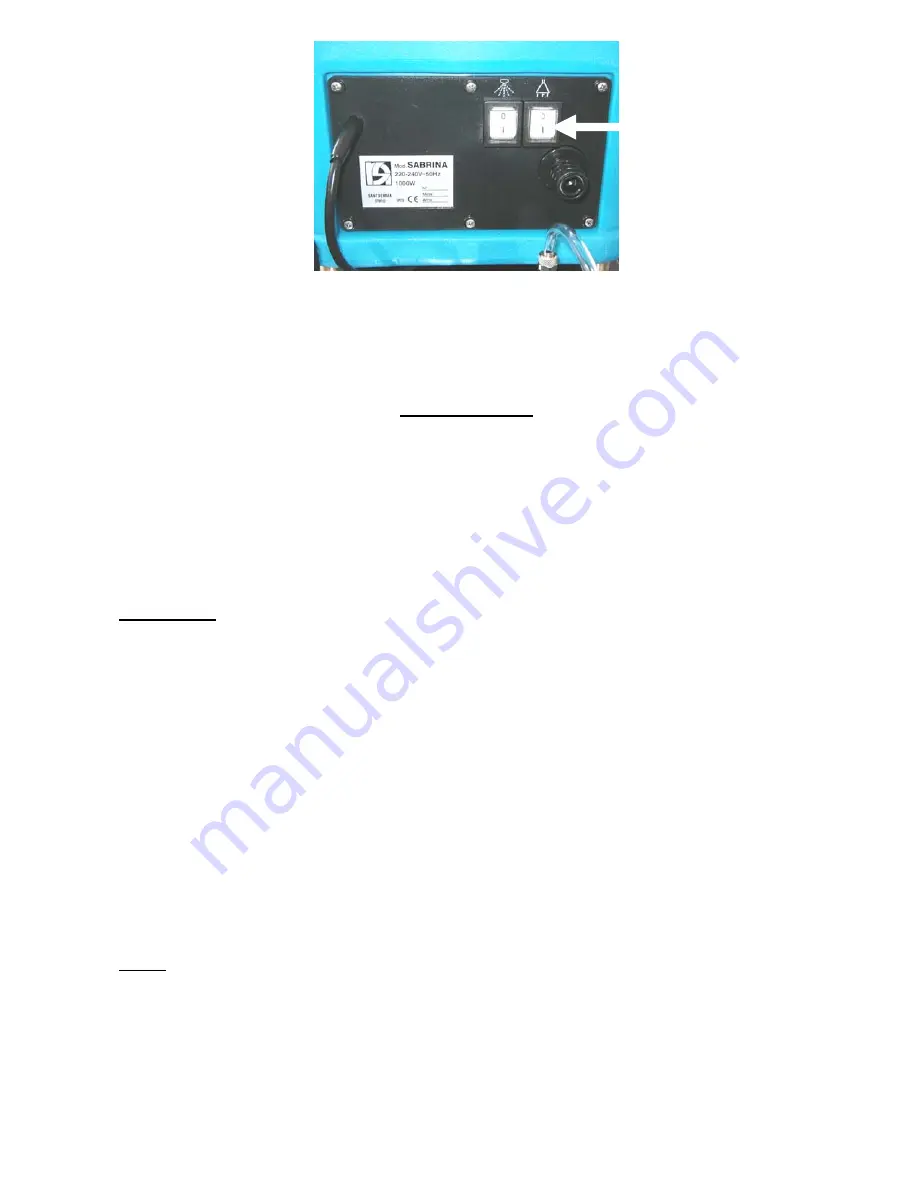
6
9. Switch on the vacuum motor.
At this point the machine is ready for work. The optimal working air pressure is 4 bars. The
air pressure is indicated on the air pressure gauge on the regulation panel.
Working method
1. In order to spray foam, pull the lever on the foam brush accessory. Spray foam uniformly
on the surface to clean. The ideal thickness of the foam is about ¼”.
2. Let the foam react with the surface for 30 seconds. If necessary, use the brush to agitate
the foam.
ATTENTION:
You only need to spray enough foam to cover the area to be cleaned. Keep in
mind that only the foam that comes in to contact with the surface is cleaning the surface.
3. Vacuum the foam from the surface. It is
mandatory
that you use
defoamer
in the
recovery tank prior to vacuuming the foam. If defoamer is not used, the foam can be
sucked in to the vacuum motor and damage it.
4. While using the machine, if for any reason you should need to switch the compressor on
again using the compressor ON/OFF switch, you must empty the air tank. Otherwise the
compressor may be unable to start, because of the air pressure inside the air tank. To
empty the air tank, spray air only with the foam brush accessory, with both compressor
and pump switched off.
NOTE:
The compressor is provided with a safety thermal protection, which intervenes to
protect it from an overheating. If the compressor stops suddenly, when the pressure or the
air has not yet reached its set value, then it can be due to an overheating. If this happens,
check that the voltage supplied to the machine corresponds to the value indicated on the
label and that the set point for the air pressure is not too high. Switch the compressor off,
empty the air tank and wait approx. 10 minutes before switching the compressor on.