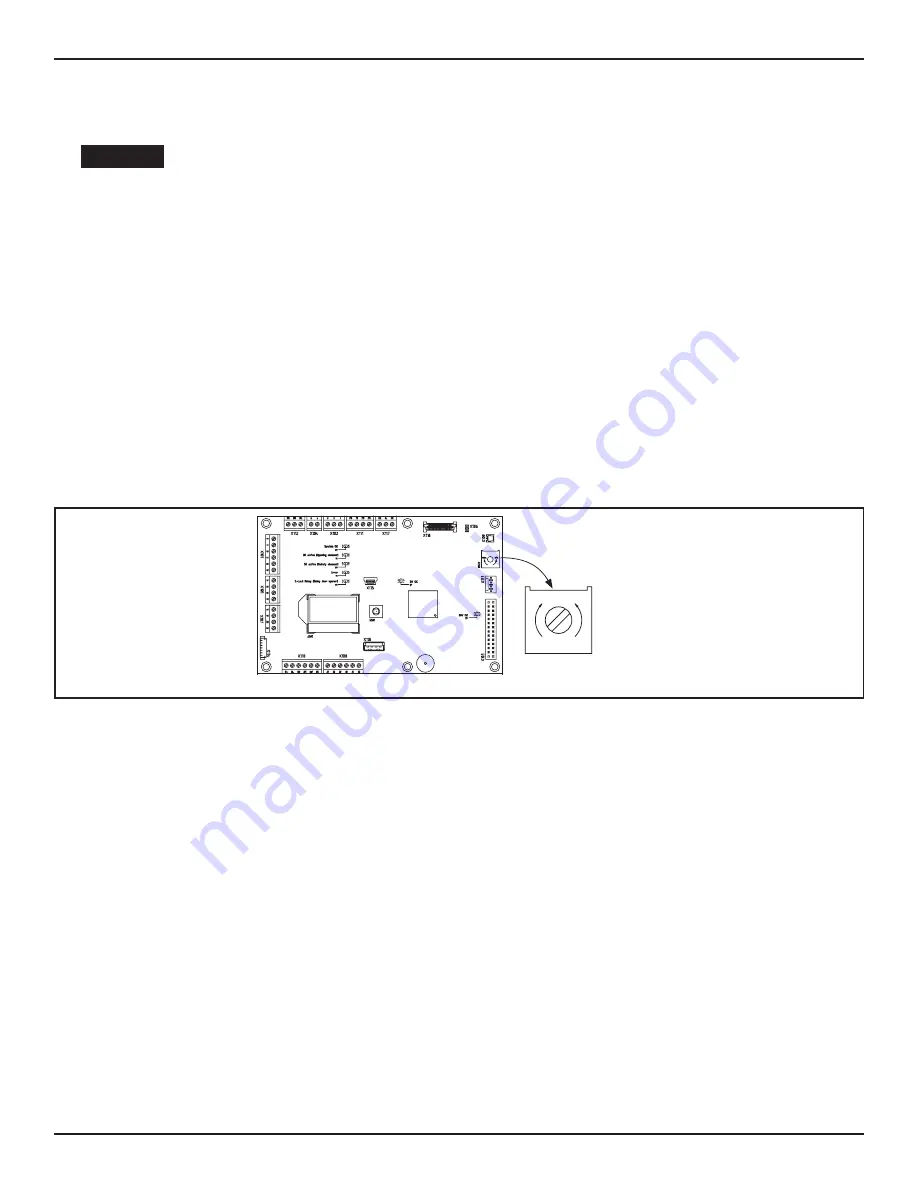
26 of 34
GT20 8300-8350 Overhead Concealed Operator Installation Manual
www.NabcoEntrances.com
P/N C-00183
Rev 8-31-16
SECTION 13 .2 FSLAM POTENTIOMETER (POWER OFF)
• Only adjust the Cam when absolutely necessary .
• During a Power Failure or when Power is turned OFF, ONLY adjust the Cam if the FSlam
Potentiometer will not close the Door after repeated adjustment attempts have been made .
The Cam can be adjusted to vary the angle where the slam function will start .
Note: The FSlam Potentiometer is utilized for Standard Application only (not Inverse Application).
When Power is OFF or during Manual Mode, the Motor slows the Door Panel down to a constant closing speed until the Full Closed
position is reached and the Door Panel is locked. This is done by utilizing the FSlam potentiometer (accelerated force). To ensure the
FSlam parameter setting is correct:
1. Open the door Panel 90 degrees, then let it go.
a. If the Door Panel fails to fully close and then lock, adjustments are deemed necessary.
1.►Go to the GT20 Control.
2.►Go to either side of the GT20 Control to locate a Blue square.
a. Exact location Depends upon the type of installation.
3.►With a flat head screwdriver turn the Potentiometer:
X
Clockwise for maximum accelerated force.
X
Counterclockwise for minimum accelerated force.
DN 1175
FSlam Poten ometer
Adjuster
max. min.
Figure 42 Adjust Closing Force
SECTION 13 .3 Adjust the Activation Angle
Note: By default, the FSlam Angle (from the Fully Closed Position) is approximately 5 degrees.
1. Carefully pry the Service Cover from the gearbox housing with a flathead screwdriver.
2. Locate the Cam Disk.
a. The Locking Screw may be positioned under Cam Setting 1 or Cam Setting 2.
3. Slightly loosen the Locking Screw with a 1.5mm socket wrench.
4. According to Table 8, turn the Cam Disk clockwise or counterclockwise to adjust the Angle.
a. Angle range is between 5 degrees - 15 degrees.
5. Tighten the Locking Screw.
6. Open the Door Panel 45 degrees, then let it go.
X
If the Door Panel locks:
•► Snap the Service Cover back onto the Gearbox Housing.
X
If the Door Panel fails to lock:
•► Repeat steps 1 - 5 accordingly.
CAUTION