and boats that do not go above 12 knots, the
water inlet must be turned towards the end of the boat.
On motor boats that go over 12 knots, the water inlet must
be turned forwards the end of the boat.
Engine room
The temperature inside the engine compartment must not
exceed 50°C with a maximum difference of 20°C with the
outside temperature.
Slow boats must have a ventilator fitted. Fresh air from the
front is circulated from front to back. The front air intake is
located low down at the front of the engine compartment
and the outlet high at the back for optimum air circulation.
Electrical installation
An incorrect or faulty electrical installation can cause
leakage currents that can affect the galvanic protection of
the engine and damage the engine subsequently.
The installer must ensure to take all necessary precautions
to protect the engine against corrosion.
4
3
5
6
2
1
7