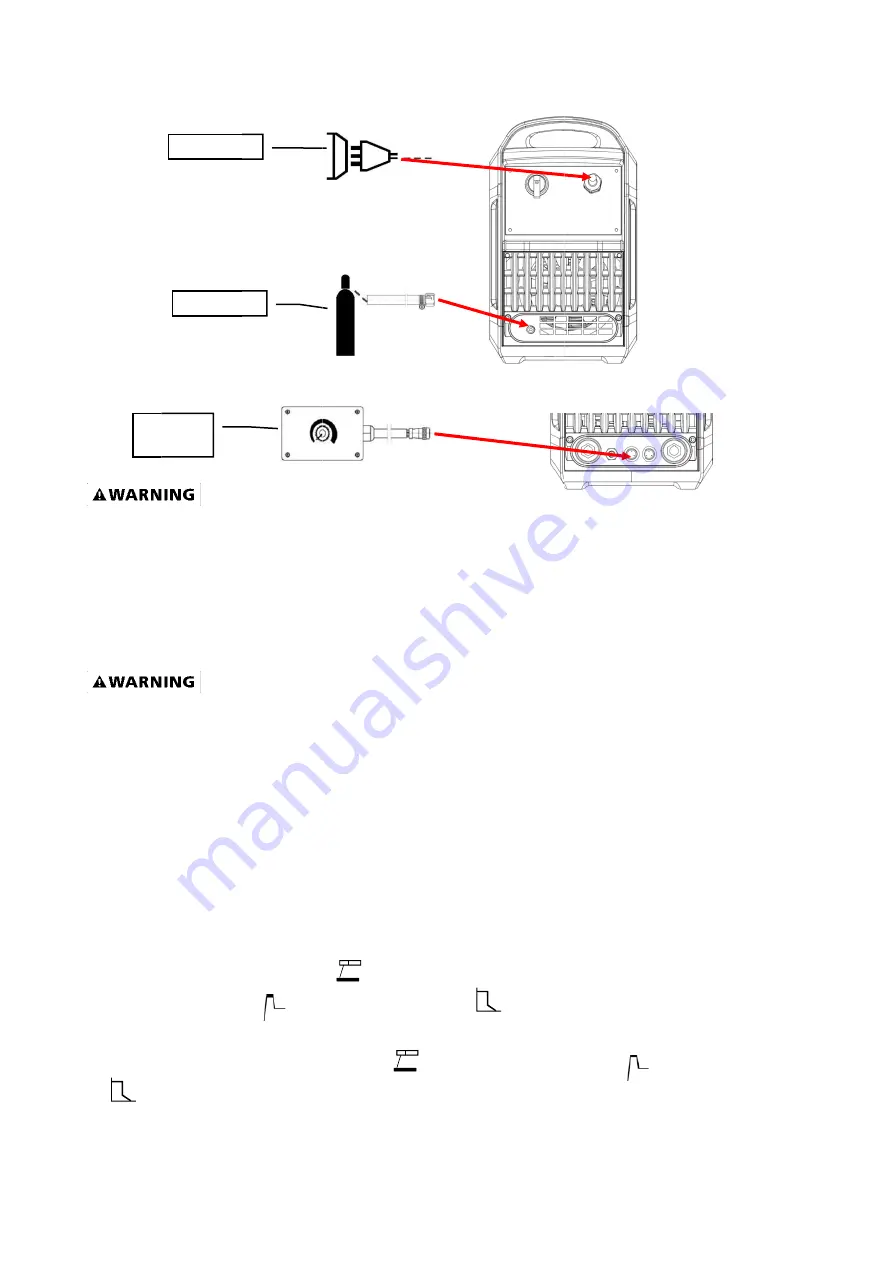
5. Input co
6. Foot cont
EXPO
Prolonged
begin weld
sleeved sh
OPERATI
High
installation
protect the
have it che
any way a
receptacle
properly g
1. MMA: D
Set the
【
W
The hot st
the weldin
NOTICE
:
“
”
ca
Remo
cont
onnection m
trol pedal
OSURE TO
d exposure
ding until yo
hirt, trouser
ION
voltage d
n of recept
e operator f
ecked by a
and do not
e. Make sur
rounded 22
C Stick arc
Welding mod
tart current
ng materials
If set
【
Wel
an be adjust
Input powe
Gas cylind
ote
trol box
method
A WELDIN
to the weld
ou are adeq
rs without c
danger from
tacle at the
from electri
qualified e
use any a
re the POW
20 VAC, 60
c welding
de knob
】
to
“
”
an
.
lding mode k
ted.
er
der
NG ARC IS
ding arc ca
quately pro
cuffs, high t
m power
e power so
ical shock.
lectrician. D
dapter betw
WER switch
HZ, single
o “
”
,
adj
d arc force c
knob
】
to “
11
S EXTREME
an cause bl
tected. Wea
topped sho
source! Co
urce. This
If you are n
Do not cut
ween the w
h is OFF th
phase, 50 a
ust the
【
Ad
current
“
”
,
just the
ELY HARM
lindness an
ar flame-pro
oes, and an
onsult a q
welder mu
not sure if y
off the grou
welder's pow
en connect
amp power
djustment kn
”
can be
e hot start cu
MFUL TO TH
nd burns. N
oof welding
ANSI appro
qualified e
ust be grou
your outlet
unding pro
wer cord a
t your weld
source.
ob
】
to chan
adjusted at
urrent
“
HE EYES A
Never strike
g gloves, a
oved weldi
electrician
unded while
is properly
ng or alter
and the pow
der's powe
nge the weld
t this mode a
”
and arc fo
AND SKIN!
e an arc or
heavy long
ng helmet.
for proper
e in use to
y grounded,
the plug in
wer source
r cord to a
ding current.
according to
orce current
r
g
r
o
,
n
e
a
.
o
t
Summary of Contents for WAVE 200DIII
Page 25: ...25 ...