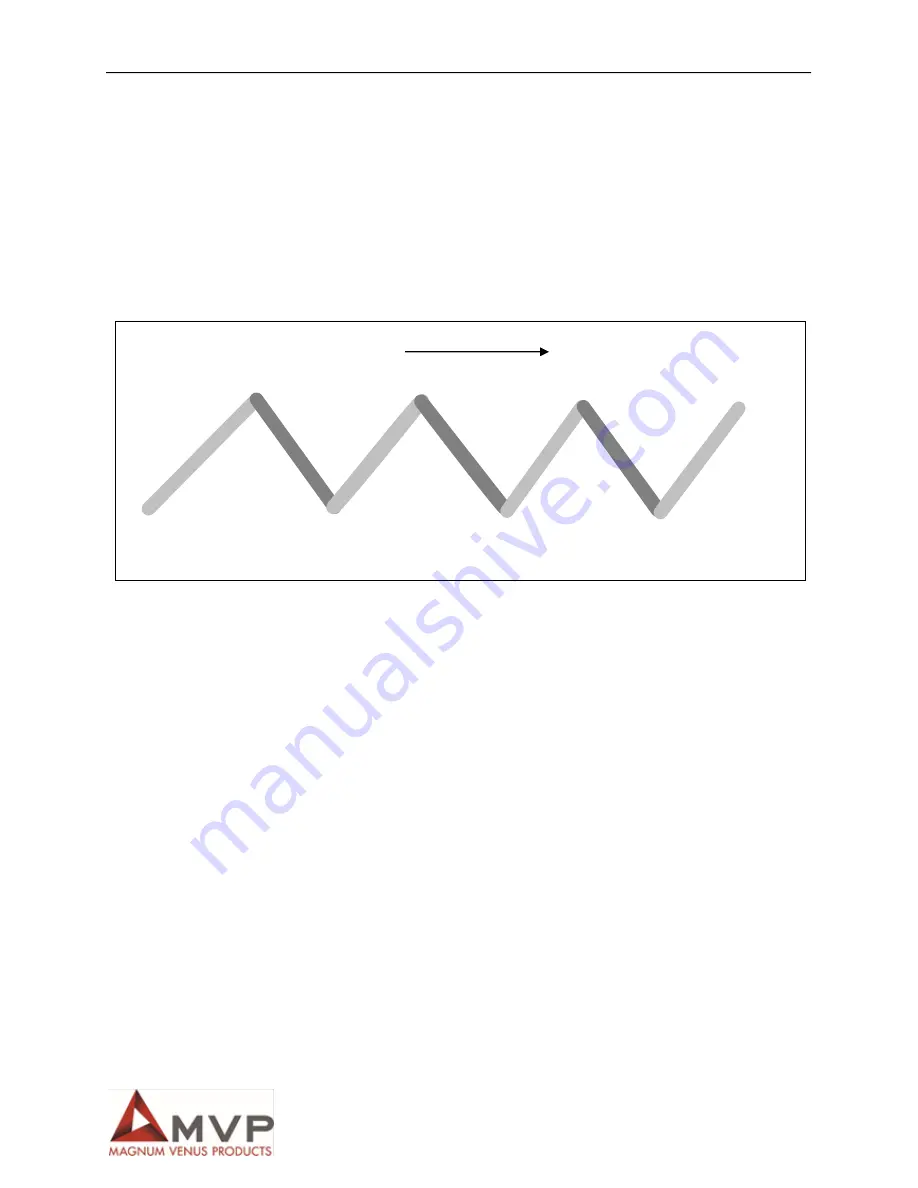
Patriot 1:1 Adhesive System Operations Manual
Rev. 07/2016
Page | 31
Result 1:
Material delivered on the activator pump down-stroke (from the top of the stroke to the bottom) is not
curing or slow cure (see figure above).
Indicates:
No or low activator is being delivered on the down-stroke.
Probable Cause:
Worn or damaged intake valve.
Worn or damaged lower seat.
Dirty or stuck intake valve.
Solution:
Replace
worn and damaged parts, see
Service and Repair Manual.
Result 2:
Material delivered on the activator pump up-stroke (from the bottom of the stroke to the top) is not curing
or slow cure (see figure above).
Indicates:
No or low activator is being delivered on the up-stroke.
Probable Cause:
Worn or damaged piston seal
Worn or damaged piston body ball.
Damaged piston body ball seat.
Solution:
Replace worn and damaged parts, see
Service and Repair Manual.
Start Pour Test
Direction of gun travel
End Pour Test
B
B
B
B
T
T
T
Summary of Contents for PATRIOT 1:1
Page 1: ...Rev 07 2016 PATRIOT 1 1 ADHESIVE UNIT Operations Manual ...
Page 38: ...Patriot 1 1 Adhesive System Operations Manual Rev 07 2016 Page 38 ...
Page 39: ...Patriot 1 1 Adhesive System Operations Manual Rev 07 2016 Page 39 ...
Page 40: ...Patriot 1 1 Adhesive System Operations Manual Rev 07 2016 Page 40 ...
Page 41: ...Patriot 1 1 Adhesive System Operations Manual Rev 07 2016 Page 41 ...
Page 42: ...Patriot 1 1 Adhesive System Operations Manual Rev 07 2016 Page 42 ...
Page 43: ...Patriot 1 1 Adhesive System Operations Manual Rev 07 2016 Page 43 ...
Page 44: ...Patriot 1 1 Adhesive System Operations Manual Rev 07 2016 Page 44 ...
Page 45: ...Patriot 1 1 Adhesive System Operations Manual Rev 07 2016 Page 45 ...
Page 46: ...Patriot 1 1 Adhesive System Operations Manual Rev 07 2016 Page 46 ...
Page 47: ...Patriot 1 1 Adhesive System Operations Manual Rev 07 2016 Page 47 ...
Page 48: ...Patriot 1 1 Adhesive System Operations Manual Rev 07 2016 Page 48 ...
Page 49: ...Patriot 1 1 Adhesive System Operations Manual Rev 07 2016 Page 49 ...
Page 50: ...Patriot 1 1 Adhesive System Operations Manual Rev 07 2016 Page 50 ...
Page 51: ...Patriot 1 1 Adhesive System Operations Manual Rev 07 2016 Page 51 ...
Page 52: ...Patriot 1 1 Adhesive System Operations Manual Rev 07 2016 Page 52 ...
Page 53: ...Patriot 1 1 Adhesive System Operations Manual Rev 07 2016 Page 53 ...
Page 54: ...Patriot 1 1 Adhesive System Operations Manual Rev 07 2016 Page 54 ...
Page 55: ...Patriot 1 1 Adhesive System Operations Manual Rev 07 2016 Page 55 ...
Page 56: ...Patriot 1 1 Adhesive System Operations Manual Rev 07 2016 Page 56 ...
Page 57: ...Patriot 1 1 Adhesive System Operations Manual Rev 07 2016 Page 57 ...
Page 58: ...Patriot 1 1 Adhesive System Operations Manual Rev 07 2016 Page 58 ...
Page 59: ...Patriot 1 1 Adhesive System Operations Manual Rev 07 2016 Page 59 ...
Page 60: ...Patriot 1 1 Adhesive System Operations Manual Rev 07 2016 Page 60 ...
Page 61: ...Patriot 1 1 Adhesive System Operations Manual Rev 07 2016 Page 61 ...
Page 63: ...Patriot 1 1 Adhesive System Operations Manual Rev 07 2016 Page 63 ...