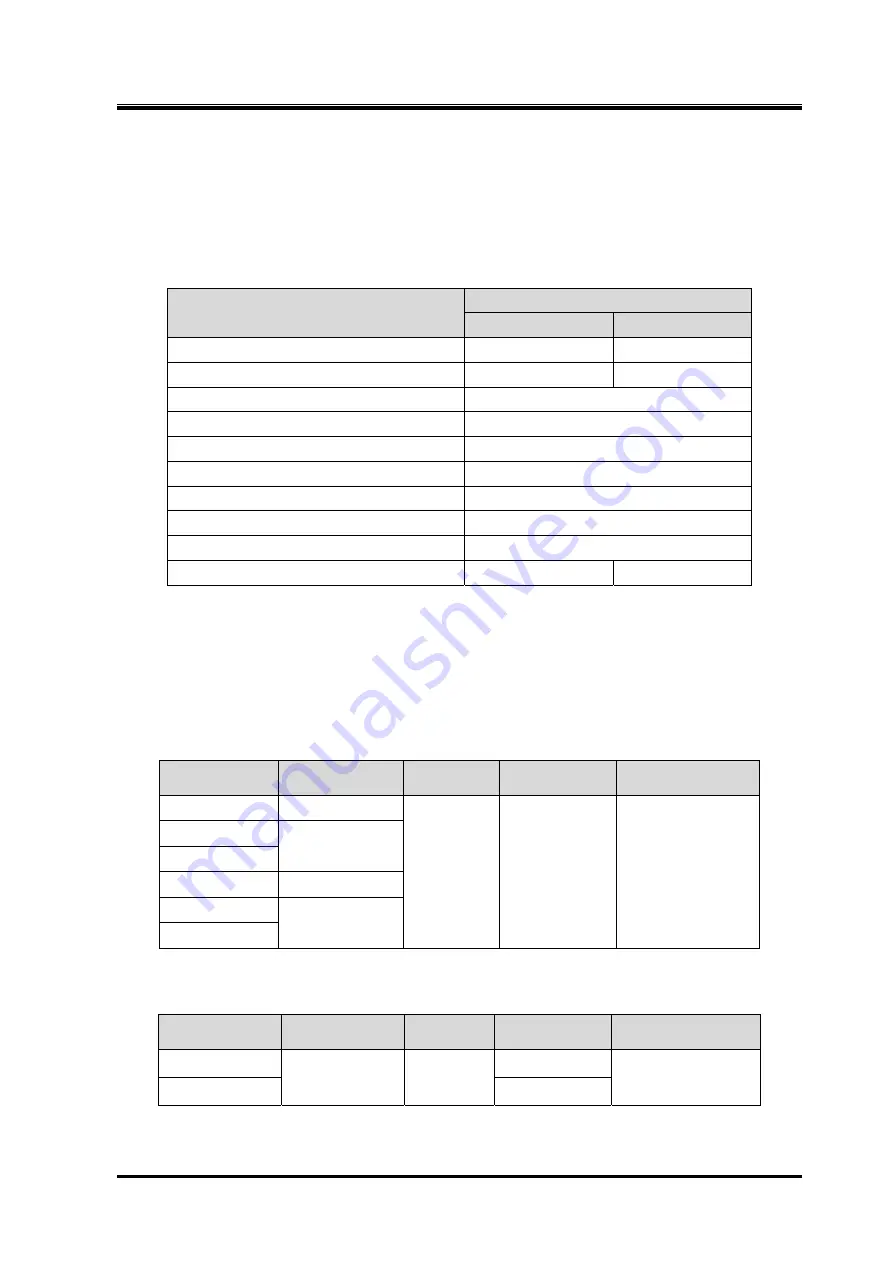
2205B0JE-DA-J-N_2014.05.
2 Structure and Specifications of the Compressor
Screw Compressor J-series
2.9 Solenoid Valve
2-31
2.9 Solenoid
Valve
2.9.1 170J/220J-Series
The 170J/220J-series are provided with solenoid valve assemblies for capacity and variable Vi control.
Table 2-4 Specifications of the Solenoid Valves
Item
Type
SBL5B-4BL
SXL6-4BL
Maximum working differential pressure
1.6 MPa
2.1 MPa
Minimum working differential pressure
0.0 MPa
0.0 MPa
Operation fluid
Lubricant (Refrigerant oil)
Fluid temperature
100°C or less
Ambient temperature
-
20—40°C
Maximum working pressure
3.5 MPa (see Note 1)
Maximum working kinematic viscosity
120 mm
2
/s. (see Note 2)
Proof counter pressure (See Note 3)
0.45 MPa (information only)
Maximum flow rate coefficient (Cv value)
0.33—0.35
Applicable standard
UL and CSA
CE
Note 1: This pressure represents the gauge pressure.
Note 2: Proper operation is not possible when the kinematic viscosity of the lubricant is over 120 mm
2
/s.
Note 3:
The proof counter pressure indicates the pressure working against the direction of flow at which
the plunger opens automatically. This control can prevent an abnormally high pressure inside
the cylinder due to liquid enclosing.
Table 2-12 Specifications of the Coil for SBL5B-4BL
Rated voltage
Lead wire color
Frequency
Effective
power
Allowable voltage
fluctuation
100V AC
Black
50/60 Hz
11/9 W
±10%
110V AC
Blue
120V AC
200V AC
Red
220V AC
Blue
240V AC
Table 2-13 Specifications of the Coil for SXL6-4BL
Rated voltage
Lead wire color Frequency Effective power
Allowable voltage
fluctuation
110-127 V AC
Blue 50
Hz
12-19 W
+10—
-
15 %
220-240 V AC
12-15 W